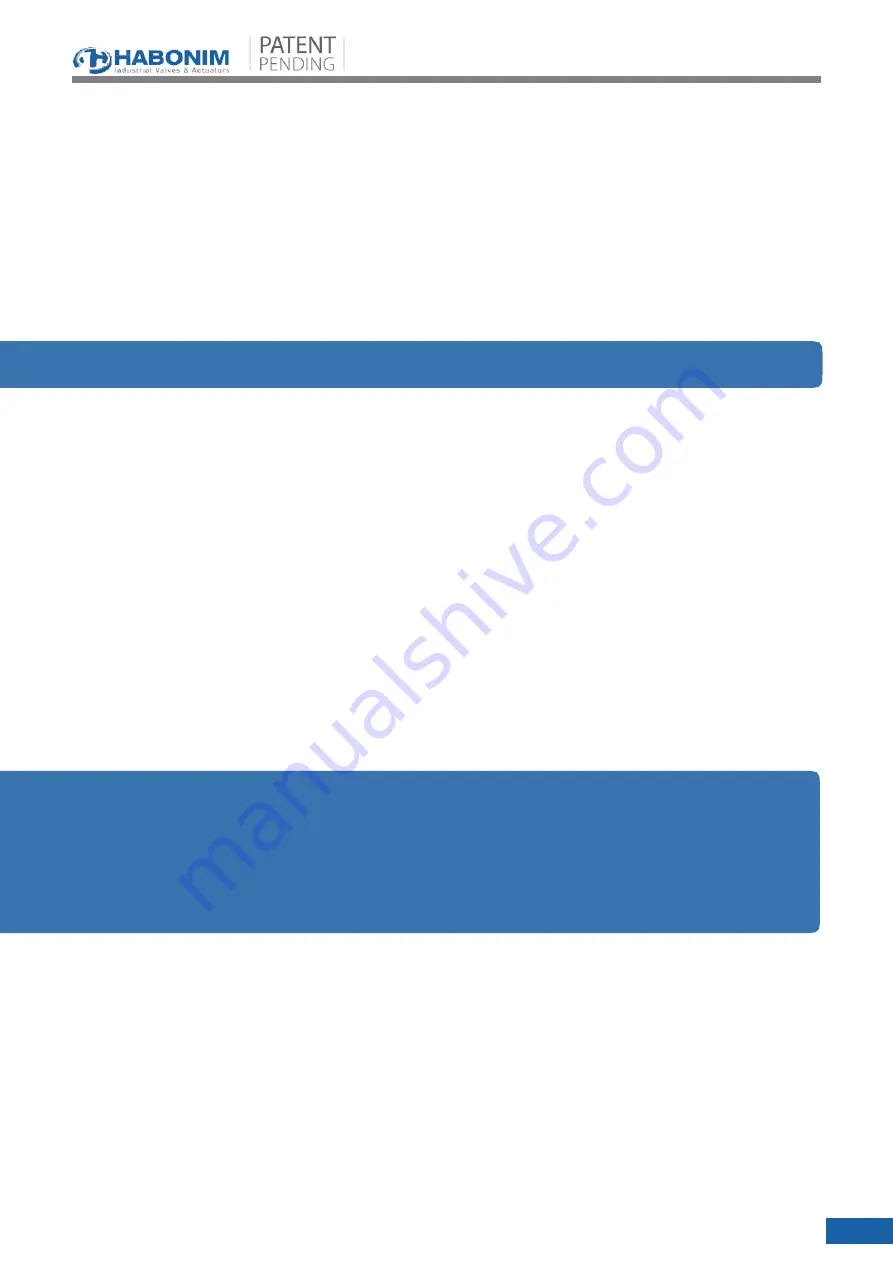
Top Entry Trunnion Mounted Cryogenic Ball Valves – C52
Valves Series
Top Entry Trunnion Mounted Cryogenic Ball Valves – C52
Valves Series
6
5.4.
Weld End Valves in-line - Extended Ends
5.4.1.
Welding of valves shall be performed by a qualified person according to the ASME Boiler Construction
Code Section IX. For valves to be welded within the EEA, refer to the requirements of ESR 3.1.2 of the
Pressure Equipment Directive 97/23/EC.
5.4.2.
Valves that will be welded directly to the line must be in the fully open position to protect the ball and
seats from excessive temperatures during the welding procedures.
5.4.3.
It is recommended to remove the valve wrench during the welding procedure. Protect or remove
actuators from weld splatter or arc strikes. Valves in the “Fail Close” position should be cycled to the
open position.
5.4.4.
Use a temperature stick and a wet cloth wrapped around the center section to prevent overheating.
WARNING: DO NOT heat the center section over 150°C (300°F).
5.4.5.
Align valve to pipe line, ensuring proper fit to minimize pipe load. Tack weld only.
5.4.6.
Complete welding in small segments. Allow enough time for cooling between each segment.
5.4.7.
After completing the welds, wait for the valve to cool below 90°C (200°F).
5.4.8.
Replace the wrench or actuator. It is recommended not to rotate the valve to the closed position
before flushing the line.
5.5.
Flanged Valves
5.5.1.
Before installing the valves, make sure the flanges and the pipe are free from grit, dirt or burrs.
5.5.2.
The flanges must be aligned and parallel with the correct distance to allow the valve face-to-face
dimension and gaskets to fit between.
5.5.3.
Insert the valve between the flanges. If tilting or levering of the flanges is required, avoid harming the
sealing surfaces of the flanges.
5.5.4.
Align the valve and the pipe counter flanges and insert at least 2 bolts at the lowest side of the flange
to support the gaskets.
5.5.5.
Slide the gaskets between the flanges. Insert the remaining bolts and thread the nuts hand tight.
5.5.6.
Before tightening the bolts, make sure the gaskets are aligned with the raised face of the flanges.
5.5.7.
Tighten the flange bolts, with a torque values determined by the gasket manufacturer, other variables
like gasket type and material, bolt, flange and lubricant affect the tightening torque values.
IMPORTANT: the tightening torque selected must be high enough to ensure
adequate strain (stretch) in the bolt, but not so high as to cause the material to
be taken beyond yield into the plastic response region. If the initial bolt stress
is too low the total amount of strain (stretch in the bolt) is low and under these
circumstances any subsequent reduction in thickness of the gasket due to creep will
quickly result in loss of bolt strain and subsequent leakage.
5.5.8.
It is recommended to use ring spanners to tighten and support the bolts and nuts.
5.5.9.
N
ote:
bolts tightening must be uniform in order to create a parallel movement of the two flanges
and uniform deformation of the gasket in between them.
5.5.10.
Before flushing the line, be sure the valves are in the fully open position. Fail-to-close actuated valves
should be operated to the open position for flushing.
5.5.11.
Before pressure testing the valves, bring the valves to the half open position to ensure pressure
reaches the stem seals and to avoid unnecessary loading of the seats. Fail-to-close actuated valves
should be brought to the half-open position.