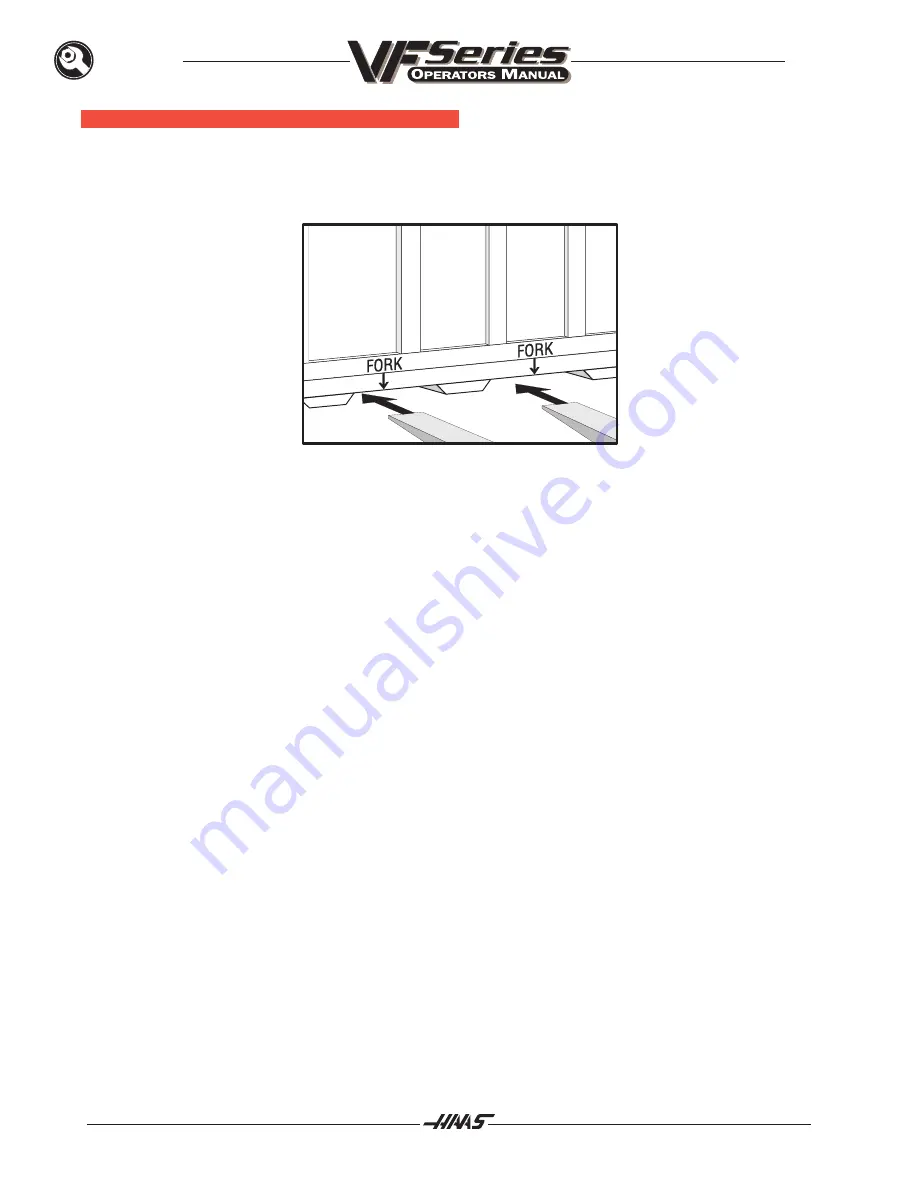
1 0
INSTALLATION
June 1999
96-8000
M
OVING
T
HE
C
RATE
CAUTION!
THE VMC CRATE CAN ONLY BE MOVED WITH A FORKLIFT.
CAUTION
! The fork positions are marked on the crate. (Also, note that there are three skids at each side of
the pallet. The heavy part of the machine [the back] is positioned over the two skids that are closest together.)
If the fork positions are ignored, there is a good chance that the retaining bolts will be sheared off by the forks
and also that the machine will tip over when it is picked up.
Содержание VF Series
Страница 1: ...1 INSTALLATION June 1999 96 8000 INSTALLATION FOR THE VF SERIES MILL ...
Страница 4: ...4 INSTALLATION June 1999 96 8000 MACHINE FOOTPRINTS Dimensions are in inches ...
Страница 5: ...5 INSTALLATION June 1999 96 8000 ...
Страница 6: ...6 INSTALLATION June 1999 96 8000 ...
Страница 20: ...2 0 INSTALLATION June 1999 96 8000 ANCHOR PATTERN VF 0 E 1 2 ...
Страница 21: ...2 1 INSTALLATION June 1999 96 8000 MACHINE FOOTPRINT VF 0 E 1 2 ...
Страница 22: ...2 2 INSTALLATION June 1999 96 8000 ANCHOR PATTERN VF 3 4 ...
Страница 23: ...2 3 INSTALLATION June 1999 96 8000 MACHINE FOOTPRINT VF 3 4 ...
Страница 24: ...2 4 INSTALLATION June 1999 96 8000 ANCHOR PATTERN VF 5 ...
Страница 25: ...2 5 INSTALLATION June 1999 96 8000 MACHINE FOOTPRINT VF 5 ...
Страница 27: ...2 7 INSTALLATION June 1999 96 8000 MACHINE FOOTPRINT VF 6 ...
Страница 28: ...2 8 INSTALLATION June 1999 96 8000 MACHINE FOOTPRINT VF 7 ...
Страница 31: ...3 1 INSTALLATION June 1999 96 8000 MACHINE FOOTPRINT VF 8 ...
Страница 32: ...3 2 INSTALLATION June 1999 96 8000 MACHINE FOOTPRINT VF 9 ...
Страница 138: ...138 OPERATION 96 8000 June 1999 THIS PAGE INTENTIONALLY LEFT BLANK ...
Страница 153: ...96 8000 CUTTER COMPENSATION 153 June 1999 ...
Страница 154: ...154 CUTTER COMPENSATION 96 8000 June 1999 ...
Страница 156: ...156 CUTTER COMPENSATION 96 8000 June 1999 CUTTER COMPENSATION ENTRY Yasnac ...
Страница 157: ...96 8000 CUTTER COMPENSATION 157 June 1999 CUTTER COMPENSATION ENTRY Fanuc style ...
Страница 220: ...220 M CODES 96 8000 June 1999 THIS PAGE INTENTIONALLY LEFT BLANK ...
Страница 270: ...270 SETTINGS June 1999 96 8000 THIS PAGE INTENTIONALLY LEFT BLANK ...
Страница 306: ...306 PARAMETERS June 1999 96 8000 THIS PAGE INTENTIONALLY LEFT BLANK ...
Страница 332: ...332 ALARMS June 1999 96 8000 THIS PAGE INTENTIONALLY LEFT BLANK ...
Страница 416: ...416 OPTIONS 96 8000 June 1999 ...
Страница 433: ...96 8000 433 OPTIONS June 1999 Recovery from an E Stop initiated during a pallet change ...
Страница 435: ...96 8000 435 OPTIONS June 1999 APC DIMENSIONS VF 3 4 WITH APC FOOTPRINT ...
Страница 437: ...96 8000 437 OPTIONS June 1999 APC PALLET CLEARANCES ...
Страница 443: ...TECHNICAL REFERENCE 443 June 1999 96 8000 SIDE MOUNT TOOL CHANGER RECOVERY FLOW CHART ...
Страница 477: ...Assembly Drawings June 1999 477 96 8000 ASSEMBLY DRAWINGS ...
Страница 478: ...Assembly Drawings June 1999 478 96 8000 VF O 1 Base ...
Страница 479: ...Assembly Drawings June 1999 479 96 8000 VF O 1 Column ...
Страница 480: ...Assembly Drawings June 1999 480 96 8000 VF O 1 Saddle ...
Страница 481: ...Assembly Drawings June 1999 481 96 8000 VF 3 Base ...
Страница 482: ...Assembly Drawings June 1999 482 96 8000 VF 3 Column ...
Страница 483: ...Assembly Drawings June 1999 483 96 8000 VF 3 Saddle ...
Страница 484: ...Assembly Drawings June 1999 484 96 8000 VF 6 Base ...
Страница 485: ...Assembly Drawings June 1999 485 96 8000 VF 6 Column ...
Страница 486: ...Assembly Drawings June 1999 486 96 8000 VF 6 Saddle ...
Страница 487: ...Assembly Drawings June 1999 487 96 8000 VF 8 Base ...
Страница 488: ...Assembly Drawings June 1999 488 96 8000 VF 8 Column ...
Страница 489: ...Assembly Drawings June 1999 489 96 8000 VF 8 Saddle ...
Страница 490: ...Assembly Drawings June 1999 490 96 8000 VF 10 Base ...
Страница 491: ...Assembly Drawings June 1999 491 96 8000 VF 10 Column ...
Страница 492: ...Assembly Drawings June 1999 492 96 8000 27 31 31 27 18 42 18 5 12 31 18 45 37 36 45 1 8 28 24 44 13 43 32 VF 10 Column ...
Страница 493: ...Assembly Drawings June 1999 493 96 8000 VF 10 Column ...
Страница 495: ...Assembly Drawings June 1999 495 96 8000 Tool Changer Assembly VF 3 4 ...
Страница 496: ...Assembly Drawings June 1999 496 96 8000 Tool Changer Assembly VF 3 4 ...
Страница 497: ...Assembly Drawings June 1999 497 96 8000 Tool Changer Assembly VF 6 10 ...
Страница 498: ...Assembly Drawings June 1999 498 96 8000 Tool Changer Assembly VF 6 10 ...
Страница 499: ...Assembly Drawings June 1999 499 96 8000 50 Taper Tool Changer Assembly ...
Страница 500: ...Assembly Drawings June 1999 500 96 8000 50 Taper Tool Changer Assembly ...
Страница 501: ...Assembly Drawings June 1999 501 96 8000 20 Pocket Tool Changer VF O 1 2 ...
Страница 502: ...Assembly Drawings June 1999 502 96 8000 20 Pocket Tool Changer VF O 1 2 ...
Страница 504: ...Assembly Drawings June 1999 504 96 8000 32 Tool Carousel Assembly Assembly CT VF 3 10 ...
Страница 505: ...Assembly Drawings June 1999 505 96 8000 50 Taper Carousel Assembly CT VF 6 10 ...
Страница 506: ...Assembly Drawings June 1999 506 96 8000 VF 1 11 Gearbox Assembly 15 HP ...
Страница 507: ...Assembly Drawings June 1999 507 96 8000 VF 1 11 Gearbox Assembly 15 HP ...
Страница 508: ...Assembly Drawings June 1999 508 96 8000 VF 1 11 Gearbox Assembly HT10K ...
Страница 509: ...Assembly Drawings June 1999 509 96 8000 VF 1 11 Gearbox Assembly HT10K ...
Страница 510: ...Assembly Drawings June 1999 510 96 8000 VF 1 11 Gearbox Assembly HT10K TSC ...
Страница 512: ...Assembly Drawings June 1999 512 96 8000 Spindle Assembly 7 5 ...
Страница 513: ...Assembly Drawings June 1999 513 96 8000 Spindle Assembly 7 5K TSCHP ...
Страница 514: ...Assembly Drawings June 1999 514 96 8000 10K Spindle Assembly ...
Страница 515: ...Assembly Drawings June 1999 515 96 8000 10K 12K Spindle Assembly ...
Страница 517: ...Assembly Drawings June 1999 517 96 8000 Spindle Assembly VF0 10K TSCHP ...
Страница 518: ...Assembly Drawings June 1999 518 96 8000 Tool Release Piston Assembly ...
Страница 520: ...Assembly Drawings June 1999 520 96 8000 50 Taper Tool Release Piston ...
Страница 521: ...Assembly Drawings June 1999 521 96 8000 50 Taper Tool Release Piston ...
Страница 522: ...Assembly Drawings June 1999 522 96 8000 TSCHP Tool Release Piston Assembly ...
Страница 523: ...Assembly Drawings June 1999 523 96 8000 TSCHP Tool Release Piston Assembly ...
Страница 524: ...Assembly Drawings June 1999 524 96 8000 32mmBall Screw Assembly ...
Страница 526: ...Assembly Drawings June 1999 526 96 8000 50mm Ball Screw Assembly ...
Страница 527: ...Assembly Drawings June 1999 527 96 8000 30 1215 Coupling Assembly ...
Страница 528: ...Assembly Drawings June 1999 528 96 8000 30 1219 Coupling Assembly ...
Страница 530: ...Assembly Drawings June 1999 530 96 8000 30 1220P Coupling Assembly ...
Страница 531: ...Assembly Drawings June 1999 531 96 8000 30 1225 Coupling Assembly ...
Страница 532: ...Assembly Drawings June 1999 532 96 8000 APC Assembly ...
Страница 533: ...Assembly Drawings June 1999 533 96 8000 APC Assembly ...
Страница 534: ...Assembly Drawings June 1999 534 96 8000 APC Assembly ...
Страница 535: ...Assembly Drawings June 1999 535 96 8000 VR Series Head Assembly ...
Страница 536: ...Assembly Drawings June 1999 536 96 8000 VR Series Head Assembly ...
Страница 537: ...Assembly Drawings June 1999 537 96 8000 VF Series Hydraulic Couterbalance System ...
Страница 538: ...538 ELECTRICAL DIAGRAMS June 1999 96 8000 ELECTRICAL WIRING DIAGRAMS ...
Страница 539: ...539 ELECTRICAL DIAGRAMS June 1999 96 8000 ...
Страница 540: ...540 ELECTRICAL DIAGRAMS June 1999 96 8000 ...
Страница 541: ...541 ELECTRICAL DIAGRAMS June 1999 96 8000 ...
Страница 542: ...542 ELECTRICAL DIAGRAMS June 1999 96 8000 ...
Страница 543: ...543 ELECTRICAL DIAGRAMS June 1999 96 8000 ...
Страница 544: ...544 ELECTRICAL DIAGRAMS June 1999 96 8000 ...
Страница 545: ...545 ELECTRICAL DIAGRAMS June 1999 96 8000 ...
Страница 546: ...546 ELECTRICAL DIAGRAMS June 1999 96 8000 ...
Страница 547: ...547 ELECTRICAL DIAGRAMS June 1999 96 8000 ...
Страница 548: ...548 ELECTRICAL DIAGRAMS June 1999 96 8000 ...
Страница 549: ...549 ELECTRICAL DIAGRAMS June 1999 96 8000 ...
Страница 550: ...550 ELECTRICAL DIAGRAMS June 1999 96 8000 ...
Страница 551: ...551 ELECTRICAL DIAGRAMS June 1999 96 8000 ...
Страница 552: ...552 ELECTRICAL DIAGRAMS June 1999 96 8000 ...
Страница 553: ...553 ELECTRICAL DIAGRAMS June 1999 96 8000 ...
Страница 554: ...554 ELECTRICAL DIAGRAMS June 1999 96 8000 ...
Страница 555: ...555 ELECTRICAL DIAGRAMS June 1999 96 8000 ...
Страница 556: ...556 ELECTRICAL DIAGRAMS June 1999 96 8000 ...
Страница 557: ...557 ELECTRICAL DIAGRAMS June 1999 96 8000 ...
Страница 558: ...558 ELECTRICAL DIAGRAMS June 1999 96 8000 ...
Страница 559: ...559 ELECTRICAL DIAGRAMS June 1999 96 8000 ...
Страница 560: ...560 ELECTRICAL DIAGRAMS June 1999 96 8000 ...
Страница 561: ...561 ELECTRICAL DIAGRAMS June 1999 96 8000 ...
Страница 562: ...562 ELECTRICAL DIAGRAMS June 1999 96 8000 ...
Страница 563: ...563 ELECTRICAL DIAGRAMS June 1999 96 8000 ...
Страница 564: ...564 ELECTRICAL DIAGRAMS June 1999 96 8000 ...