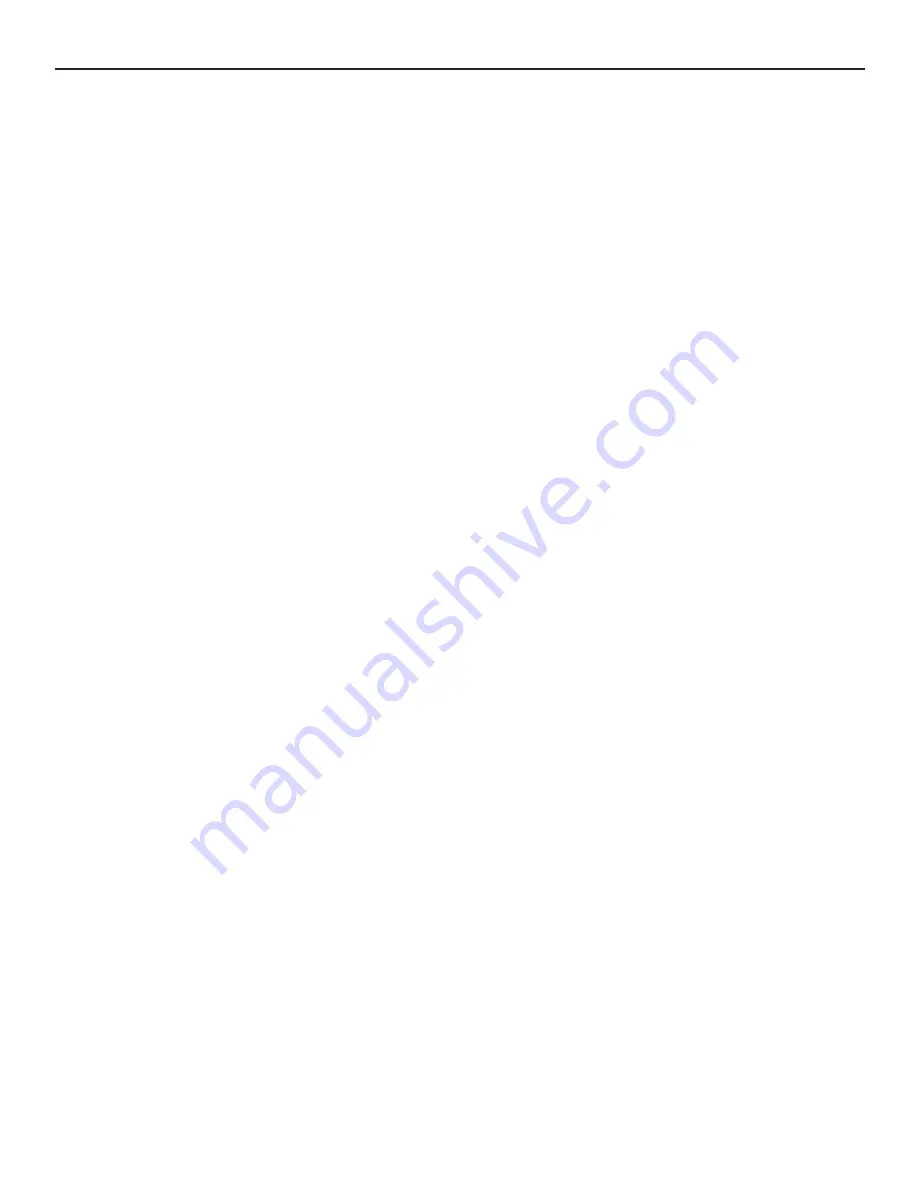
4
APM-001e
AUG 2015
PURGE POINT CONNECTIONS
Foul gas lines from condensers should be purged at points
recommended by the condenser manufacturer. Usually, this
is at the top of each circuit’s outlet header which drains
down through a P-trap to the receiver. In some cases, a
small high pressure auxiliary receiver is located at the
outlet of one or more condensers. This receiver should
have a purge point at the top, preferably at a “dead” area
away from condenser drain pipes. Below is a typical valve
arrangement for a purge point (Figure 3).
Regardless of
the purge point location, it is absolutely necessary to
ensure that liquid is not drawn into the foul gas line.
WATER LINE
The APM has an automatic water bubbler to eliminate any
water bottle attention. Connect the water supply to the
purger water shut-off valve (See Figure 1). Water pressure
should be between 30 and 80 psig (2 and 5 bar). The
factory-installed flow controller limits the amount of water
going into the bubbler.
The transparent tube of the water bubbler may become
coated with mineral deposits after a period of time. These
deposits can be removed by adding a cup of vinegar to the
water in the bubbler and cleaning the clear tube through
the top plastic fitting with the brush supplied. A water
conditioning filter cartridge and housing are available for
abnormally hard water.
DRAIN LINE
A 1” PVC socket water drain connection is located at the
bottom of the bubbler (an alternate 1” FPT threaded adapter
is also supplied). The water should flow to a suitable drain.
Initially, fill the water bubbler with water via the threaded
plug located at the top of the bubbler. Keep the plug
lubricated and hand tight. A circular, thin, plastic “stick-
on” acts as a bubbler relief device in case of water drain
plugging. The drain line should be supported to prevent
undue stress on the water bubbler.
OIL DRAINS
There are two 3/8” valve oil drain connections near the
bottom of purger (see Figure 1) from which oil can be
drained. These valves are fitted with 5/16” (8 mm) hex
socket plugs. Before draining oil, first close the liquid and
foul gas lines to prevent additional liquid from entering the
purger. Wait approximately one half hour and then turn
the purger off. Allow the purger to pump out, then close
the suction line shut-off valve. Use normal refrigerant oil
draining precautions to prevent human or property damage.
In general, oil will not be a problem unless the liquid line
is connected to a vessel or line where oil can enter the
purger. See also the Caution section on page 14. Escaping
refrigerant may cause personal injury, particularly to the
eyes and lungs.
LEAK TEST
Use standard refrigeration procedures to check the APM
for leaks before placing it into service. See also the
Caution section on page 14. Manually open one purge
point solenoid valve. Open the foul gas line shut-off valve
and wait a few moments for the flooded evaporator to
pressurize through the metering orifice. Allow pressure to
build to condensing pressure, as shown on the high side
pressure gauge. Close the foul gas line shut-off valve and
check the purger for leaks.
Where a high-pressure float regulator is used to drain one
or more condensers, the top of the float valve chamber
should also be a purge point.
Horizontal shell and tube water-cooled condensers, and
heat exchangers should be purged at the top, usually at
the point(s) furthest from the compressor discharge main
inlet.
Vertical condensers should be purged near the top of the
vessel if possible.
For certain types of oil separators where very low velocities
may exist near the top of the vessel, purging may be
advisable from a top fitting.
It is normally not advisable to purge controlled pressure
receivers, high-pressure thermosyphon vessels, or vessels
located on the low side of the system.
SUCTION LINE
The ¾” suction line from the purger should be connected
to a protected main suction line or a suction accumulator.
Install a suction line isolation shut-off valve near purger.
Excess amounts of liquid from the purger evaporator may
occasionally be transmitted through the suction line. The
suction temperature must be 40°F (4.4°C) or less to satisfy
the APM temperature sensor before purging will occur.
LIQUID LINE
A high-pressure ½” liquid line is required for the APM. The
connection to the high-pressure liquid source should be
a location where oil will not be directed into the purger.
Install liquid line shut-off valve near the purger. The liquid
line supplies refrigerant during start-up and feeds make-
up liquid as required. The only requirement is the liquid
supply pressure must be sufficiently above the purger
evaporator pressure, usually greater than 60 psi (4.1 bar).
During operation, only 5% of the liquid refrigerant required
for cooling comes from the liquid line. The remainder of
the refrigerant is condensate from the foul gas line, which
is collected in the drain, condensed in the coil, and into
the evaporator.
SECTION 1 MOUNTING & PIPING INSTALLATION