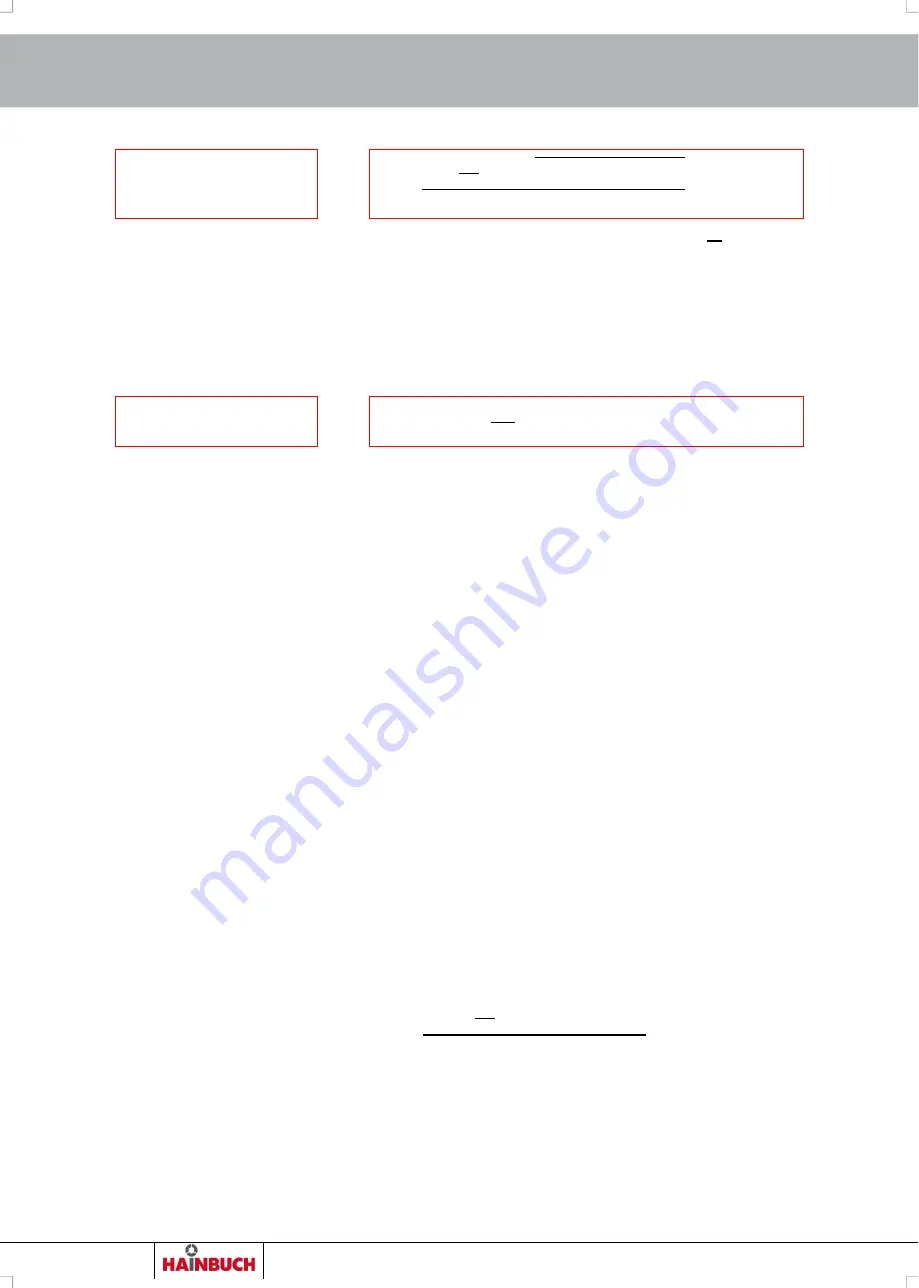
HYDROK
Use and limits of use
46
Order h49 7144.907-333
III
𝐹
𝑠𝑘
=
(0.27∗
𝐿𝑧
𝑑𝑠𝑝
+0.63)∗√(𝐹
𝑐
∗𝐿
𝑧
+𝐹
𝐺
∗𝐿
𝑔
)
2
+(𝐹
𝑐
∗𝑃)
2
0.5∗(0.67∗(1.9∗𝐿
𝑠𝑝
−4.5𝑚𝑚)+𝜇
𝑎
∗𝑑
𝑠𝑝
)
Longitudinal turning
𝑃 =
𝑑
𝑧
2
Surface turning / plunge-ma-
chining
𝑃 = 𝐿
𝑧
If the workpiece is braced against a tailstock, it
is OK to continue calculating with
20%
from the
computed
𝐹
𝑠𝑘
value.
IV
𝐹
𝑓𝑧
= 𝑚 ∗ 𝑟
𝑠
∗ (
𝜋∗𝑛
30
)
2
With reference to the principle defined at the start, this
means that the radial clamping force of the clamping head
chuck equates to at least the computed level of radial clamp-
ing force required
𝐹
𝑟𝑎𝑑 𝑒𝑟𝑓
to resolve this use of the clamping
head chuck.
If this condition is not satisfied, the clamping head chuck
would not be suitable. It would not then be possible to per-
form this machining task.
When clamping and machining workpieces with bigger er-
rors in axial and face run-out, please note that the cutting
cross-section fluctuates greatly. Particular attention needs to
be paid to the resultant local increase in cutting force.
Determining the required clamping force for radial drill-
ing operations
With radial drilling operations directed at the center, radial
clamping force
𝐹
𝑟𝑎𝑑 𝑒𝑟𝑓
is also determined in accordance with
an approach
𝐹
𝑟𝑎𝑑 𝑒𝑟𝑓
= 𝑆 ∗ 𝑐 ∗ (1.6 ∗ (𝐹
𝑠𝑧
+ 𝐹
𝑠𝑘
) + 𝐹
𝑓𝑧
)
whereby, although based upon components
𝐹
𝑠𝑧
= 0
and
𝐹
𝑓𝑧
= 0
, a simplified form [just transverse force] can be used:
𝐹
𝑟𝑎𝑑 𝑒𝑟𝑓
= 𝑆 ∗ 𝑐 ∗ 1.6 ∗ 𝐹
𝑠𝑘
Determining of
𝐹
𝑠𝑘
can be calculated as follows for
drilling operations performed radially in relation to the
clamping device axis, in a similar way to Formula III:
𝐹
𝑠𝑘
=
(0.27∗
𝐿𝑧
𝑑𝑠𝑝
+0.63)∗(𝐹
𝑞
∗𝐿
𝑧
+𝐹
𝐺
∗𝐿
𝑔
)
0.5∗(0.67∗(1.9∗𝐿
𝑠𝑝
−4.5𝑚𝑚)+𝜇
𝑎
∗𝑑
𝑠𝑝
)
To calculate
𝐹
𝑞
, see the »Further to Principle 4:
𝐹
𝑞
≤
𝐹
𝑞 𝑚𝑎𝑥
« chapter.
𝐹
𝑞
= 𝐹
𝐵
= 0.45 ∗ 𝐷
𝐵
∗ 𝑓
𝑛
∗ 𝑘
𝑐