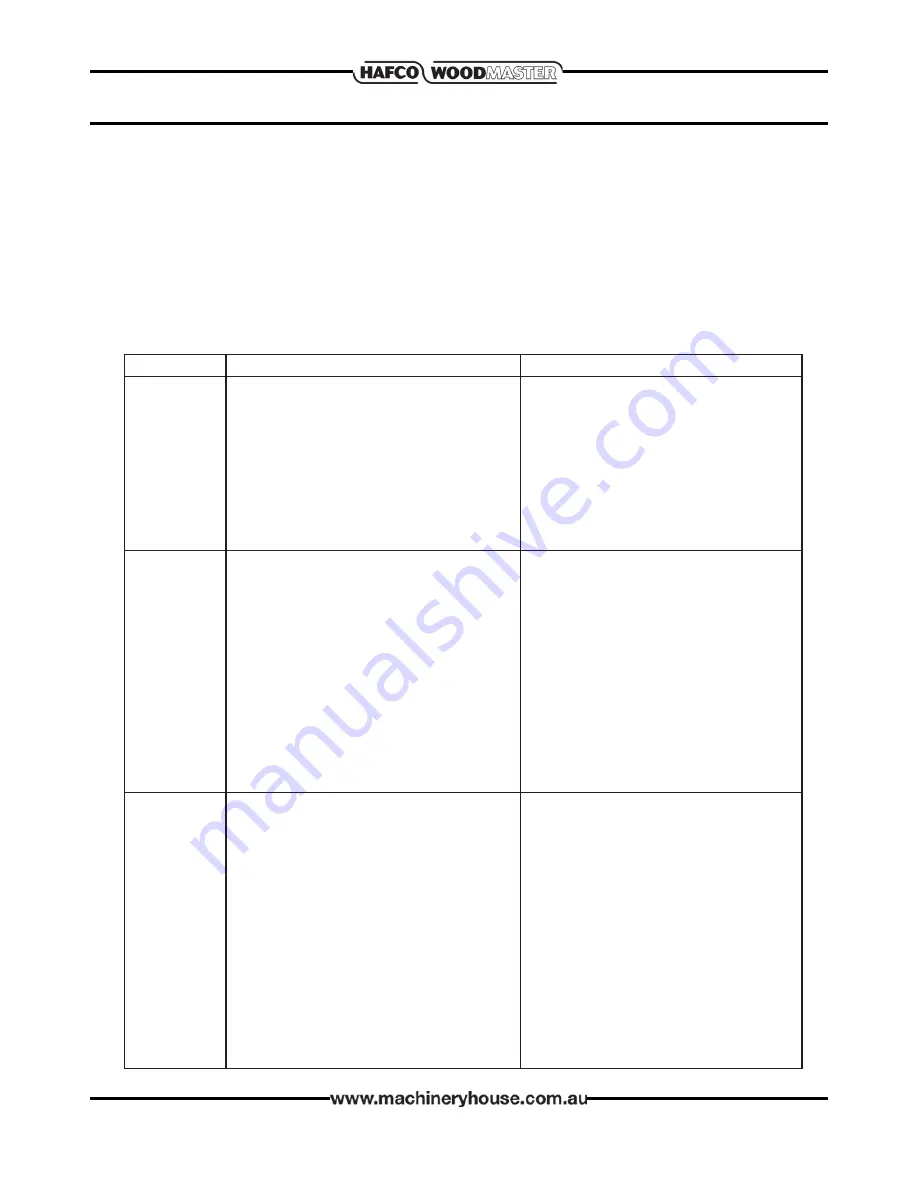
21
OPERATION MANUAL
Review the troubleshooting and procedures in this section to fix or adjust your machine if a
problem develops. If you need replacement parts or you are unsure of your repair skills, then
contact your local distributor or service provider.
NOTE:
Hafco/Woodmaster advise that exten-
sion leads should not be used permanently, but recommend that the plug be placed directly in
to a wall socket.
6. MAINTENANCE
Symptom
Possible Cause
Possible Solution
Machine does
not start or a
breaker trips.
1. Plug/receptacle is at fault or wired incorrectly.
2. Motor connection wired incorrectly.
3. Power supply is at fault/switched OFF.
4. Motor ON/OFF switch is at fault.
5. Wiring is open/has high resistance.
6. Start capacitor is at fault.
7. Motor is at fault.
1. Test for good contact or correct the wiring.
2. Correct motor wiring connections
3. Have a qualified electrician check the volt-
age at the meter box, and that connections
are not faulty.
4. Replace faulty ON/OFF switch.
5. Check for broken wires or corroded connec-
tions, and repair/replace as necessary.
6. Test/replace if faulty.
7. Repair/replace.
Machine
stalls or is
underpowered
1. Wrong workpiece material (wood).
2. Processing speed too fast for task.
3. Low power supply voltage.
4. Run capacitor is at fault.
5. V-belt slipping.
6. Blade is slipping on wheels.
7. Motor bearings are at fault.
8. Motor has overheated.
9. Motor is at fault.
1. Use wood with correct moisture content,
without glues, and little pitch/resins.
2. Decrease processing speed.
3. Ensure all hot lines have correct voltage on
all phase.
4. Repair/replace.
5. Replace bad V-belt, align pulleys, and
re-tension
6. Adjust blade tracking and tension.
7. Test by rotating shaft; rotational grinding/
loose shaft requires bearing replacement.
8. Clean off motor, let cool, and reduce work-
load.
9. Repair/replace.
Machine has
vibration or
noisy oper-
ation when
running.
1. Motor or component is loose.
2. V-belt worn or loose.
3. Motor fan is rubbing on fan cover.
4. Pulley is loose.
5. Machine is incorrectly mounted or sits
unevenly on the floor.
6. Motor bearings are at fault.
7. Blade weld is at fault or teeth are broken.
8. Worn arbor bearings.
9. Wheels not aligned correctly.
10. Tyres incorrectly installed.
11. Bent or worn out blade.
12. Wheels out of balance.
1. Inspect/replace stripped or damaged bolts/
nuts, and re-tighten with thread locking fluid.
2. Inspect/replace belt .
3. Replace dented fan cover
4. Realign/replace shaft, pulley, set screw, and
key as required.
5. Adjust the feet on the bottom of the stand;
relocate machine.
6. Test by rotating shaft and replace bearing if
required
7. Replace blade
8. Check/replace arbor bearings.
9. Adjust wheel alignment (Page 22)
10. Re-install tyres.
11. Replace blade.
12. Replace wheels.
6.1 TROUBLESHOOTING