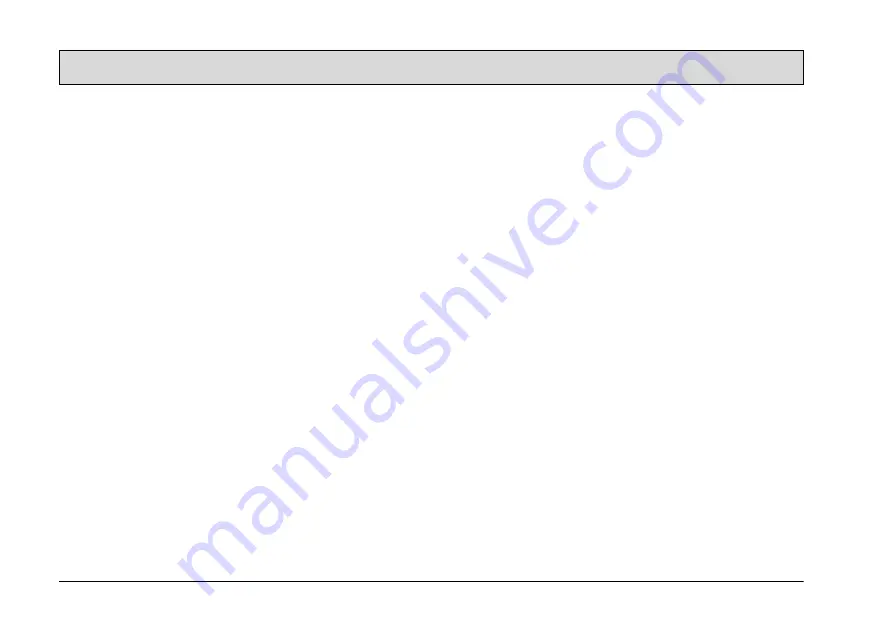
20
Operation
Covers (Fig. 5/12)
The covers must be removed in order to
change the circular brushes.
Star-sharped knobs for sealing strip
The sealing strips are fixed to the cov-
ers by means of star-sharped knobs so
that they can be vertically adjusted.
Star-sharped knobs for covers (Fig.
5/14)
The s
tar-sharped knob
s hold the cov-
ers on the brush head.
Содержание 7300.10
Страница 1: ...Instruction Manual Scrubmaster B100R 7300 10 20 ...
Страница 50: ...50 Maintenance and Service ...