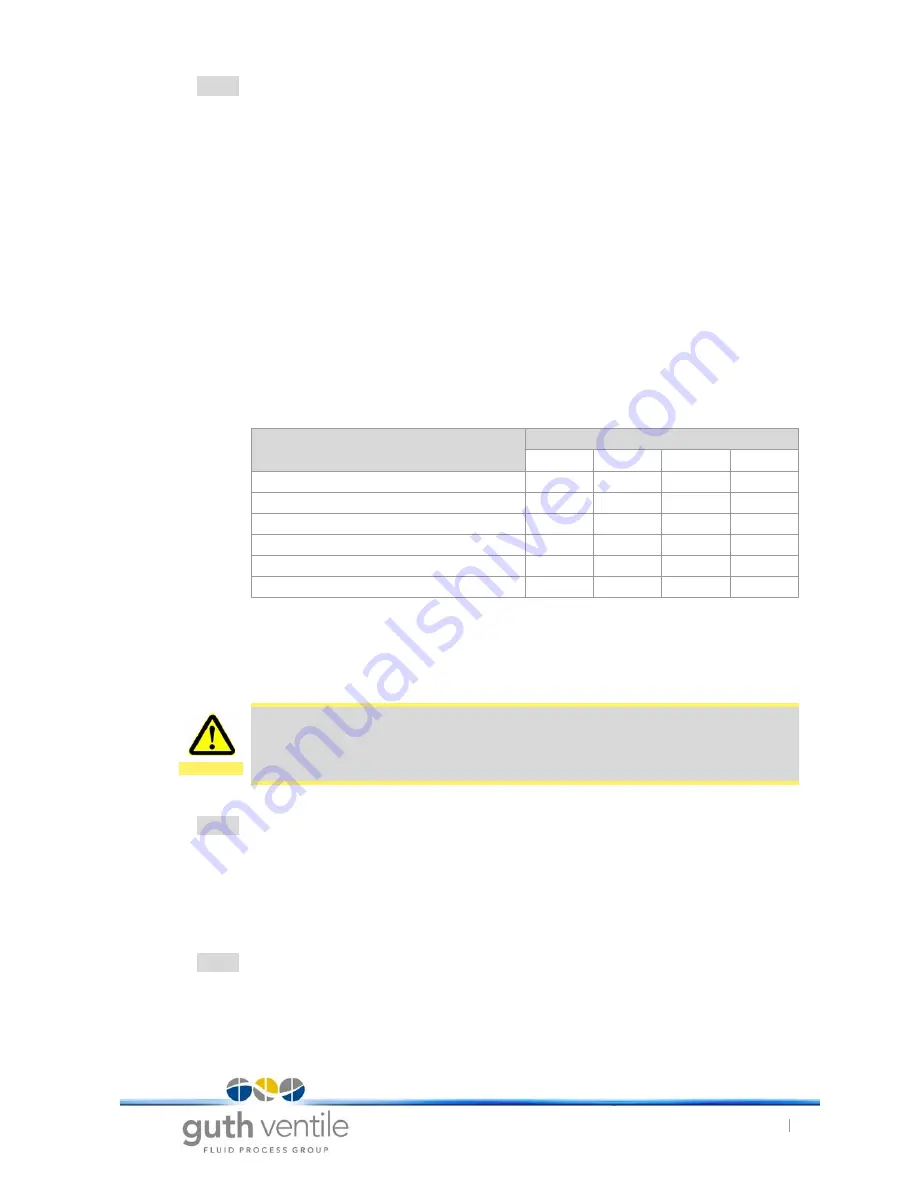
18.4.17
Modulating Valves Type: VSR
4. Installation of the Modulating valve
11
4 . 4
Welding seam preparation
Welding seam preparation:
The plant pipe ends to be welded are to be sawn flush and at right angles and deburred. Allign the
housing welding ends to the pipe ends (radially and axially flush align).
Prior to welding in the fitting:
The entire valve insert (actuator, lantern and spindle) is to be removed from the housing. If leakage
valves or housing inserts are present, these must be disassembled as well. During the welding work
no seals may be present next to or in the valve housing.
Welding-in instructions:
Recommended welding filler materials
Tab. 3 Examples for possible welding filler materials
Welding seam treatment:
As a rule, no reworking of the weld seam is needed inside the connecting pipe if the weld has been
carried out properly. For the outside surface of the connecting pipe, we recommend passivating the
weld seam (pickling using pickling paste).
4 . 5
Pneumtatic connection
GUTH multi-turn actuators are delivered as standard with a pneumatic connector for standard 4 mm
pneumatic hoses. In case of high ambient temperatures, a PP quality hose is recommended.
Please refer to the corresponding data sheets to obtain the required air pressure. For reasons of
functional safety and service life of the regulating device, the air quality should be high i.e. dry, de-
oiled and filtered to 5 µm. For oiled compressed air the quality must be according to ISO VG32
Class 1.
4 . 6
Electrical connection
Connection to be carried out according to the operating instructions of the respective control head
or electrical attachment components.
Scope of usage:
Welded connections of welded-in fittings with pipes according to DIN
11850. We recommend preparing the seam according to DIN 2559.
Welding procedure:
TIG (Tungsten Inert Gas welding), as appropriate using orbital welding
technique — flood pipe internally with forming gas so as to displace the
air from the welding area.
certified Personnel:
To prevent damage, welding should be undertaken by certified person-
nel (EN287).
Plant part
Filler material
1.4316
1.4430
1.4404
1.4519
1.4301
x
1.4306
x
1.4401
x
1.4404
x
1.4435
x
x
x
1.4571
x
x
CAUTION
• After welding, the valve housing must be thoroughly cleaned. Welding residue and dirt particles
can cause damage to the seals.
www.sks-online.com
www.sks-webshop.com