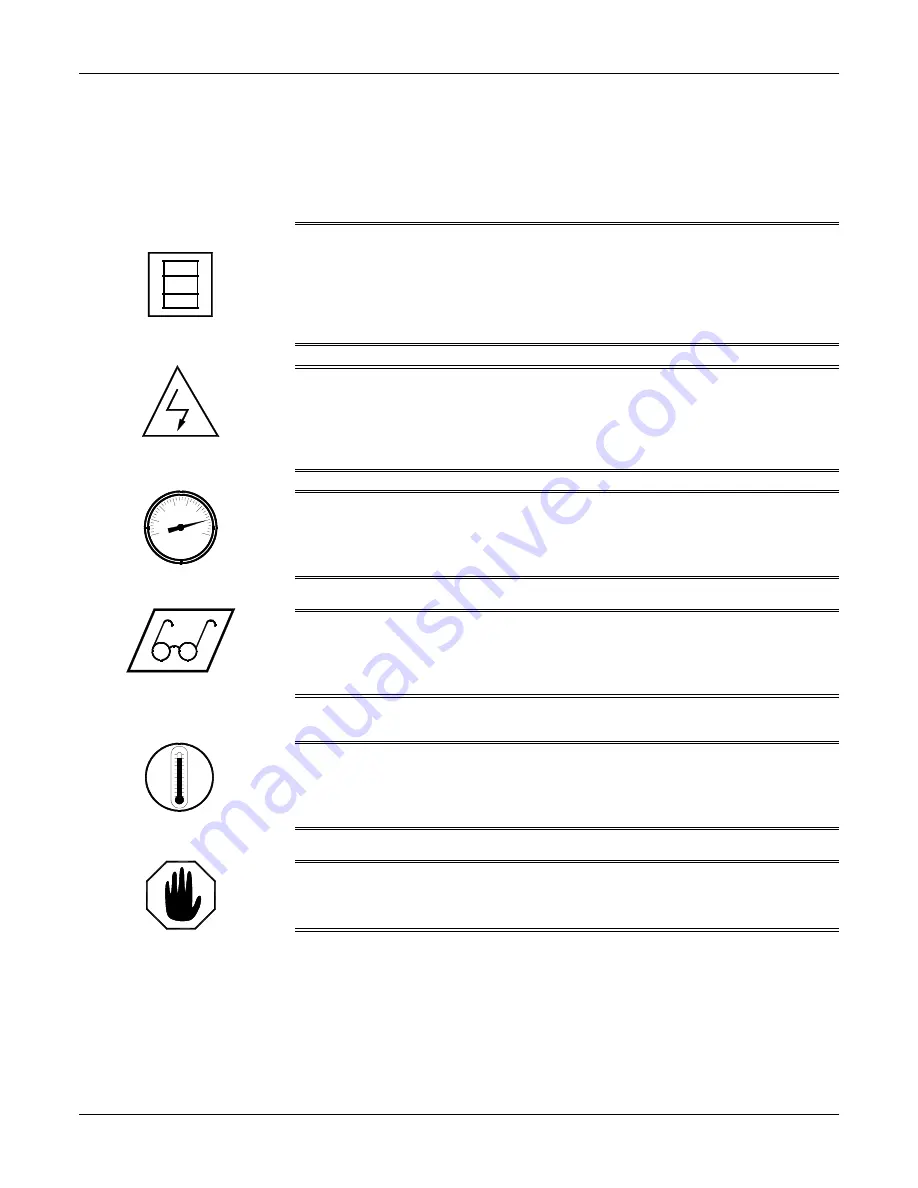
Operating Manual
General Safety Information
12/6/00
7
Operational Safety Procedures
This safety information is not repeated in this manual. The symbols pertaining to this
information will appear where appropriate to alert the operator to potential hazards.
Solvents and Chemicals
WARNING: T
HE SOLVENTS AND CHEMICALS USED WITH THIS EQUIPMENT EXPOSE THE
OPERATOR TO CERTAIN HAZARDS
. A
DEQUATE PERSONAL PROTECTIVE MEASURES MUST BE
TAKEN SO AS TO AVOID EXCEEDING THE
T
HRESHOLD
L
IMIT
V
ALUE
(TLV)
OF THE PRODUCTS
BEING USED
,
AS ESTABLISHED BY THE
O
CCUPATIONAL
S
AFETY AND
H
EALTH
A
DMINISTRATION
(OSHA)
OR OTHER QUALIFIED AGENCY
. I
NFORMATION CONCERNING PERSONAL PROTECTION
AND PROPER HANDLING SHOULD BE OBTAINED FROM THE SUPPLIER OF SUCH CHEMICALS
.
High Voltage
WARNING: T
O PREVENT SERIOUS BODILY INJURY FROM ELECTRICAL SHOCK
,
NEVER OPEN
THE ELECTRIC CONSOLES OR OTHERWISE SERVICE THIS EQUIPMENT AND
/
OR EQUIPMENT USED
WITH IT BEFORE SWITCHING OFF THE MAIN POWER DISCONNECT AND INTERRUPTING SUPPLY
VOLTAGE AT THE SOURCE
. T
HE ELECTRICAL SERVICE MUST BE INSTALLED AND MAINTAINED BY
A QUALIFIED ELECTRICIAN
.
High Pressure
WARNING: T
HIS EQUIPMENT HAS OR IS USED WITH EQUIPMENT THAT HAS HYDRAULIC
COMPONENTS CAPABLE OF PRODUCING UP TO
3500
PSI
. T
O AVOID SERIOUS BODILY INJURY
FROM HYDRAULIC INJECTION OF FLUID
,
NEVER OPEN ANY HYDRAULIC CONNECTIONS OR
SERVICE HYDRAULIC COMPONENTS WITHOUT BLEEDING ALL PRESSURES TO ZERO
.
Personal Protective
Equipment
WARNING: T
O AVOID SERIOUS BODILY INJURY
,
PROPER PROTECTIVE GEAR MUST BE WORN
WHEN OPERATING
,
SERVICING
,
OR BEING PRESENT IN THE OPERATIONAL ZONE OF THIS
EQUIPMENT
. T
HIS INCLUDES
,
BUT IS NOT LIMITED TO
,
EYE AND FACE PROTECTION
,
GLOVES
,
SAFETY SHOES
,
AND RESPIRATORY EQUIPMENT AS REQUIRED
.
High Temperature
WARNING: T
HIS EQUIPMENT HAS OR IS USED WITH EQUIPMENT THAT HAS HIGH
TEMPERATURE COMPONENTS SUCH AS PRIMARY HEATERS AND HEATED HOSES
. T
O PREVENT
SERIOUS BODILY INJURY FROM HOT FLUID OR HOT METAL
,
NEVER ATTEMPT TO SERVICE THE
EQUIPMENT BEFORE ALLOWING IT TO COOL
.
Warning
WARNING: F
AILURE TO READ AND FOLLOW THIS SAFETY INFORMATION MAY RESULT IN
PERSONAL INJURY AND
/
OR DAMAGE TO THE EQUIPMENT FROM ONE OR MORE OF THE ABOVE
LISTED HAZARDS
Содержание GAP
Страница 26: ...GAP Spray Gun 26 35943 1 Issue 5 NOTES ...