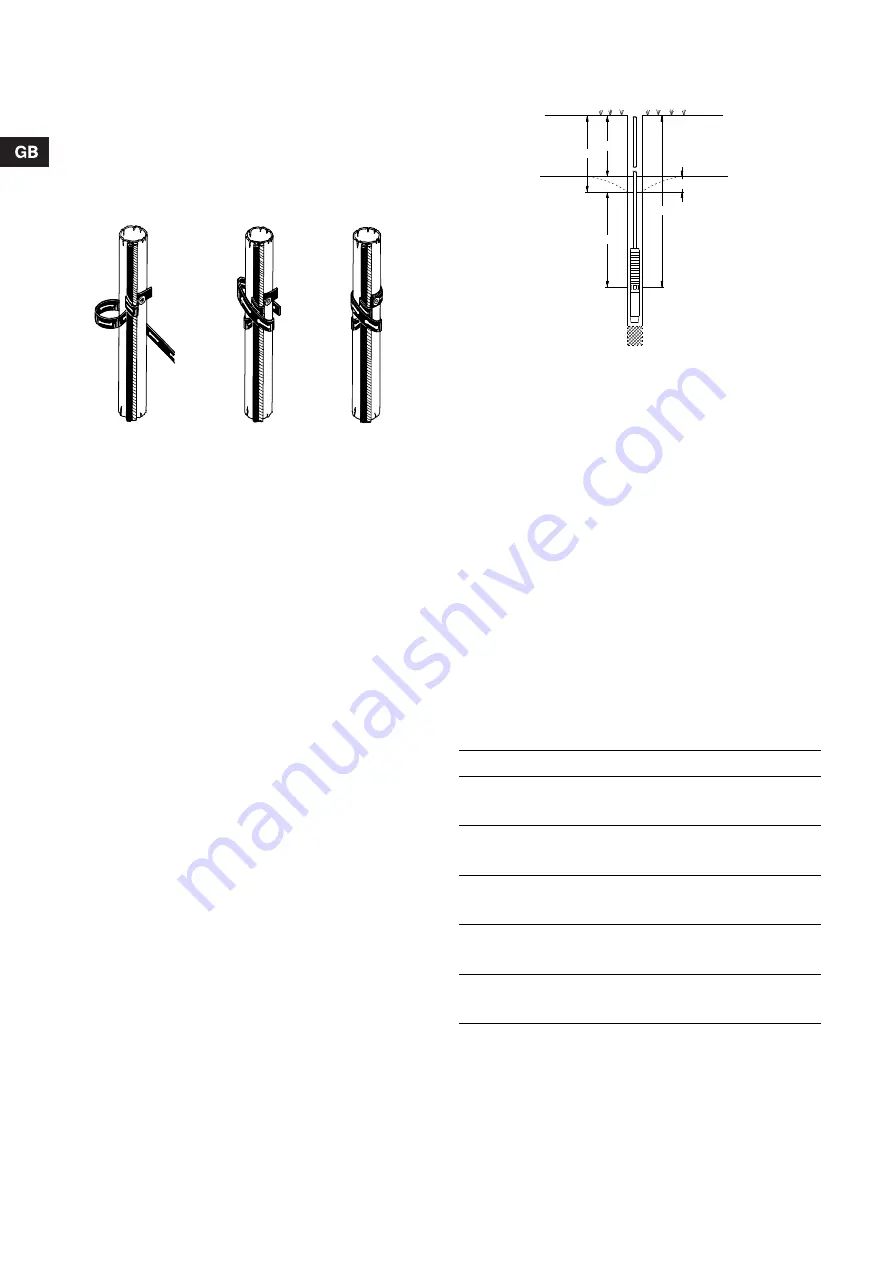
10
5.5 Cable fitting
Cable clips must be fitted every 3 metres to fix the submersible
drop cable and the straining wire, if fitted, to the riser pipe of the
pump.
GRUNDFOS supplies cable clip sets on request. The set consists
of a 1.5 mm thick rubber band and 16 buttons.
Cable fitting: Cut off the rubber band so that the piece with no
slit becomes as long as possible.
Insert a button in the first slit.
Position the wire alongside the submersible drop cable, fig. 12.
Fig. 12
Wind the band once around the wire and the cable.
Then wind it tightly at least twice around the pipe, wire and the
cable.
Push the slit over the button and then cut off the band.
Where large cable cross-sections are used, it will be necessary to
wind the band several times.
When flanged pipes are used, the cable clips should be fitted
above and below each joint.
5.6 Lowering the pump
It is recommended to check the borehole by means of an inside
calliper before lowering the pump to ensure unobstructed pas-
sage.
Lower the pump carefully into the borehole, taking care not to
damage the motor cable and the submersible drop cable.
Note: Do not lower or lift the pump by means of the motor cable.
5.7 Installation depth
The dynamic water level should always be above the suction
interconnector of the pump, see section 3.2 Positional require-
ments and fig. 13.
Minimum inlet pressure is indicated in the NPSH curve for the
pump.
The minimum safety margin should be 1 metre head.
It is recommended to install the pump so that the motor part is
above the well screen in order to ensure optimum cooling, see
section 3.4 Liquid temperatures/cooling.
When the pump has been installed to the required depth, the
installation should be finished by means of a borehole seal.
6. Start-up and operation
6.1 Start-up
When the pump has been connected correctly and it is sub-
merged in the liquid to be pumped, it should be started with the
discharge valve closed off to approx. 1/3 of its maximum volume
of water.
Check the direction of rotation as described in section
4.5.1 Checking of direction of rotation.
If there are impurities in the water, the valve should be opened
gradually as the water becomes clearer. The pump should not be
stopped until the water is completely clean, as otherwise the
pump parts and the non-return valve may choke up.
As the valve is being opened, the drawdown of the water level
should be checked to ensure that the pump always remains sub-
merged.
The dynamic water level should always be above the suction
interconnector of the pump, see section 3.2 Positional require-
ments and fig. 13.
Fig. 13
L1:
Minimum installation depth below dynamic water level.
Minimum 1 metre is recommended.
L2:
Depth to dynamic water level.
L3:
Depth to static water level.
L4:
Drawdown. This is the difference between the dynamic
and the static water levels.
L5:
Installation depth.
If the pump can pump more than yielded by the well, it is recom-
mended to fit the GRUNDFOS control unit, type CU 3, or some
other type of dry-running protection.
If no water level electrodes or level switches are installed, the
water level may be drawn down to the suction interconnector of
the pump and the pump will then draw in air.
Long time operation with water containing air may damage the
pump and cause insufficient cooling of the motor.
6.2 Operation
6.2.1 Minimum flow rate
To ensure the necessary cooling of the motor, the pump should
never be set so low that the cooling requirements specified in
section 3.4 Liquid temperatures/cooling cannot be met.
6.2.2 Frequency of starts and stops
TM
00 13
69 50
92
T
M
00
10
41
36
9
5
Motor type
Number of starts
MS 6000
Minimum 1 per year is recommended.
Maximum 30 per hour.
Maximum 300 per day.
MMS 6000
Minimum 1 per year is recommended.
Maximum 15 per hour.
Maximum 360 per day.
MMS 8000
Minimum 1 per year is recommended.
Maximum 10 per hour.
Maximum 240 per day.
MMS 10000
Minimum 1 per year is recommended.
Maximum 8 per hour.
Maximum 190 per day.
MMS 12000
Minimum 1 per year is recommended.
Maximum 5 per hour.
Maximum 120 per day.
L2
L3
L1
L5
L4
Содержание SP-G
Страница 1: ...SP G GRUNDFOS INSTRUCTIONS Installation and operating instructions ...
Страница 17: ...112 ...
Страница 18: ...113 ...
Страница 19: ...114 ...