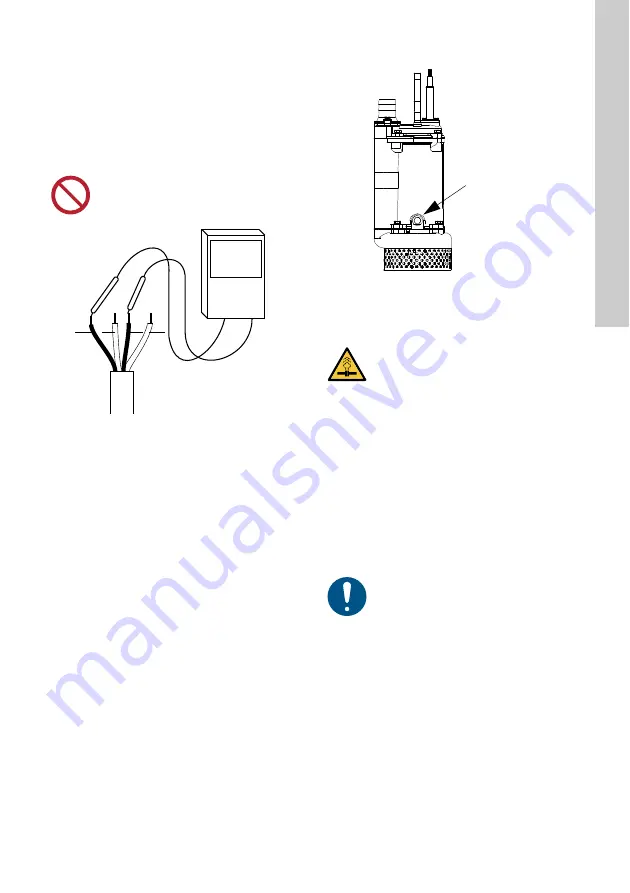
English (GB)
15
8.4.3 Checking the outlet pressure and flow rate
Declining performance can indicate the need for an
overhaul. Regardless of performance, the pressure
and flow rate must be stable, and rapidly changing
pressure or flow rate indicate system problems on
the inlet or outlet side.
8.4.4 Inspecting the seal sensor
Check the resistance of the seal sensor with a
multimeter as shown in fig.
Fig. 15
Resistance check
8.4.5 Oil check and oil change
Fig. 16
Position of oil plug
1. Loosen the oil plug. See fig.
2. Remove the oil plug and check the oil level.
3. Take a sample to inspect the condition of the oil.
4. If the oil needs to be changed, place a clean
container under the pump to collect all the
drained-off oil.
5. Tilt the pump with the oil-filling hole pointing
downwards in order to drain the pump of oil.
If the drained oil is contaminated or opaque, this
is an indication of an impending mechanical shaft
seal failure. Replace the mechanical seal.
6. Fill fresh oil into the oil chamber through the oil
filling hole. Use lubrication oil ISO VG 32 Mobil
DTE 24 turbine oil 90 or equivalent.
8.4.6 Inspection and adjustment of impeller
clearance
Check the clearance between the impeller and the
wear plate. Recommended clearance is 0.3 - 0.5
mm. Replace or repair as necessary.
Do not use a megger as it will damage the
control circuit of the seal sensor.
TM
04
41
19
08
0
9
20 K
Ω
TP
TP
SS
SS
TM
04
41
44
090
9
CAUTION
Pressurised system
Minor or moderate personal injury
- When loosening the oil plug of the oil
chamber, note that pressure may have
built up in the chamber. Do not remove
the oil plug until the pressure has been
fully relieved.
Used oil must be disposed of in
accordance with local regulations.
Oil plug