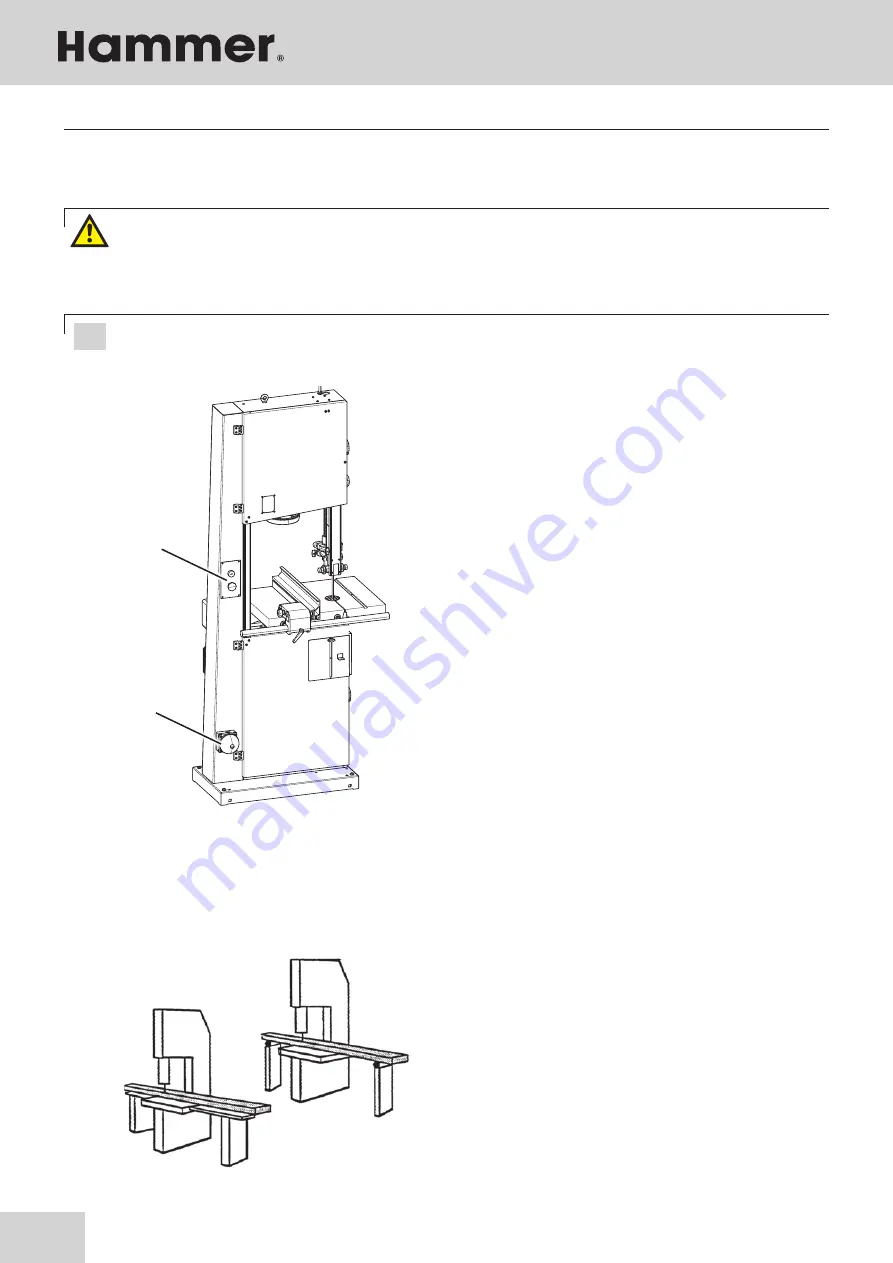
28
!
"
!
Bandsaw
N2-38 / N3800 / N4400
Operation
Warning! Risk of injury due to insufficient preparation!
It is only permitted to switch on the machine if, for the work at hand, the required preconditions are
fulfilled and any preliminary work is completed. Therefore, the adjusting, fitting and operating instructions
(see the corresponding chapters) must be read before switching on the machine.
Fig. 7-7: On- and Off switch
7.6 Switching on the machine / Switching off the machine
All uses which differ from the following work techniques
have not been intended for this machine and are therefore
not authorised.
Feed the workpiece with constant speed and pressure for-
wards without applying sideways pressure Do not interrupt
the cut and do not pull the workpiece backwards When
cutting large pieces, use appropriate table extensions or
roll supports.
Fig. 7-8: Rip cut
7.7.1 Longitudinal cut along the marked line
7.7 Authorised working techniques
Attention! The machine will not start with the doors open and will automatically stop if doors are opened
during operation. (Only valid for the CE-version !)
The bandsaw has an On- and Off switch.
Green push button:
Switch machine on
Red push button:
Switch off the machine.
Optional equipment: Additional emergency stop
!
On/Off switch
"
Additional emergency stop
Содержание N2-38
Страница 3: ...3 Bandsaw N2 38 N3800 N4400 ...