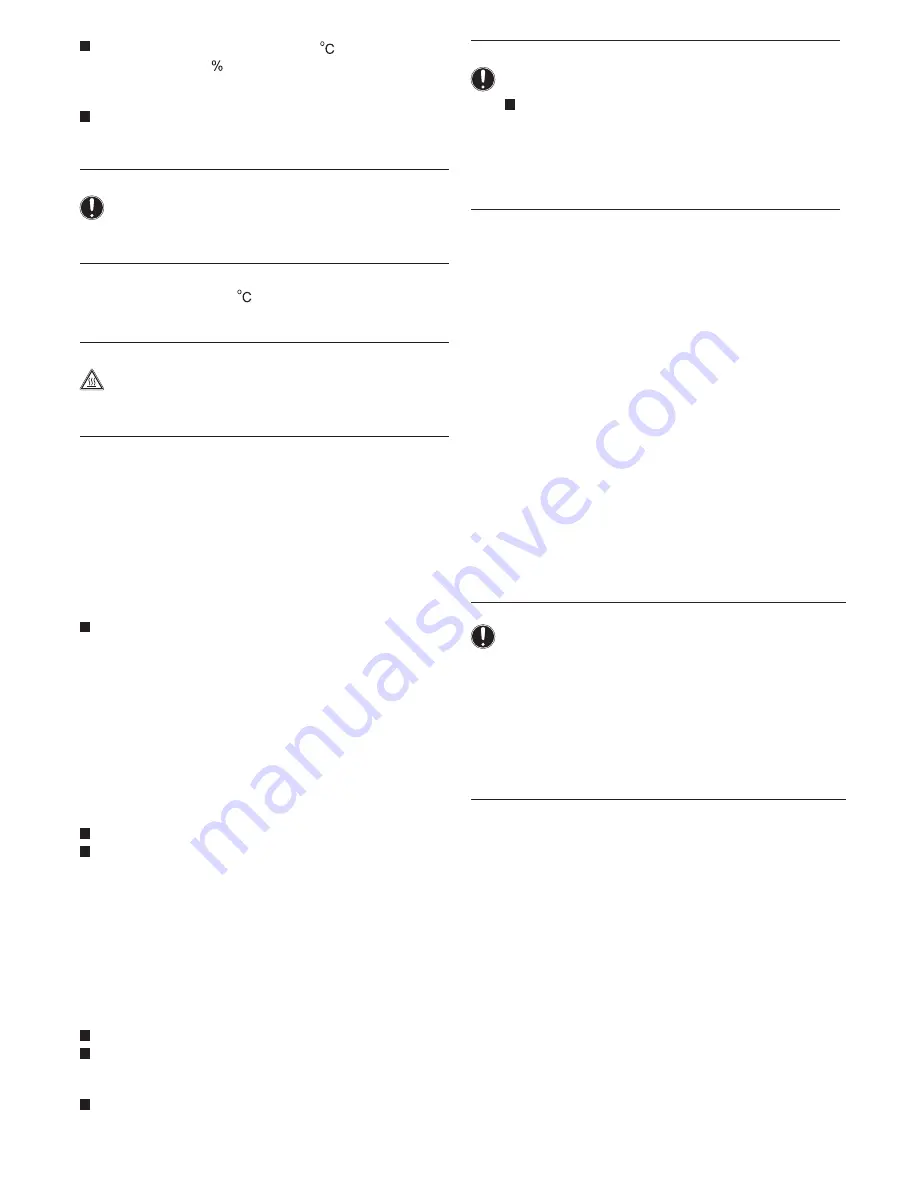
13
If the temperature is higher than 30 and the humidity is
higher than RH 80 , then thickness of the sealing materials
should be at least 20mm in ouder to avoid condensation
on the surface of the sealing.
Be sure to insulate the liquid and gas-side field piping.
Any exposed piping may cause condensation.
(The highest temperature that the gas-side piping can
reach is around 120 , so be sure to use insulating
material which is very resistant.)
No not touch piping and internal parts.
To avoid the the risk of oil held inside the riser piping flowing
back into the compressor when stopped and causing liquid
compression phenomenon, or cases of deterioration of oil
return, it will be necessary to provide a trap at each difference
in height of 10m in the riser gas piping.
A trap is not necessary when the outdoor unit is installed
at higher position than the indoor unit.
NOTICE
DANGER
7.7. Cautions for necessity of a trap
When all piping work is complete and the outdoor unit is
connected to the indoor unit, it is necessary to :
check for any leakages in the refrigerant piping
to perform vacuum drying to remove all moisture in the
refrigerant piping.
If there is a possibility of moisture being present in the
refrigerant piping (for example, rainwater may have entered
the piping), first carry out the vacuum drying procedure
below until all moisture has been removed.
All piping inside the unit has been factory tested for leaks.
Use a 2-stage vacuum pump with a non-return valve
which can evacuate to a gauge pressure of-100.7kPa(5
Torr absolute,-755mm Hg).
Connect the vacuum pump to both the service port of
the gas stop valve and the liquid stop valve to increase
efficiency.
8. Leak test and vacuum
drying
8.1. General guidelines
Do not purge the air with refrigerants. Use a vacuum
pump to evacuate the installation. No additional
refrigerant is provided for air purging.
Make sure that the gas stop valve and liquid stop
valve are firmly closed before performing the leak
test or vacuum drying.
NOTICE
The leak test must satisfy specification EN378-2.
1 Vacuum leak test
1.1 Evacuate the system from the liquid and gas piping
to -100.7 kPa(5 Torr).
1.2 Once reached, turn off the vacuum pump and check
that the pressure does not rise for at least 1 minute.
1.3 Should the pressure rise, the system may either
contain moisture (refer to the paragraph " Vacuum
drying ") or have leaks.
2 Pressure leak test
2.1 Break the vacuum by pressurizing with nitrogen gas
to a minimum gauge pressure of 0.2 MPa (2 bar).
Never set the gauge pressure higher than the
maximum operation pressure of the unit, i.e. 4.0MPa
(40bar).
2.2 Test for leaks by applying a bubble test solution to
all piping connections.
8.2. Leak test
Make sure to use a recommended bubble test solution
from your wholesaler.
Do not use soap water, which may cause cracking of
falre nuts (soap water may contain salt, which absorbs
moisture that will freeze when the piping gets cold).
and/or lead to corrosion of flared joints (soap water may
contain ammonia which causes a corrosive effect between
the brass flare nut and the copper flare).
NOTICE
To remove all mositure from the system, proceed as follows:
1 Evacuate the system for at least 2 hours to a target
vacuum of -100.7 kPa(=-1.007 bar).
2 Check that, with the vacuum pump turned off, the target
vacuum is maintained for at least 1 hour.
3 Should you fail to reach the target vacuum within 2 hours
or maintain the vacuum for 1 hour, the system may contain
too much moisture.
4 In that case, break the vacuum by pressurizing with
nigrogen gas to a gauge pressure of 0.05 MPa (0.5bar)
and repeat steps 1 to 3 unit all moisture has been removed.
5 The stop valves can now be opened, and/or additional
refrigerant can be charged .
8.3. Vacuum drying
Содержание 1UH071N1ERG
Страница 22: ...22 12 6 Failure diagnosis ...
Страница 23: ......