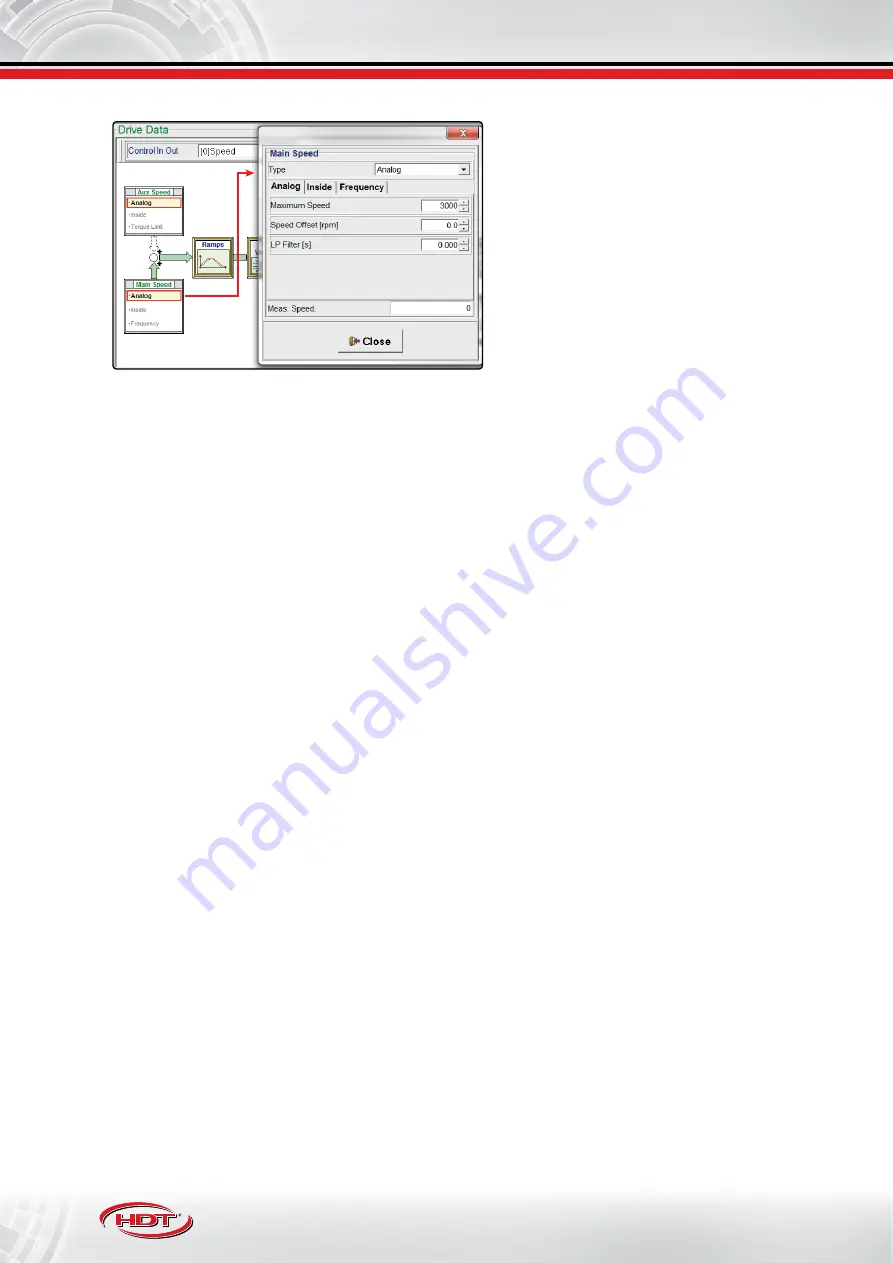
88
Installation and user guide
Rev: 4.0
NTT 240/460
Operation mode
Analog input setting, related to a speed control, is shown in picture below:
Parameters to set are:
• maximum absolute value for reachable speed
(back and forth operation) when analog input
voltage value matches with ±10V scale value
(example: ±3000RPM).
• speed offset useful to compensate any external
signal offset.
• a low pass digital filter on external signal.
Information about istantaneous measured speed
appears.
6.09.2 Auxiliary references
Auxiliary reference AUX1/IN9
provides following features:
•
speed control
as auxiliary speed reference.
•
speed control
as torque limit reference.
•
position control
as analog position reference, if ‘analog positioner’ is used.
•
pressure control
as analog/inside pressure reference.
Topologies are shown below:
1.
Analog IN9
: reference is feeded from external signal, whose voltage range lies between ±10V. Drive input is
a differential port (pin 3-4 of J9 connector).
•
In auxiliary speed control
, this signal is added to main speed reference and parameters to set are
maximum reachable speed (in absolute value) when analog input voltage value matches with ±10V
scale value (example: ±3000RPM).
•
In position control
, setting minimum target position (equivalent -10V) and maximun target position
(equi10V) parameters, drive performs positioning between this two values following the 12 bit
analog auxiliary reference range (±10V).
•
In pressure control
, this signal feeds pressure reference related to settable parameters into press sub-
menu.
2.
Inside
: auxiliary reference is generated internally by drive and it’s constant. By the way, it can be modified
via Caliper software during operation or via fieldbus parameter.
3.
Torque limit
: reference is used in speed control as torque limit value. Reference is feeded from external
signal, whose voltage range lies between ±10V (pin 3-4 of J9 connector). Parameters to set are:
•
absolute torque value to load when analog input voltage value matches with +10V scale value
(example: 100%).
•
torque offset useful to compensate any external signal offset.
Auxiliary reference AUX2/IN10
(pin 5-6 of J9 connector) is available with all operatin modes and and provides
following features:
•
pressure control
as analog/inside speed reference.
Topologies are shown below:
1.
Analog IN10
: pressure transducer feedback is feeded from external signal, whose voltage range lies
between ±10V. Drive input is a differential port (pin 5-6 of J9 connector).
•
In pressure control
, this signal feeds speed reference related to settable parameters into press sub-menu.
2.
Inside
: auxiliary reference is generated internally by drive and it’s constant. By the way, it can be modified
via Caliper software during operation or via fieldbus parameter.
Содержание NTT 240
Страница 129: ......