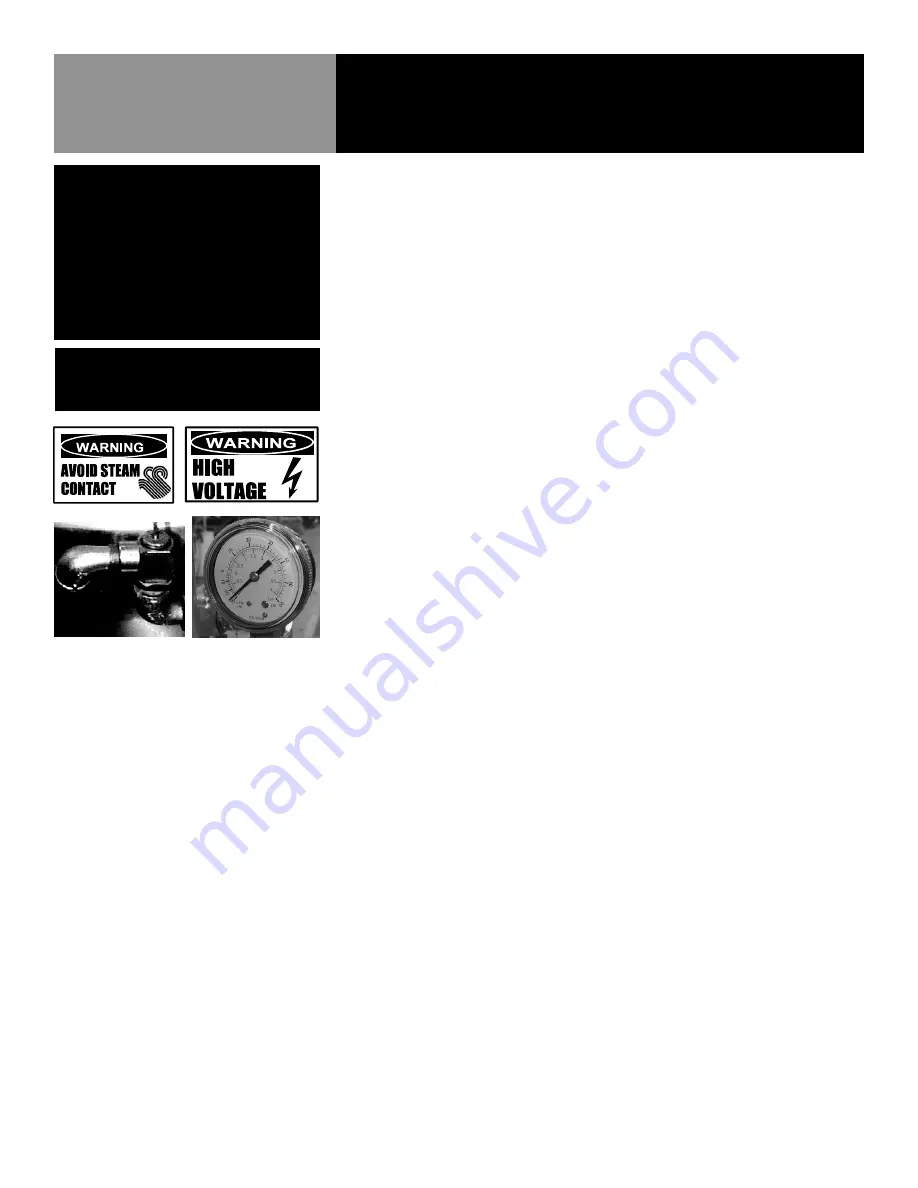
14 OM-TDB/6
Maintenance
NOTICE: Contact an authorized representative when repairs are required.
A Maintenance & Service Log is provided at the back of this manual. Each time
maintenance is performed on your kettle, enter the date on which the work was done,
what was done, and who did it. Keep this manual on file and available for operators to
use. Periodic inspection will minimize equipment down time and increase the efficiency
of operation. The following points should be checked:
1.
Jacket Vacuum/Removing Air from Jacket (by Operator)
Every day, while the kettle is cold, read the pressure/ vacuum gauge. A
positive reading or a negative reading between zero and 20” vacuum on the
pressure/ vacuum gauge indicates excess air in the jacket. Air in the jacket
slows kettle heating and can prevent the kettle from reaching operating
temperature. To remove air:
To remove air:
a.
Start the unit. (See “Operation” section).
b.
Make sure the elbow on the outlet of the pressure relief valve is turned
so that escaping steam is directed down toward the floor. Be sure and
follow the instructions on the attached pressure relief valve tag.
c.
When the pressure/vacuum gauge reaches a positive pressure reading
of 5 PSI (0.35 Bar/ 34.5 kPa), release trapped air by lifting the pressure
relief valve ring for about one second. Repeat this step, then let the
valve ring snap closed, so the valve will seat properly and not leak.
2.
Pressure Relief Valve (by Operator)
At least twice a month, test the pressure relief valve. Test the valve with the
kettle operating at 15 PSI (1.1 Bar/105 kPa), by holding the test ring for at least
five seconds. Then release the ring and permit the valve to snap shut. If the ring
does not activate, if there is no discharge, or if the valve leaks, stop using the
kettle immediately and contact a authorized service representative.
3.
Grease / Lubrication (by Service)
At least twice a year, grease the two trunnion bearings. The bearings are
located within the kettle support housing. Remove the access panels from the
support housing with a screwdriver to gain access to the grease fittings. Use
a lithium-based, multi-purpose grease. When the access panels are removed,
the mounting bolts for the trunnion bearings and tilt switch can also be
checked for tightness. When finished, reassemble access panels to support
housing.
4.
Jacket Filling
Every day, before you turn on the unit, make sure the water level is
approximately in the center of the water gauge glass. The jacket was filled at
the factory with the proper amount of treated water, and is airtight, but over
time steam may be vented and water lost.
From time to time, you may need to restore the water to its proper level. The
procedure for adding water follows.
WARNING
AVOID ANY EXPOSURE TO THE STEAM
BLOWING OUT OF THE PRESSURE
RELIEF VALVE. SEVERE BURNS CAN
RESULT ON EXPOSED SKIN.
FAILURE TO CHECK PRESSURE RELIEF
VALVE OPERATION PERIODICALLY
COULD RESULT IN PERSONAL INJURY
AND/OR DAMAGE TO EQUIPMENT.
Make sure that the
open end of the elbow
on the pressure
relief valve is directed
downward.
The pressure gauge
should show a
vacuum of 20 to 30
inches when the
kettle is cold.
CAUTION
KEEP GREASE AWAY FROM ELECTRICAL
PARTS LOCATED NEAR THE GEARS.