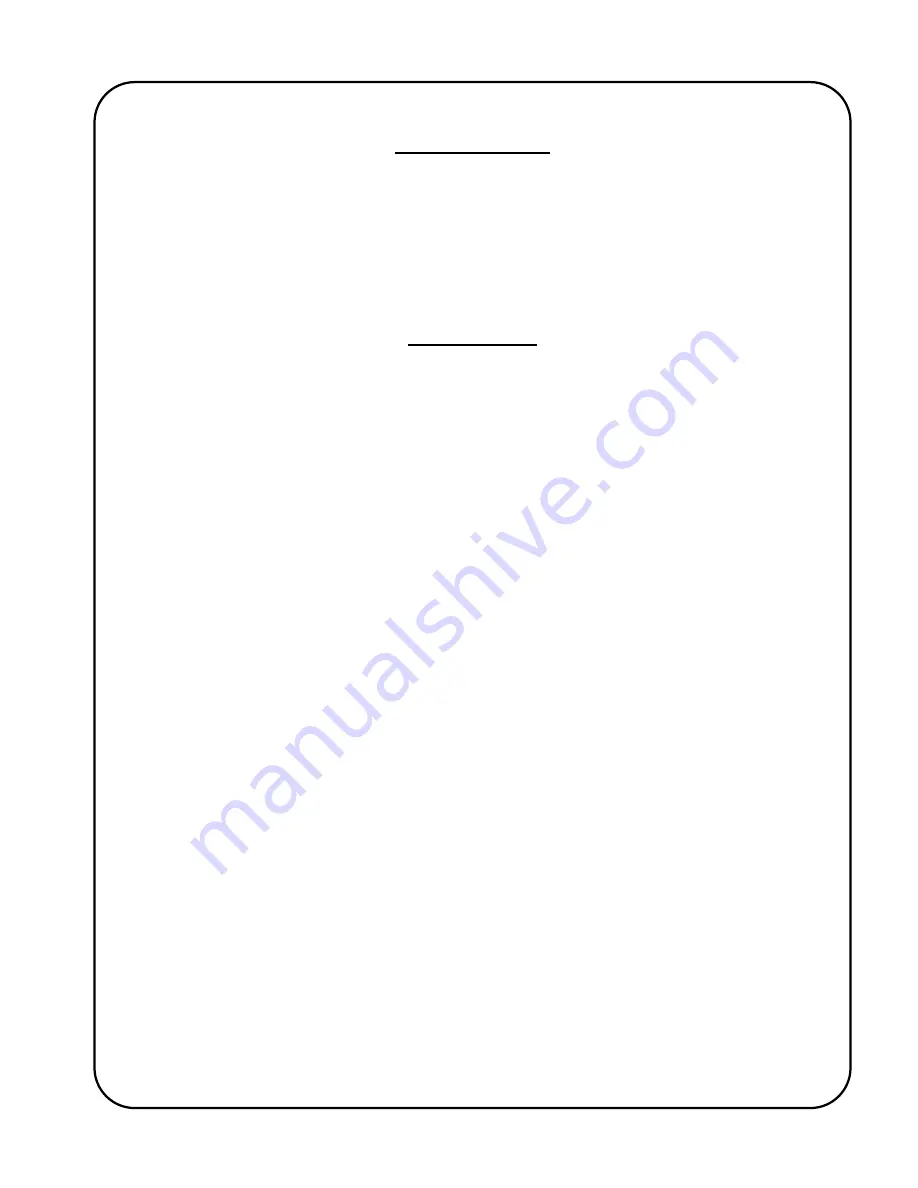
7
MAINTENANCE
The Gullco welding positioner is a heavy duty, robust piece of equipment, and under normal
conditions, it will give you years of trouble free service, if it is operated within the limits of its
expected use and if the following maintenance points are adhered to:
Clean all excess dust, spatter, slag etc. from the positioner regularly. Do not allow any foreign
material to impede operation. Pay particular attention to the following paragraph regarding
inspection.
INSPECTION
The welding ground should be inspected for a secure, clean electrical contact from the welding
power source to the grounding bracket of the positioner before the start of each new day of welding.
The fasteners of the positioner grounding assembly should be inspected for security. A visual
check of the grounding block, springs and ground strap should be performed to ensure that the
ground block is seating flat against a clean, spindle flange and that there are no signs of obvious
damage occurring.
Frequent inspections should be performed with respect to the stability and rigidity of the positioner
mounting. Also, the drive sprockets, chain and spindle bearings should be inspected for signs of
wear and replaced if necessary.
The tension of the drive chain should be inspected and adjusted as necessary. The drive chain
tension is adjusted by loosening off the four (4) motor mounting button headed cap screws (item#
37 in drawing GP-200 & item# 38 in drawing GPP-200). Then loosen the jam nut and adjust the
motor tensioning screw as required (items # 31 & 43 in drawing GP-200 & items 32 & 44 in drawing
GPP-200). Once the desired tension has been set, re-tighten the jam nut and the four (4) motor
mounting screws.
WARNING!
A small amount of radial backlash on the spindle is inherent in the design of the
Positioner. Do not over-tension the drive chain in an attempt to remove this backlash
as this will cause the motor to overload and possibly result in gear-motor failure and
will invalidate the Gullco warranty.
The tachometer feed-back encoder sensor assembly located on the back of the motor should be
inspected for dirt accumulation and cleaned where necessary. It is common for the armature shaft
of a fatiguing motor to develop excessive axial float. This float sometimes causes the tachometer
feed-back sensor wheel to rub on one of the encoder sensor faces, causing damage and failure.
Check that the sensor disk is located centrally within the slot of the encoder sensor when the
armature shaft is pressed in and pulled out. Adjust as necessary. The frequency of this inspection
should increase with the accumulated use and or workload of the gear-motor.
At least once per year, the equipment should be taken out of service, stripped down and all moving
parts should be cleaned, greased and inspected for wear and damage. All cables must be
inspected for breaks and abrasion and must be well secured. All damaged and worn parts should
be replaced, using genuine/authorized replacement parts only. All fastening devices should be
inspected for tightness.
NOTE:
These inspections should be performed with greater frequency if conditions and usage
requires.
Содержание , GPP-200
Страница 2: ......
Страница 6: ...4 GENERAL DIMENSIONS...
Страница 12: ...10 WELDING POSITIONER PARTS BREAKDOWN DRAWING GP 200 Specify model and serial numbers when ordering parts...
Страница 13: ...11 WELDING POSITIONER PARTS BREAKDOWN DRAWING GP 200...
Страница 15: ...13 WELDING GAS PURGE POSITIONER PARTS BREAKDOWN DRAWING GPP 200...
Страница 23: ......
Страница 24: ...www GULLCO com...
Страница 26: ......
Страница 35: ...T 9 GSP 1100 CONTROL ASSEMBLY BREAKDOWN SEE NOTES...
Страница 36: ...T 10 GSP 1100 CONTROL CIRCUIT BOARD SCHEMATIC DRAWING G1100 RB REV B...
Страница 38: ...www GULLCO com...