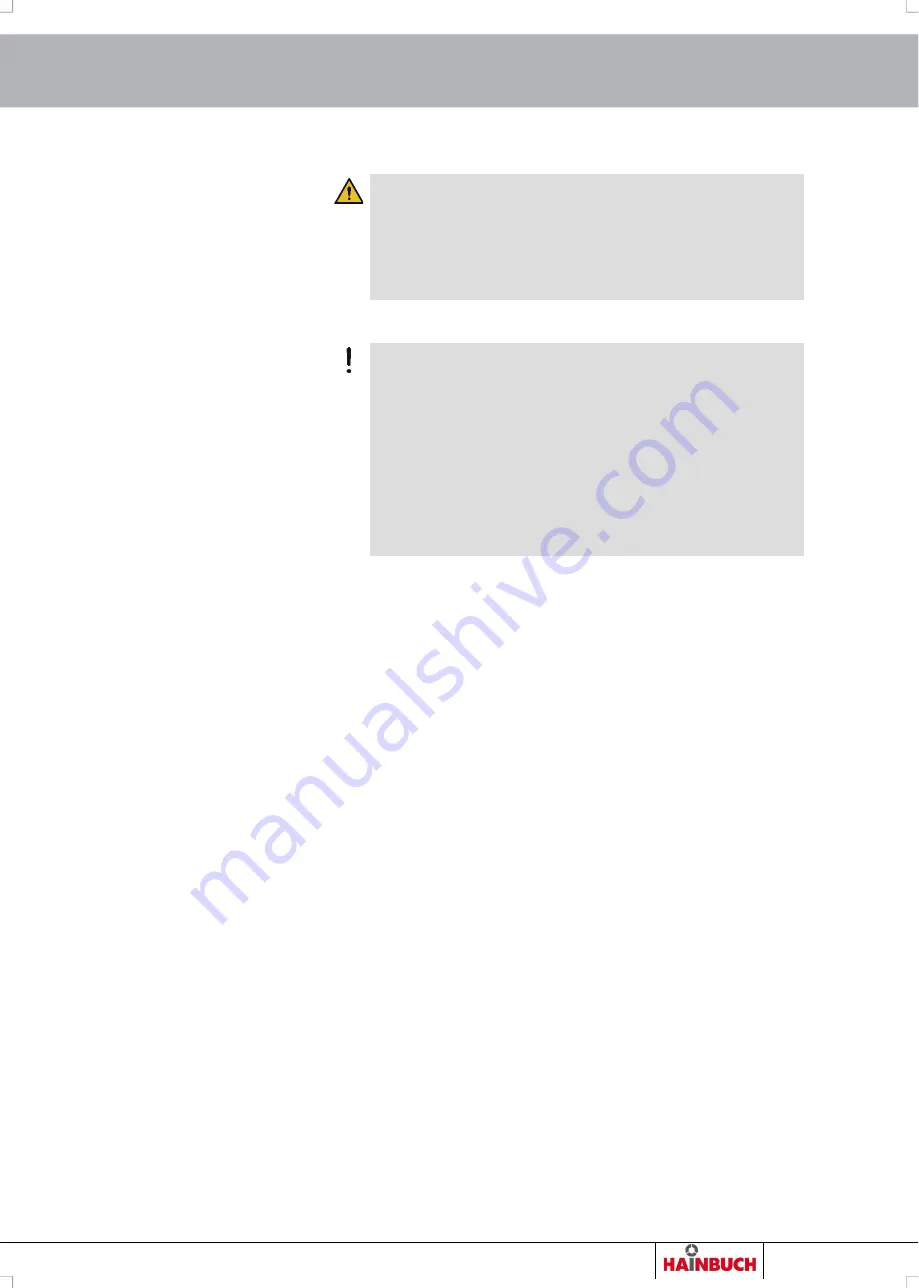
MANDO G211
Safety
Order h49 7144.907-333
21
2.8 Functionality
WARNING
Serious injuries caused by severe contamination
of the product!
Always comply with the cleaning instructions and
intervals [see »Cleaning« chapter].
2.9 Environmental protection
NOTE
Substantial damage to the environment can result
from non-compliant handling or incorrect dis-
posal of environmentally hazardous substances!
If environmentally hazardous substances enter
the environment accidentally, take immediate re-
medial action.
If in doubt, notify the relevant municipal authori-
ties about the incident.
The following environmentally hazardous substances are
used:
Lubricants, auxiliary materials and operating fluids
Lubricants such as grease and oil can contain toxic sub-
stances. These must not enter the environment.
Dispose of environmentally hazardous substances properly
[see »Disposal« chapter].