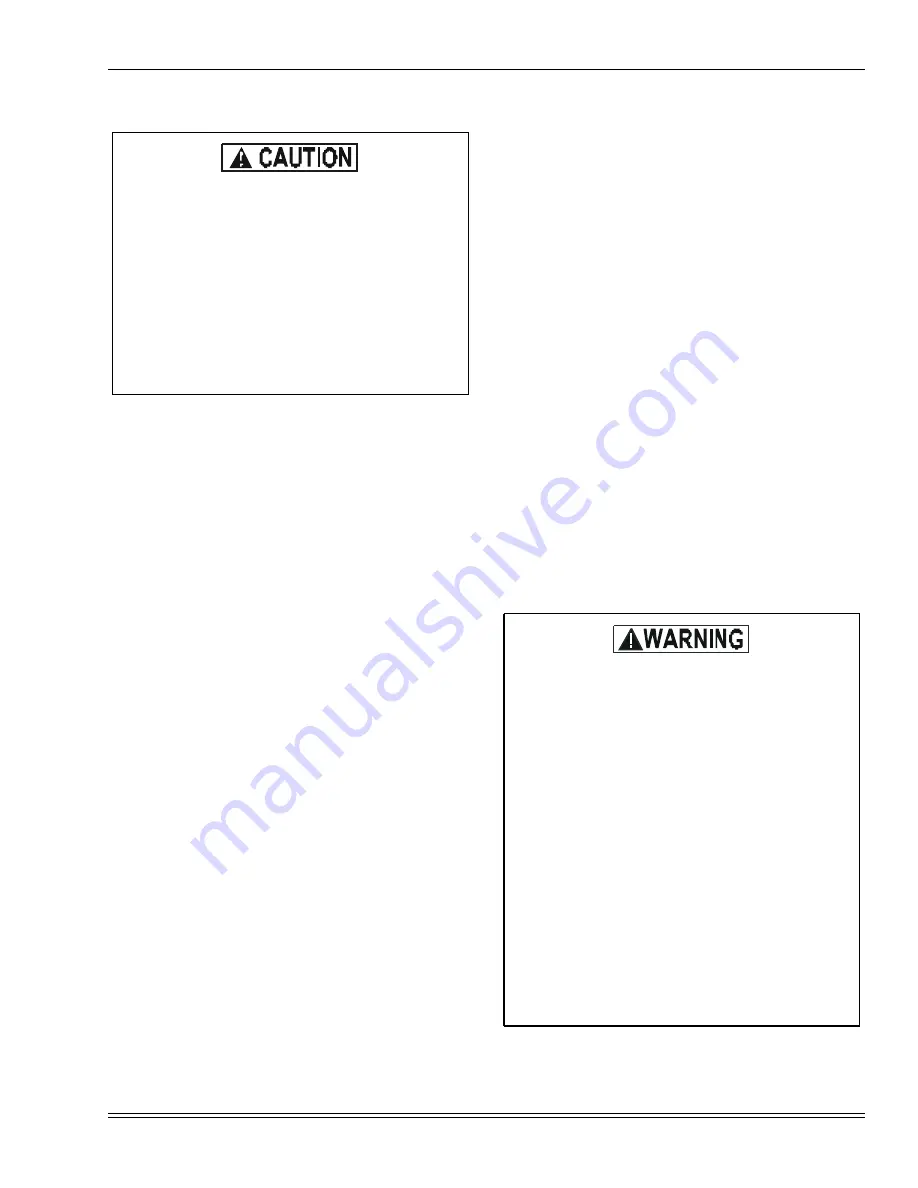
035-17477-002 Rev. D (1202)
Unitary Products Group
3
VENT SAFETY CHECK PROCEDURE
The following steps shall be followed with each appliance
connected to the venting system placed in operation, while
any other appliances connected to the venting system are not
in operation:
1.
Seal any unused openings in the venting system.
2.
Inspect the venting system for proper size and horizontal
pitch, as required in the National Fuel Gas Code, ANSI
Z223.1, or the CAN/CGA B149 Installation Codes and
these instructions. Determine that there is no blockage
or restriction, leakage, corrosion or other deficiencies
which could cause an unsafe condition.
3.
Insofar as is practical, close all building doors and win-
dows and all doors between the space in which the appli-
ance(s) is located and other spaces of the building. Turn
on clothes dryers. Turn on any exhaust fans, such as
range hoods and bathroom exhausts, so they shall oper-
ate at maximum speed. Do not operate a summer
exhaust fan. Close fireplace dampers.
4.
Follow the lighting instructions. Place the appliance
being inspected in operation. Adjust thermostat so the
appliance shall operate continuously.
5.
Test for draft hood equipped appliance spillage at the
draft hood relief opening after 5 minutes of main burner
operation. Use the flame of a match or candle.
6.
After it has been determined that each appliance con-
nected to the venting system properly vents when tested
as outlined above, return doors, windows, exhaust fans,
fireplace dampers and any other gas burning appliance
to their previous conditions of use.
7.
If improper venting is observed during any of the above
tests, the venting system must be corrected.
8.
Any corrections to the common venting system must be
in accordance with the National Fuel Gas Code Z223.1
or CAN/CGA B149.1 or .2 Installation Code (latest edi-
tions). If the common vent system must be resized, it
should be resized to approach the minimum size as
determined using the appropriate tables in Appendix G
of the above codes.
SPECIFIC UNIT INFORMATION
LIMITATIONS & LOCATION
This furnace should be installed in accordance with all
national and local building/safety codes and requirements, or
in the absence of local codes, with the National Fuel Gas
Code ANSI Z223.1 or CAN/CGA B149.1 or.2 Installation
Code (latest editions), local plumbing or waste water codes,
and other applicable codes.
Downflow/horizontal models when installed in a downflow
configuration are AGA/CGA listed for application into a manu-
factured (mobile) home.
Upflow models or horizontal applications are not approved for
mobile homes.
CLEARANCES FOR ACCESS
Ample clearances should be provided to permit easy access
to the unit. The following minimum clearances are recom-
mended:
1.
Twenty-four (24) inches between the front of the furnace
and an adjacent wall or another appliance, when access
is required for servicing and cleaning.
2.
Eighteen (18) inches at the side where access is
required for passage to the front when servicing or for
inspection or replacement of flue/vent connections.
In all cases, accessibility clearances shall take precedence
over clearances for combustible materials where accessibility
clearances are greater.
This furnace may not be common vented with any
other appliance, since it requires separate, prop-
erly-sized air intake and vent lines. The furnace
shall not be connected to any type of B, BW or L
vent or vent connector, and not connected to any
portion of a factory-built or masonry chimney.
If this furnace is replacing a common-vented fur-
nace, it may be necessary to resize the existing
vent line and chimney to prevent oversizing prob-
lems for the new combination of units. Refer to the
National Gas Code (ANSI Z223.1) or CAN/CGA
B149.1 or .2 Installation Code (latest editions).
Do not install the furnace in an unconditioned
space or garage that could experience ambient
temperatures of 32° F (0° C) or lower. For applica-
tion in below freezing locations, See “BELOW
FREEZING LOCATIONS” on page 4.
The furnace is not to be used for temporary heat-
ing of buildings or structures under construction.
This unit must be installed in a level (1/4”) position
side-to-side and front-to-back to provide proper
condensate drainage.
Do not allow return air temperature to be below
55°F for extended periods. To do so may cause
condensation to occur in the main fired heat
exchanger.
Only use natural gas in furnaces designed for nat-
ural gas. Only use propane (LP) gas for furnaces
that have been properly converted to use propane
(LP) gas. Do not use this furnace with butane.
Using wrong gas could create a hazard, resulting
in damage, injury or death.