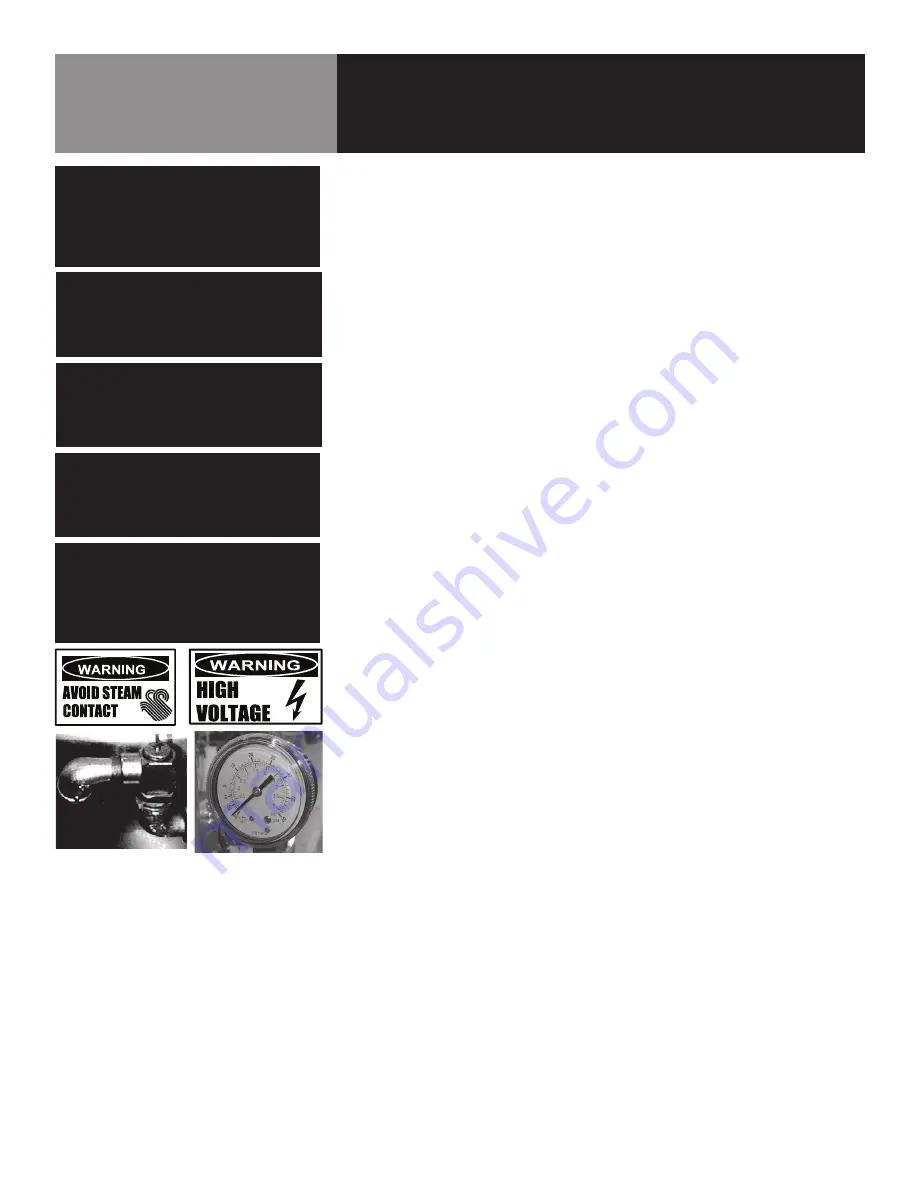
16 OM-DEE/4
Maintenance
NOTICE: Contact an authorized representative when repairs are required.
A Maintenance & Service Log is provided at the back of this manual. Each time
maintenance is performed on your kettle, enter the date on which the work was done,
what was done, and who did it. Keep this manual on file and available for operators to
use. Periodic inspection will minimize equipment down time and increase the efficiency of
operation. The following points should be checked:
1.
Check the pressure/vacuum gauge everyday. The gauge should show a vacuum of
20 to 30 inches mercury (Hg), when the kettle is cold. If it does not, see “Jacket
Vacuum” below.
2.
Also check the jacket water level every day. It should be between the markers on
the gauge glass. If the level is low, see “Jacket Filling and Water Treatment” below.
3.
Test the safety valve at least twice each month. Test the valve with the kettle
operating at 15 psi (105 kPa), by holding the test lever for at least 5 seconds. Then
release the lever and let the valve snap shut. If the lever does not activate, or there
is no evidence of discharge, or the valve leaks, stop using the kettle and contact a
qualified service representative.
4.
Keep electrical wiring and connections in good condition.
5.
Keep the inside of the control console clean and dry.
6.
Jacket Vacuum/Removing Air from Jacket
When the kettle is cold, a positive pressure reading on the pressure/vacuum gauge
or a reading near zero indicates that there is air in the jacket. Air in the jacket acts
as an insulator, and slows kettle heating.
To remove air:
a.
Start the unit. (Be sure there is water or product in the kettle when heating).
b.
When the pressure/vacuum gauge reaches a positive pressure reading of 5
PSI, release the trapped air and steam by pulling up or out on the safety
valve lever or ring for about 1 second. Repeat this step, then let the pull ring
or valve lever snap back into the closed position.
7.
Jacket Filling and Water Treatment
The jacket was charged at the factory with the proper amount of treated water. You
may need to restore this water, either because it was lost as venting steam or by
draining.
a.
If you are replacing water lost as steam, use distilled water. If you are
replacing treated water that ran out of the jacket, prepare more treated
water as directed in “Water Treatment Procedure.”
b.
Allow the kettle to cool. Turn the elbow on the safety valve counterclockwise
(to avoid thread damage) until the opening of the elbow faces upward.
c.
Open the safety valve and pour the water or treated water in at the elbow
until the water level rises to a point between the marks on the gauge glass.
WARNING
WHEN TESTING, AVOID ANY EXPOSURE TO
THE STEAM BLOWING OUT OF THE SAFETY
VALVE. DIRECT CONTACT COULD RESULT IN
SEVERE BURNS.
WARNING
DISCONNECT ELECTRICAL POWER FROM
THE UNIT BEFORE ATTEMPTING TO
GREASE THE TRUNNION BEARINGS.
WARNING
TO AVOID INJURY, READ AND FOLLOW ALL
PRECAUTIONS STATED ON THE LABEL OF
THE WATER TREATMENT COMPOUND.
WARNING
ELECTRIC POWER ALWAYS SHOULD BE
SHUT OFF BEFORE WORK IS DONE ON
INTERNAL COMPONENTS.
CAUTION
BEFORE YOU HEAT THE KETTLE AGAIN
FOR ANY PURPOSE, TURN THE ELBOW
BACK CLOCKWISE UNTIL THE OPENING
FACES DOWNWARD.
Make sure that the
open end of the elbow
on the pressure
relief valve is directed
downward.
The pressure gauge
should show a
vacuum of 20 to 30
inches when the
kettle is cold.
Содержание DEE/4-20A
Страница 19: ...OM DEE 4 19 Parts List For Classic Advanced Control Models...
Страница 20: ...20 OM DEE 4 Parts List For Classic Advanced Control Models...
Страница 22: ...22 OM DEE 4 Wiring Diagram For Classic Control Models...
Страница 23: ...OM DEE 4 23 Wiring Diagram For Advanced Control Models...
Страница 25: ......
Страница 26: ......
Страница 27: ......