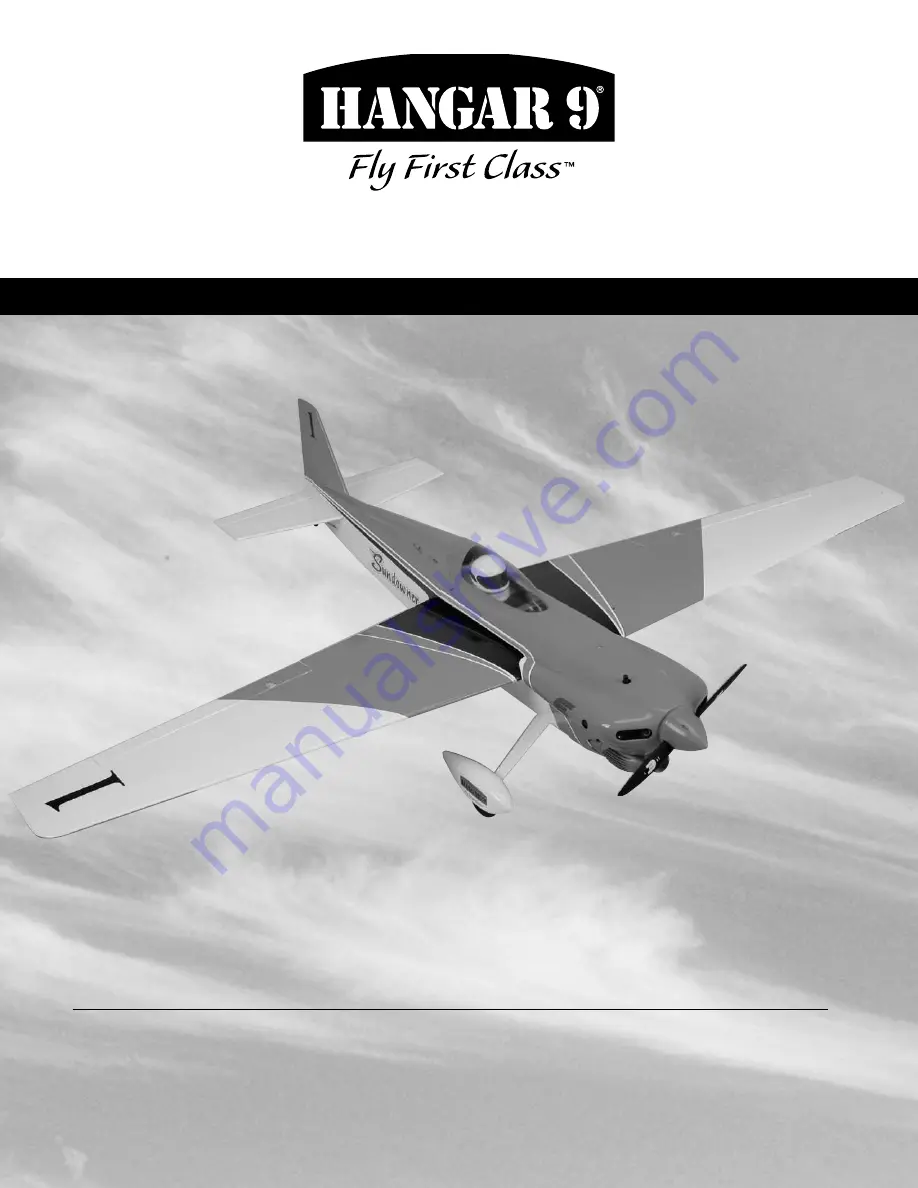
Wingspan ........................................63 in (1600mm)
Wing area .............................572 sq in (36.9 sq dm)
Length ..........................................47.4 in (1204mm)
Weight ................................... 6–6.75 lb (2.72–3 kg)
Assembly mAnuAl
Sundowner 50 ARF
Engine ..................................... .56–.82 Four-Stroke
....................................... .40–.52 Two-Stroke
...........................................Power 46 Electric
Radio..............4-Channel w/5 Servos (4 for electric)
Specifications