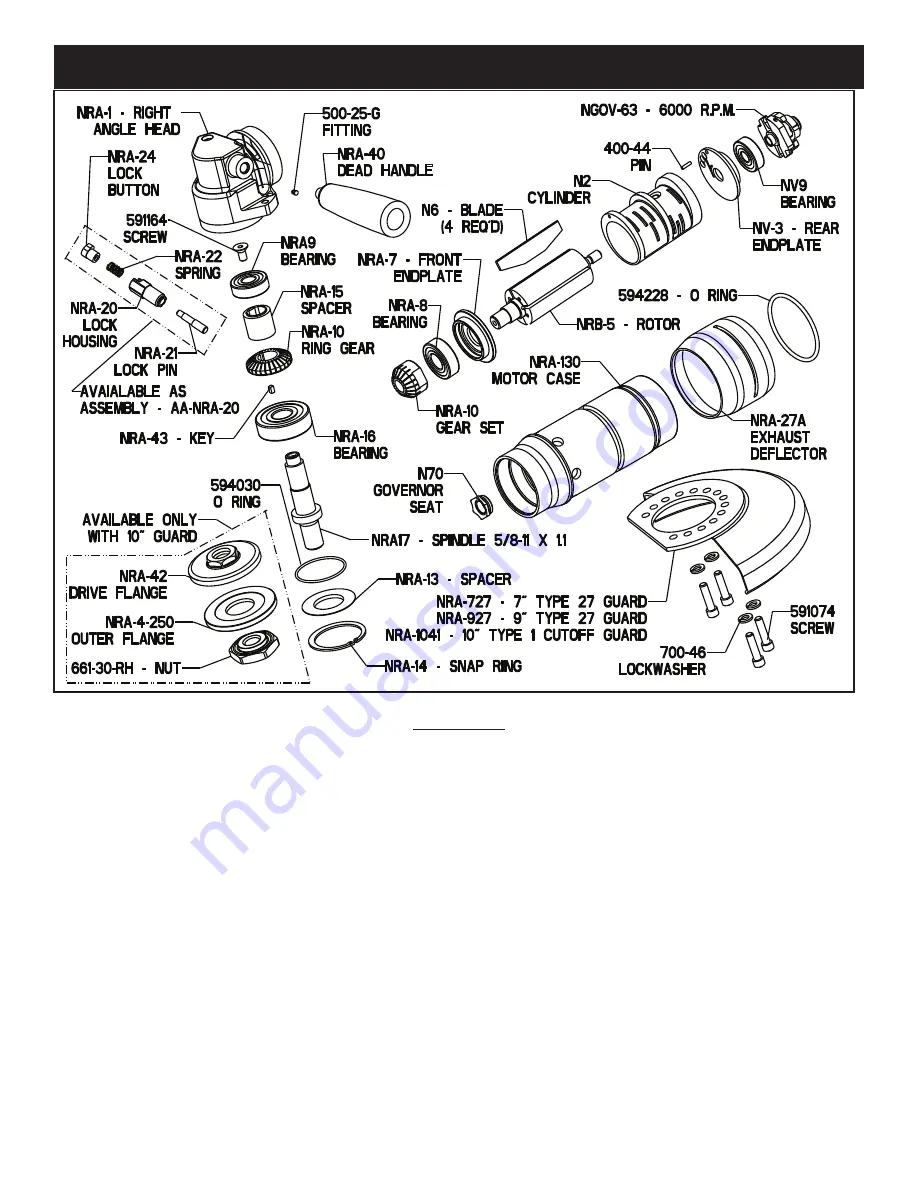
Maintenance
Disassemble
1. Disconnect tool from air supply and remove all wheels or accessories. Remove spindle lock assembly (AA-NRA-20).
2. Secure the tool in vise vertically with the angle head (NRA-1) toward downward direction. Clamp lightly onto dead
handle boss on the side of angle head. Using a wrench on
fl
ats at base of live handle, unscrew motor housing from angle
head. Remove motor from case or angle head (depending on how it came apart).
The Motor Assembly
3. Place brass jaws on vice. Secure pinion gear (NRA-10) in vise and remove governor (NGOV-XX). (Left-hand thread).
(Governor wrench (1100-832) is available to properly remove the governor with less risk of damage.) Remove assembly
from vise.
4. Clamp motor assembly into vise with output pointed down. Clamp lightly onto the cylinder (N2) and rear endplate (NV-
3). Place a small punch into the center of the motor spindle (NRB-5) where the governor was removed. Tap lightly on end
of punch with a small hammer. This will drive the spindle through the rear bearing (NV-9) (Be sure not to damage threads
on the rear of the spindle.) (Take care not to drop the spindle assembly when it becomes free.) Remove from vise.
5. Remove rear bearing from rear endplate (NV-3) with a small punch or screwdriver. Remove rotor blades (N6) from
rotor/spindle
6. Place brass jaws on vise. Clamp front spindle assembly in vise vertically with output in upward direction. Clamp onto
the large outside diameter of the rotor/spindle. Remove pinion gear (NRA-10) with a wrench. Remove assembly from vise.
7. Press output end of spindle through front bearing (NRA-8) with an arbor press. Remove front bearing support (NRA-8).
The Angle Head
8. Remove snap ring (NRA-14) using snap ring pliers. Remove spacer (NRA-13) and o-ring (594030). Lift output spindle
assembly from angle head.
9. Place brass jaws on vise. Cla
mp firmly onto threads of output assembl
y. Unscrew and remove screw (591164) from end
of spindle. Remove from vise.