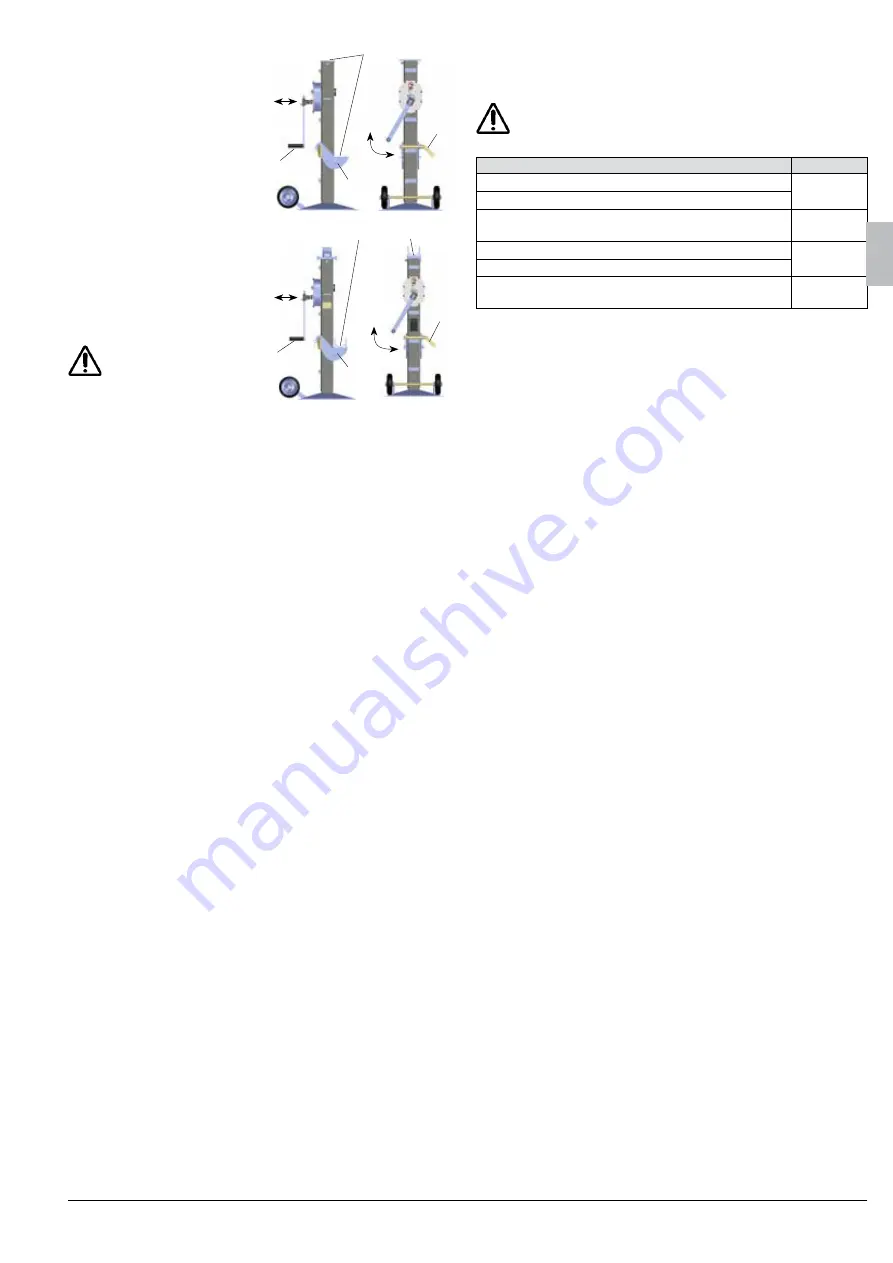
094025_o_de_gb_fr_dk_wkstwin_s
haacon hebetechnik gmbh T49 (0) 9375 - 84-0 Fax +49 (0) 9375 - 84-66
6. OpERATiOn
Loads can be raised and lowered
only in low gear.
Raised / lowered:
Turn the hand crank clockwise
when lifting.
Turn the hand crank anticlockwise
when lowering.
Switching to rapid traverse gear:
Pull the crank out until it reaches the
stop.
Switching to load gear:
Push the crank in,
the switch lock must engage.
Adjusting the lifting claw:
The hoist claw can be positioned in
four fixed positions on the shaft.
Pull the clip connector out, remove
the socket pin and adjust the lifting
claw to the required height. After
attaching the lifting claw, secure the
socket pin with a clip connector.
Support loads safely!
The load capacity of the
ground must be at least
25 kN/cm².
Observe the load specifications on the vehicle’s axles.
Attach the load as close to the load attachment surfaces as
possible.
Secure the height-adjustable lifting claw with a spring clip after attaching.
After lifting a little, check that the load has been picked up safely.
During lifting and lowering movements observe the load and lifting
equipment at all times. Do not leave raised loads unattended.
Remove the crank after reaching the required working position in order
to prevent the unit being actuated inadvertently.
The crank force increases significantly when the unit’s maximum posi-
tions are reached. Stop lifting.
Do not use the unit outdoors if the wind is gusty. Set down loads that
have already been lifted or secure them accordingly.
7. ChAnGinG ThE SET-up lOCATiOn
The unit is equipped with wheels due to its weight.
The unit is mobile according to the barrow principle.
8. TESTinG
The equipment must be inspected in accordance with the conditions of
use and the operating conditions at least once per year by an authorised
person for testing per TRBS 1203 (Technical expert) (testing per BetrSi-
chV, §10, sect.2 represents implementation of EC Directives 89/391/
EEC and 2009/104/EC and the annual occupational safety inspection per
DGUV-V 54, §23, sect. 2 and DGUV-G 309-007).
These inspections must be documented:
– Before commissioning.
– After significant alterations before recommissioning.
– At least once per year.
– In the event of unusual occurrences arising that could have detrimen-
tal effects on the safety of the winch (extraordinary tests, e.g. after a
long period of inactivity, accidents, natural events).
– After repair works that could have an influence on the safety of the
winch.
Technical experts are persons, who have sufficient knowledge based
on their specialist training and experience, in the areas of winches, lift
and pull systems, and familiarity with the relevant official occupational
health and safety rules, accident prevention regulations, guidelines and
generally accepted engineering rules (e.g. EN standards), to evaluate
the operational safety of winches, and lift and pull systems. Authorised
persons for testing are selected and commissioned by the operator of
the unit.
carnk
up
down
socket
pin
load bearing surfaces
Type 1094
crank
up
down
socket
pin
load bearing surfaces
Type 1095
lifting claw
lifting claw
9. MAinTEnAnCE RECOMMEnDATiOn
The operator determines the intervals themselves based on frequency
of use and the operating conditions.
– Regular cleaning, no steam jets!
– General overhaul by the manufacturer after 10 years at the latest.
CAuTiOn!
Only perform inspection, maintenance and repair work on an
unloaded hoist. Only allow work on brakes and locks to be per-
formed by qualified specialist personnel.
Maintenance and inspection work
intervals
Visual and functional tests
Before
every use
Brake function under load
Relubrication (lubricating nipple), while doing so deploy
and retract the unit over its full stroke length
Every 6
months
Check type plate for legibility
Annually
Professional inspection according to DGUV-V 54
Check gear parts, replace if necessary, lubricate
Every 2 - 5
years
lubricant recommendations:
Multi-purpose grease per DIN 51502 K3K-20
10. SpARE pARTS
The following data should be given with each order:
– Type number and serial number of the equipment / Pos. and Part
number.
11. DiSASSEMBly, DiSpOSAl
– Make sure to observe the safety instructions.
– Dispose of the equipment and the substances within it in an environ-
mentally responsible manner.
GB