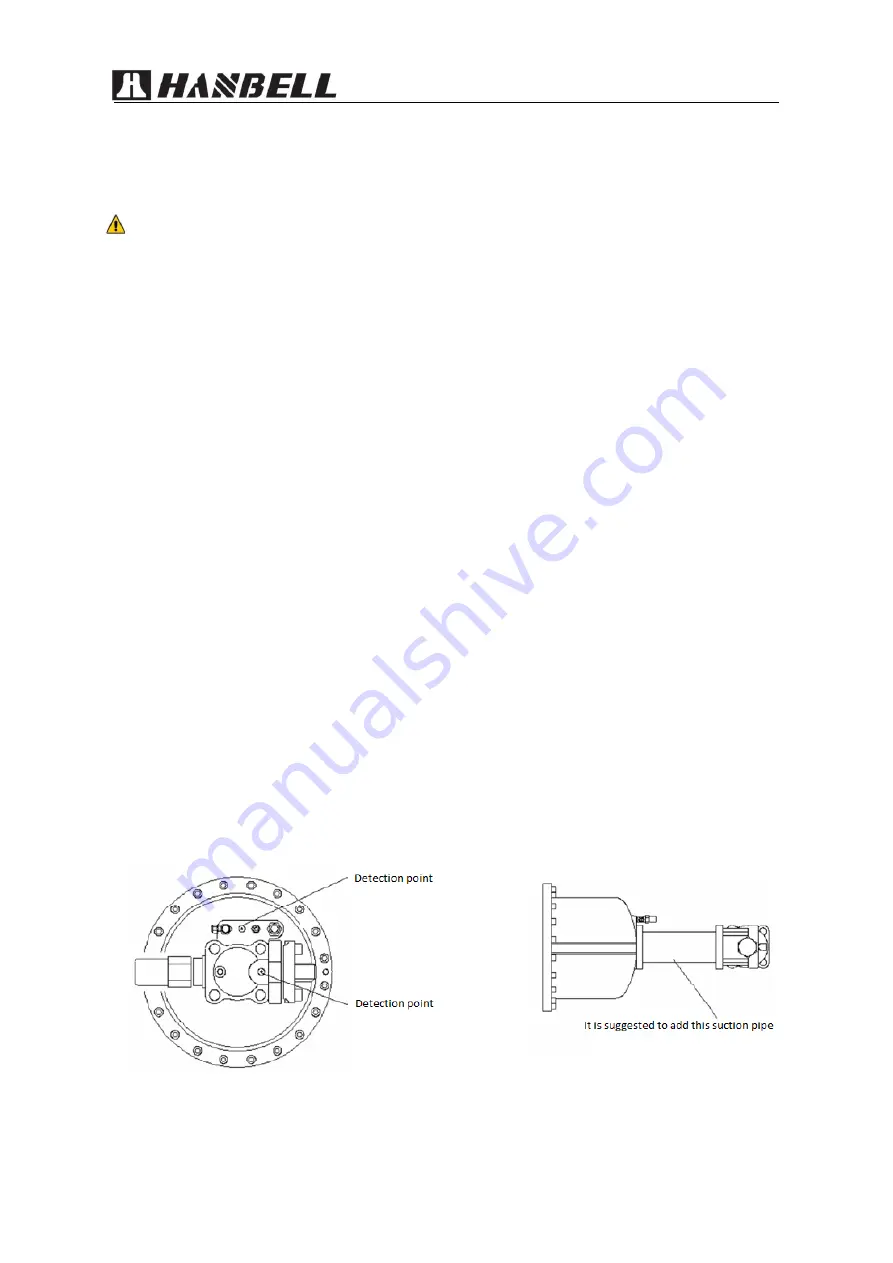
RC2-D Technical Manual
41
3.
Make sure each pressure switch is set correctly.
4.
Make sure all check valves are in open state.
5.
Start the compressor shortly (about 0.5-1 second) to ensure that the rotation is normal,
through monitoring the suction and discharge pressure .
Note:
Normal rotation judgment method: suction pressure drops immediately, while
the pressure rise.
1)
After start-up, the lubricating oil in the external oil filter should be checked. The oil
level should be within the visual range of the sight glass or higher than the middle line of
the sight glass.
2)
When the compressor starts, the oil in the separator will produce foam, but when the
compressor operates under the rated condition, the foam will decrease; otherwise it
means too much liquid in the compressor or excessive discharge temperature.
3)
The working condition should be adjusted according to the following ways: The
discharge temp should be 30K higher than the condensation temp, and the difference
between suction superheat and evaporation temperature should be within 15K .
4)
The whole system, especially the pipeline and capillary, must pass the vibration test. If
there is abnormal vibration or noise during operation, please contact Hanbell.
5)
If the compressor operates for long time, the following items should be inspected dai ly:
The operation data such as 3-phase voltage, compressor line current, etc.
Check lubricity of the oil and its level
Check all the sensor of compressor
Check the connection of the wire and its fastening property
Check the sight glass of the oil circuit
8.2
Compressor maintenance
The compressor can not be operated normally for without regular maintenance. The following items
need to be maintained regularly:
8.2.1
Maintenance instructions of suction filter
Regularly check the pressure difference at both ends of the suction filter. If the pressure difference is
greater than 0.5bar, clean or replace it. The pressure detection points are as shown in the figure.
The steps are as follows:
1.
Shut off the suction& discharge stop valve, oil line hand valve and liquid injection hand valve to
release the pressure in the compressor.
Содержание RC2-D
Страница 27: ...RC2 D Technical Manual 2 RC2 200 470 D S P terminal box 3 RC2 510 930 D S P terminal box ...
Страница 44: ...RC2 D Technical Manual 46 10 Appearance Drawing 10 1 RC2 100 930D S Drawing RC2 100 140D S Drawing ...
Страница 45: ...RC2 D Technical Manual 47 RC2 180D S Drawing ...
Страница 46: ...RC2 D Technical Manual 48 RC2 200 620D S Horizontal suction port Drawing ...
Страница 48: ...RC2 D Technical Manual 50 RC2 620 930D S Vertical suction port Drawing ...
Страница 49: ...RC2 D Technical Manual 51 10 2 RC2 100 930D P Drawing RC2 100 140D P Drawing ...
Страница 50: ...RC2 D Technical Manual 52 RC2 180D P Drawing ...
Страница 51: ...RC2 D Technical Manual 53 RC2 200 620D P Drawing ...
Страница 53: ...RC2 D Technical Manual 55 RC2 620 930D P Drawing ...