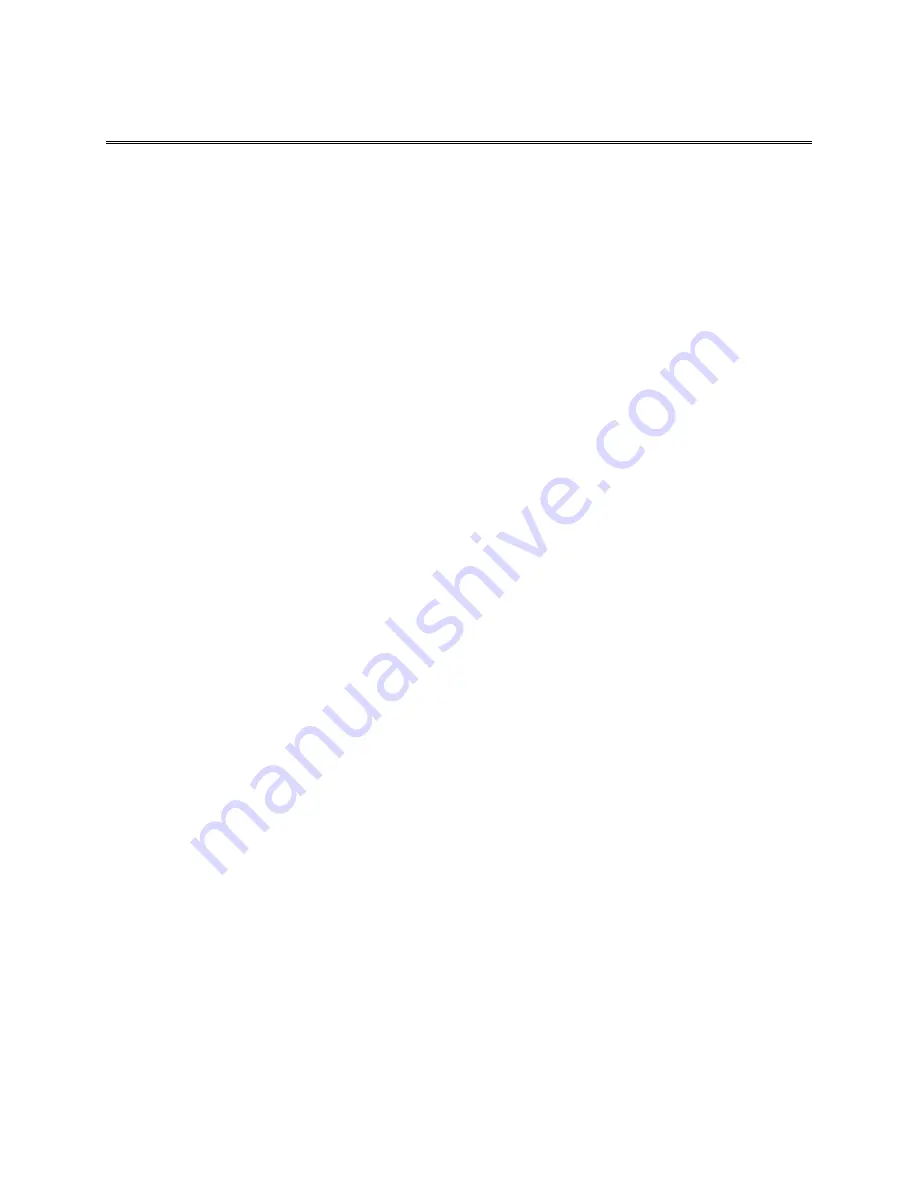
14
Measurement Overview
In general, a laser is used for alignment by making it parallel to
reference points
and using a target to
measure deviations from those points. Reference points are points chosen on a surface or in a bore that
represent the starting point for which all other points on the surface or in a bore will be compared. For
bore, spindle and rotating shaft applications, two reference points are needed to establish a
datum
, or the
basis used for calculating and measuring. For surfaces, three reference points are needed to establish a
datum.
For continuously rotating laser applications, like machining centers and presses, three to five reference
points are needed, although Level to Earth Measurements are frequently used instead of reference points.
Laser
buck-in
refers to the adjustment of a laser plane or beam to be parallel to the reference points (a
table top, a surface plate, or a way surface).
Once the laser is "bucked in," any point within range of the laser device, typically up to 100 ft. (30.5 m),
can be measured for deviation in one axis for rotating laser applications. One of the principal advantages
of geometry lasers is that they provide live alignment data, which means a machine or part may be
aligned without moving or changing the laser's setup. In effect, the targets act as a live digital indicator of
the alignment. When the target reads zero, the point is aligned and the next point is measured.
Selecting Reference Points on Machine Tools
When using a laser system or any other alignment method, it is important to select reference points
carefully. Poor reference points, like those on the heavily worn portion of a machine bed where all the
work is performed, may mean extra time to bring the machine back into tolerance. In other words, it could
be the reference points that need alignment rather than the rest of the axis.
In metrology, it is recommended that some sort of data analysis be performed on a machine's axis before
proceeding to the alignment stage. This step may save countless hours when aligning a machine tool that
has only a couple of bad points. Typically, a least-squares, best-fit algorithm is applied to a set of data for
an individual axis. This algorithm calculates a line or a plane that best fits the data and will quickly show
any bad data points. The data can also be adjusted so the alignment for each point would bring it parallel
to the best-fit line or plane.
Selecting Reference Points on Process Mills
Conventional methods of roll alignment usually use floor benchmarks (monuments) at the side of the
machine as references. The L-742 and L-732 offer the versatility of using the benchmarks or of picking
up a reference roll, such as a cooch roll on paper mills. However, we strongly believe that using a
reference roll provides a more accurate reference and results in better alignments.
Benchmarks are usually set in a thin concrete floor, are rarely covered, and are routinely run over and
nicked. More importantly, they move with their slab of concrete and rarely hold their position relative to
the mill itself. Most floors in a typical plant have multiple slabs and are usually cracked throughout,
creating instability of the monuments. Unless checked every time they are used, the use of the benchmark
probably will result in significant alignment errors.
Содержание Dual Scan L-732
Страница 1: ......
Страница 31: ...27 Appendix B Equipment Drawings L 733 Precision Geometry Laser...
Страница 32: ...28 L 743 Ultra Precision Geometry Laser...
Страница 33: ...29 The L 732 Dual Scan Precision Roll Alignment Laser...
Страница 34: ...30 The L 742 Dual Scan Ultra Precision Roll Alignment Laser...