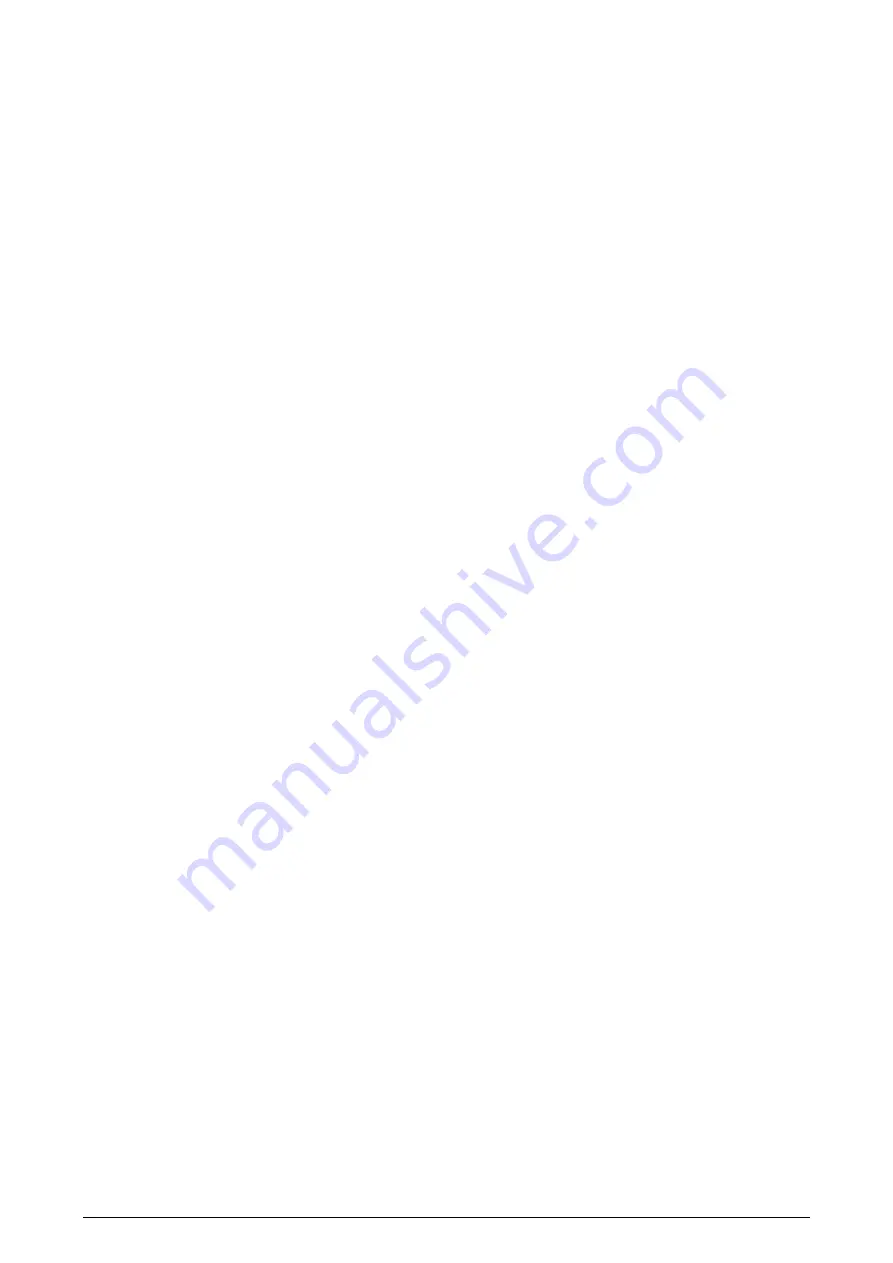
FST 75/150
260-2210-002 EN064
Page 23 / 37
Manual/automatic operation
A selection switch allows you to deactivate the automatic timed closing actions. It is possible to operate this
manually.
Running time control
An additional protective mechanism for drives with slip clutch. If the current motion exceeds the standard
running time, the door will be stopped.
Interlock-system
To build an interlock-system, every door has to be equiped with a controller FST75/150. By using the
connectors SLF both controllers are connected. The function is activated by the menu. (refer to menu
function). By doing this the doors only move in accordance to the limiting positions.
As an option it is possible to pass over an opening-command.
Example:
A forklift operator opens the first door using a rope switch and closes it using i.e. a photo cell in conjunction
with the function “closing after release 2 (NVZ)”. The forklift operator moves to door 2. As soon as door 1 has
closed, door 2 will open automatically by an opening commend from door 1 controller.
Cycle counter
The cycle counter is started upon initial operation and cannot be reset. Using the cycle counters, it is
possible to check or set the maintenance intervals for the unit.
Relays:
The FST 75/150 has integrated several functions for the output relays. These functions can be configured
independently and individually for each relay. In the standard design, a simple red/green traffic light control
with advance warning can be used. However, it is also possible to provide two “OPEN” position indicators,
for example. This is especially useful for meeting special requirements.
WARNING! Please observe the maximum load of the relays. Under certain circumstances, it may be
necessary to fuse protect the circuit.
Level adjusment (only in connection with DES)
The function cannot be applied to pneumatic systems. The FST 75/150 has the means to adapt the shut-
down point of the drive to the changing ground conditions (e.g. installation of the unit prior to the floor being
laid). At the same time, the shut-down point “close” undergoes constant change. The unit continues to edge
forwards until the safety edge activates. As soon as it activates, the shut-down point is once again brought a
little further forward.
Correcting the slowing down path (only in connection with DES)
The FST 75/150 incorporates a function that allows the open and close position of the unit to be kept
constant. The path between shutting down the contactors and the unit actually coming to a standstill
(slowing-down path) may vary depending on the external influences. This is possible, for example, in the
case of thermal loads or when the brake has worn down. The FST 75/150 registers any overrunning of the
programmed shut-down position and shuts down the contactors correspondingly sooner on the next run.
Warning!
This function may only be activated if the unit regularly undergoes maintenance! This must be
performed to ensure that the unit does not take on a dangerous state through prohibited wear and tear or a
lack of readjustment, for example (full loss of brake power).