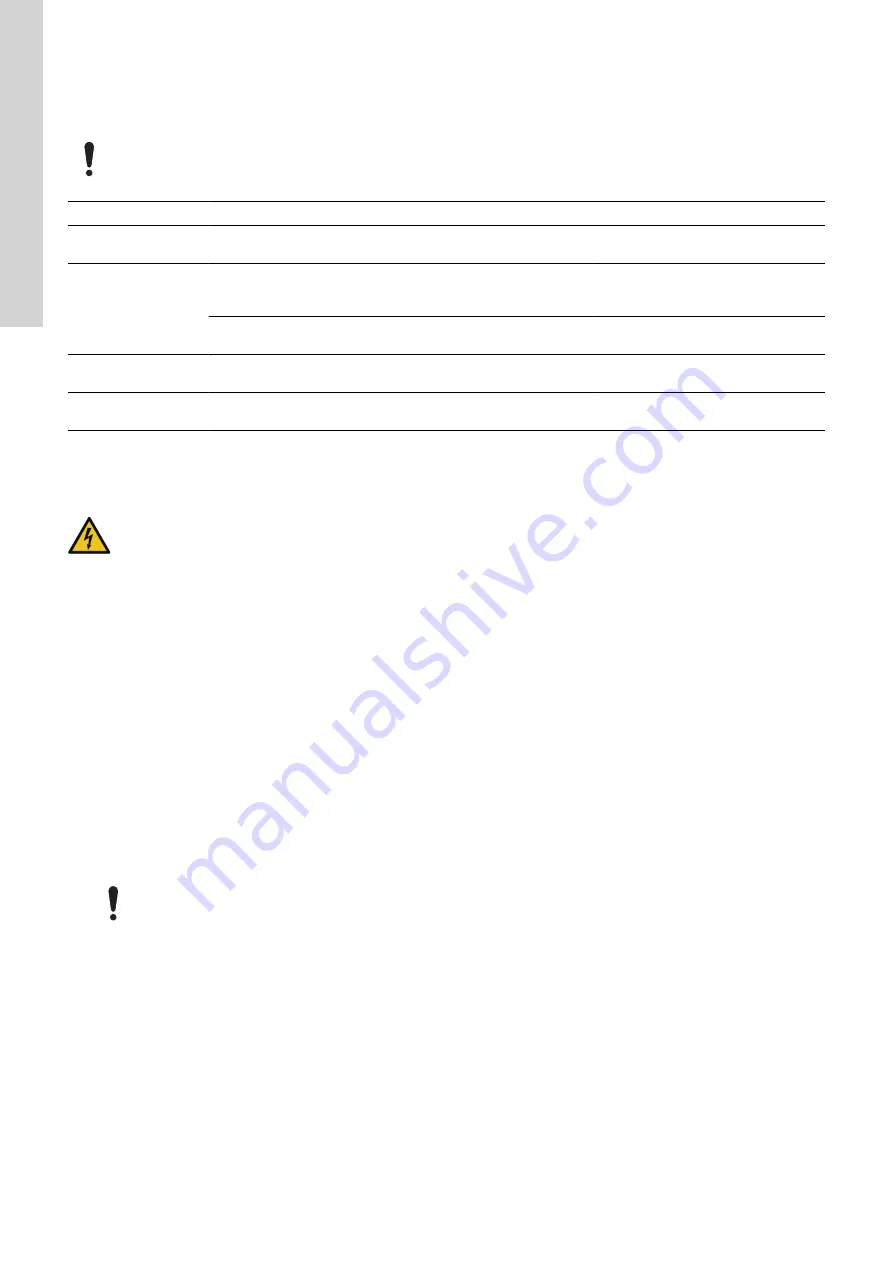
9.2 Basic maintenance schedule
In the following table, the basic maintenance activities are listed that help to avoid system faults and breakdowns. These activities must be
performed by trained users. The intervals for some of the tasks depend on the individual installation and must therefore be defined by the
operating company.
If the result of a check requires change, repair or adjustment which is not described in this manual, call certified service persons.
Interval
Component
Task
See section
To be defined by the
operating company
Polydos 412E system
Clean the surfaces of the system.
9.3 Cleaning the system surface
Weekly
Pressure reducing
valve
Check the strainer. Clean or replace if
necessary.
9.4 Checking and cleaning or replacing
the strainer in the pressure reducing
valve
Dissolving hopper
Check the dissolving hopper for deposits.
Clean if necessary.
9.5 Checking and cleaning the dissolving
hopper
Every 3 months
Dry-material feeder
Check the hopper, the dosing screw and the
dosing pipe for deposits. Clean if necessary.
9.6 Checking and cleaning the dry-
material feeder
In case of malfunction
Solenoid valve
Clean or replace the solenoid valve
9.7 Cleaning or replacing the solenoid
valve
9.3 Cleaning the system surface
WARNING
Electric shock
Death or serious personal injury
Liquids on electrical components can lead to electric
shock. Short circuits can cause damage to the equipment.
‐
Keep all electrical components dry.
‐
Do not use water or any other liquid to clean electrical
components or electrical lines of the system.
‐
Do not use a high-pressure cleaner.
1.
If necessary, clean all system surfaces with a dry and clean
cloth.
9.4 Checking and cleaning or replacing the strainer in
the pressure reducing valve
1.
Check the strainer visually via the transparent cover at the
bottom of the pressure reducing valve.
Cleaning/replacing procedure
2.
Switch off the main switch on the control cabinet.
a. Make sure the main switch cannot be switched on
accidentally.
3.
Put on the stipulated personal protective equipment. Observe
the chemical manufacturer's safety data sheets (SDS) and
safety instructions of the used chemicals.
4.
Close the shut-off valve upstream the pressure reducing valve.
5.
The transparent cover of the strainer is fragile. To
unscrew it, use a ring spanner or open-end spanner
that fits accurately.
Carefully unscrew the transparent cover of the strainer at the
bottom of the pressure reducing valve.
6.
Remove the strainer and clean it with clean water and a soft
brush.
a. If the strainer is damaged, replace it.
7.
Insert the clean or new strainer into the pressure reducing
valve.
8.
Carefully screw in the transparent cover of the strainer at the
bottom of the pressure reducing valve.
a. Make sure the O-ring is positioned correctly.
9.
Open the shut-off valve.
10. Make sure the pressure reducing valve does not leak.
11. Switch on the main switch.
12. Put the system back into the operating state that was set
before you started your work.
9.5 Checking and cleaning the dissolving hopper
1.
Switch off the main switch on the control cabinet.
a. Make sure the main switch cannot be switched on
accidentally.
2.
Close the shut-off valve upstream the pressure reducing valve.
3.
Put on the stipulated personal protective equipment. Observe
the chemical manufacturer's safety data sheets (SDS) and
safety instructions of the used chemicals.
4.
Visually inspect the dissolving hopper.
a. Check that the hopper is completely flushed with water and
that no deposits of dry material have formed.
In case of slight deposits:
5.
Unscrew the safety guard at the top of the dissolving hopper.
6.
Clean the dissolving hopper with clean warm water and a soft
brush.
7.
Install the safety guard again.
In case of medium or heavy deposits:
8.
Manually loosen the union nut at the water connection of the
dissolving hopper and disconnect the water supply.
a. Keep the O-ring.
9.
Remove the screws that connect the dissolving hopper to the
tank.
10. Remove the dissolving hopper from the tank.
a. Keep the O-ring.
11. Unscrew the safety guard at the top of the dissolving hopper.
12. Clean the dissolving hopper with clean warm water and a soft
brush.
13. Install the safety guard at the top of the dissolving hopper.
14. Install the dissolving hopper on the tank.
a. Make sure the O-ring is positioned correctly.
15. Connect the water connection of the dissolving hopper.
a. Make sure the O-ring is positioned correctly.
16. Open the shut-off valve.
44
English (GB)
Содержание Polydos 412E
Страница 2: ......
Страница 3: ...Polydos 412E English GB Installation and operating instructions 4 3 Table of contents...