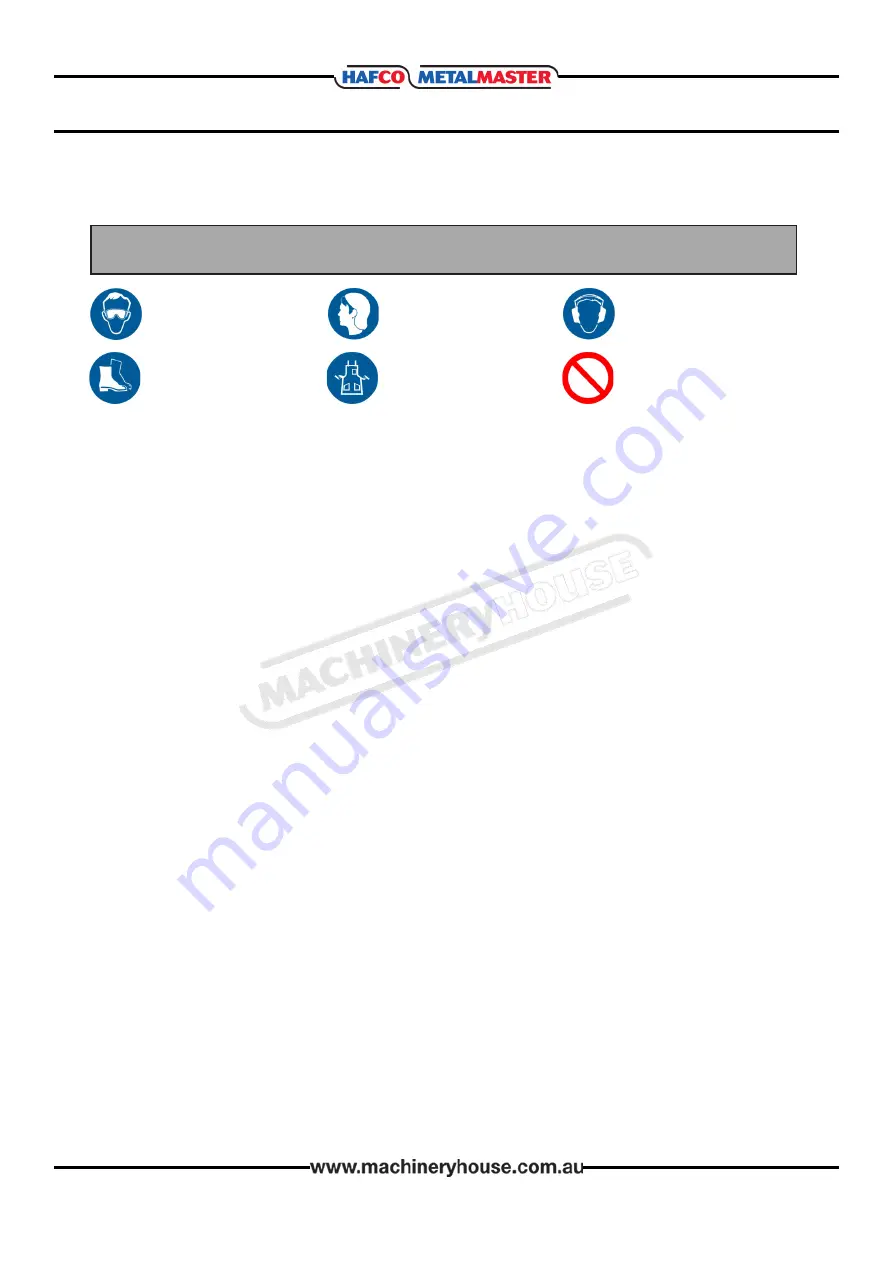
9
OPERATION MANUAL
2.2 MITRE SAW SAFETY
DO NOT use this machine unless you have been instructed in its safe use and
operation and have read and understood this manual
Safety glasses must be
worn at all times in work
areas
Long and loose hair must
be contained.
Long and loose hair must
be contained.
Sturdy footwear must be
worn at all times in work
areas
Close fitting/protective
clothing must be worn
Rings and jewelery must
not be worn.
PRE-OPERATIONAL SAFETY CHECKS
Locate and ensure you are familiar with all machine operations and controls.
Ensure all guards are fitted, secure and functional. Do not operate if guards are missing or faulty.
Ensure the saw base is properly secured to the floor by bolts
Ensure the saw is operated on an RCD protected circuit.
Check workspaces and walkways to ensure no slip/trip hazards are present.
Keep table and work area clear of all tools, and aluminium off-cuts.
Start the mist coolant before using the machine.
OPERATIONAL SAFETY CHECKS
Ensure all adjustments are secure before making a cut.
Use clamps to secure and support the workpiece to a stable platform. Make sure that the workpiece
is clamped hard up against the fence.
Before turning on the saw, perform a dry run of the cutting operation to ensure no problems will
occur when the cut is made.
Avoid reaching over the saw line. Do not cross arms when cutting.
When pulling the saw down with your right hand, keep the left hand, especially the thumb, well
clear of the line of cut.
After finishing the cut, release the switch, hold the saw arm down and wait for blade to stop before
removing work or off-cut piece.
Before making any adjustments, disconnect the machine from the power source and bring the
machine to a complete standstill.
DON’T
Do not use faulty equipment. Immediately report suspect equipment.
Do not exceed the maximum cut for the machine.
Do not cut more than one workpiece at a time.
Do not start the saw with the blade touching the workpiece. Allow the blade to reach full speed
first.
POTENTIAL HAZARDS AND INJURIES
r
Saw may grab and ‘kick-back’ toward operator.
r
Flying metal chips and airborne coolant.
r
Contact with rotating blade.
r
Eye injuries.
21/01/2020
Instructions Manual for ALU-350A (S851)
9
Содержание ALU-350A
Страница 21: ...21 OPERATION MANUAL TURNTABLE SPARE PARTS DIAGRAM 21 01 2020 Instructions Manual for ALU 350A S851 21 ...
Страница 22: ...22 OPERATION MANUAL SAW ARM SPARE PARTS DIAGRAM 21 01 2020 Instructions Manual for ALU 350A S851 22 ...
Страница 23: ...23 OPERATION MANUAL STAND SPARE PARTS DIAGRAM 21 01 2020 Instructions Manual for ALU 350A S851 23 ...