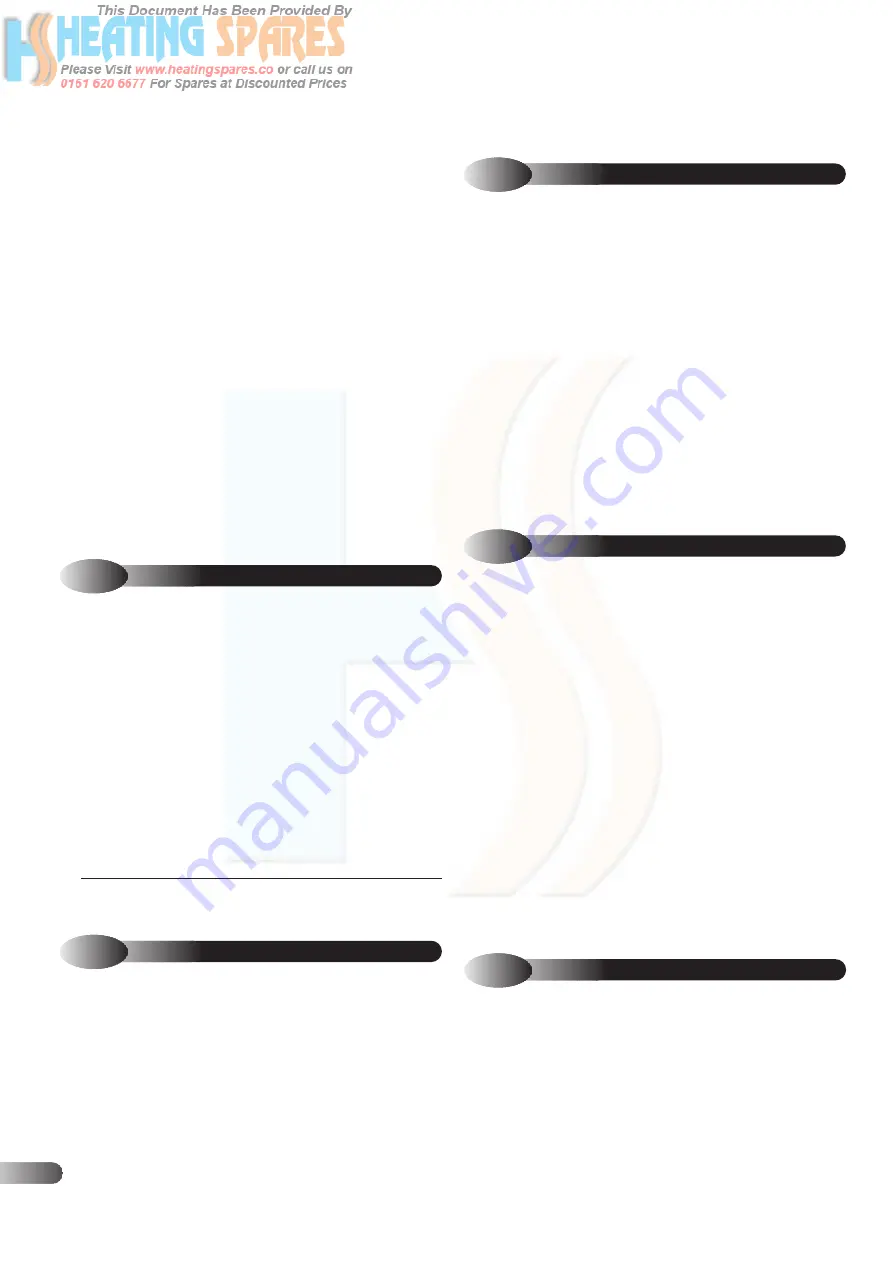
Supplied By www.heating spares.co Tel. 0161 620 6677
8
Detailed recommendations for air supply are given in
BS5440:2. The following notes are for general guidance.
a)
It is not necessary to have a purpose provided air vent in the
room or internal space in which the appliance is installed.
b)
If the boiler is installed in a cupboard or compartment,
permanent air vents are required for cooling purposes in the
cupboard or compartment at both high and low levels. Both
air vents must communicate with either the same internal
room/space or be on the same wall to external air. Each air
vent communicating with another room or internal space must
have a minimum effective area. See table below.
Minimum Area Requirements cm
2
(in
2
) For Compartment
Air Ventilation.
Best
Air from another room
Air direct from outside
High & Low level
High & Low level
80
264cm (42in)
132cm (20in)
3.4
VENTILATION REQUIREMENTS
a)
The Local Gas Supplier should be consulted at the installation
planning stage in order to establish the availability of an
adequate supply of gas.
b)
An existing service pipe MUST NOT be used without prior
consultation with the Local Gas Supplier.
c)
A gas meter can only be connected by the Local Gas Supplier
or by a Local Gas Region Contractor.
d)
An existing meter should be of sufficient size to carry the
maximum boiler input plus the demand of any other installed
appliance. (BS6891: 1988). See section 2.2 General Data for
the gas required for each specific model. A minimum of 22mm
dia. pipework to within 1 metre of the appliance gas cock.
3.5
GAS SUPPLY
The mains supply required is 230V - 50 Hz fused at 3A, via a
fused double pole isolator with a contact separation of at least
3 mm in both poles. This should be a permanent connection to
the fixed wiring of the system.
There must be only one common isolator for the boiler and its
control system, and it must provide complete electrical isolation.
The power supply cable to the appliance should be at least
0.75 mm
2
(24 x 0.2 mm) PVC heat resistant, as specified in
table 16 of BS6500.
All external wiring to the boiler must be in accordance with the
latest I.E.E. Wiring Regulations, and any local regulations
which apply.
The appliance must be earthed.
In the event of an electrical fault after installation of the appliance,
preliminary electrical systems checks must be carried out i.e. Earth
Continuity, Short Circuit, Polarity, and Resistance to Earth.
All fuses must be ASTA approved to BS1362.
3.6
ELECTRICAL SUPPLY
The boiler must not be used for direct hot water supply. The hot
water cylinder must be of the fully indirect (double feed) type, Self
priming (single feed) cylinders MUST NOT BE USED.
The boiler is supplied with fittings necessary for use with copper
tubing to BS2871 on fully pumped systems, and combined
pumped CH and gravity DHW systems. It is important that the
appropriate fittings are correctly used.
‘Street’ elbows must also be used for the 28mm gravity
connections to the boiler to provide adequate clearance for fitting
the right hand inner case.
Drain off cocks must be fitted at the lowest points of the system.
If the position of the boiler is such that it may be vulnerable to
freezing it should be protected as specified in the current issue of
BS5422. It is recommended that a frost protection thermostat
is fitted.
The pump, with its isolation valves, should be fitted in the heating
flow pipework from the boiler. It should be set to produce a
temperature difference of 11°C between the flow and return pipes
on the boiler. The resistance through the appliance at the
required flow rate, may be found in Section 2.3.
3.7
WATER SYSTEMS
An open vent pipe of 22mm diameter must be fitted in the boiler
flow and terminated above the cold feed, discharging into the
expansion cistern. The open vent must rise continuously from its
connection with the system.
The expansion cistern should not have a smaller capacity than
22 litres, (5 gallons).
The cold feed should be of 15mm minimum diameter.
The expansion cistern should have a lid to prevent
evaporation loss.
The cistern must not be higher than 30m (100ft) above the boiler,
or less than 1.2m (47in).
3.7.1
OPEN VENTED SYSTEMS
b)
It is important that the position of the terminal allows free
passage of air across it at all times.
c)
It is ESSENTIAL TO ENSURE that products of combustion
discharging from the terminal cannot re-enter the building, or
any other adjacent building, through ventilators, windows,
doors, other sources of natural air infiltration, or forced
ventilation / air conditioning.
d)
The minimum acceptable dimensions from the terminal to
obstructions and ventilation openings are specified in Fig.9.
e)
If the terminal discharges into a pathway or passageway
check that combustion products will not cause nuisance and
that the terminal will not obstruct the passageway.
f)
Where the lowest part of the terminal is fitted less than 2m
(78ins) above ground, above a balcony or above a flat roof to
which people have access, the terminal MUST be protected by
a purpose designed guard. (Available as an optional extra)
g)
Where the terminal is fitted within 850mm (34in) of a plastic
or painted gutter, or 450mm (18in) of painted eaves, an
aluminium shield at least 750mm long must be fitted to the
underside of the painted surface.
h)
The air inlet / flue outlet duct MUST NOT be closer than
25mm (1in) to combustible material.
i)
In certain weather conditions the terminal may emit a plume
of steam. This is normal but positions where this would cause
a nuisance should be avoided.
j)
It is recommended that the flue pipe should have a slight fall
away from the boiler towards the terminal.
e)
The governor at the meter must give a constant outlet pressure
of 20mbar (8 in.wg) when the appliance is running.
f)
The gas supply line should be purged. WARNING: Before
purging, open all doors and windows, also extinguish any
cigarettes, pipes, and any other naked lights.
g)
The complete installation must be tested for gas soundness.