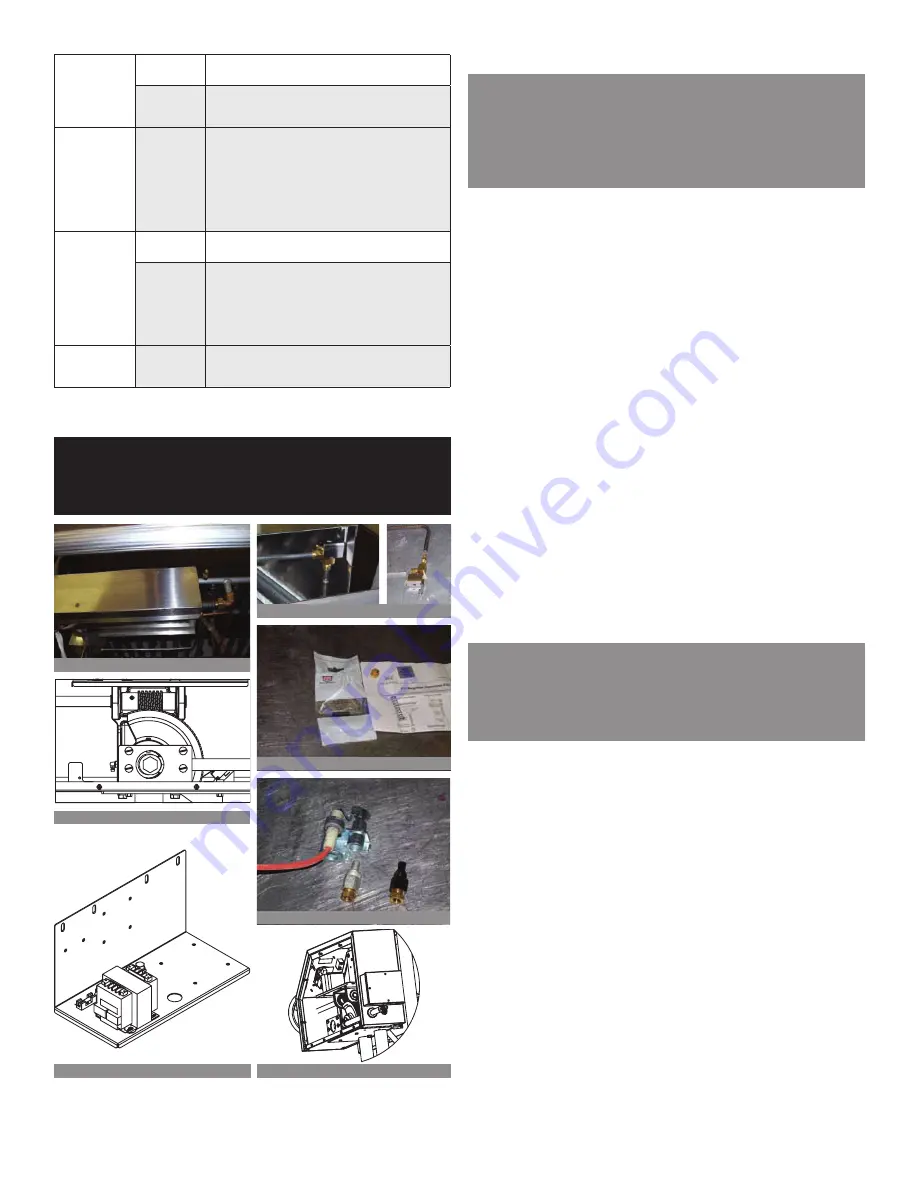
9
OM-BPM-15/30/40G(C,A) (CE) INTERNATIONAL
Pilot will not light.
User
a. Lighting procedure, to ensure that the instructions in the
Operation section of this manual are followed.
Authorized
Service Rep
Only
b. That the pilot gas supply line is purged of air. X
c. Pilot gas adjustment screw, to ensure that it is open. X
d. Pilot tubing and orifice for clogging. X
Pilot flame goes
out when
Combination
Control knob is
released.
Authorized
Service Rep
Only
a. Pilot gas adjustment. X
b. Are connections from Powerpile generator to Pilotstat
power unit and Powerpile operator clean and secure? X
c. Are open and closed circuit output voltages of the
generator in the acceptable range shown by the charts
in the manual for the W720 Systems Tester? X
d. Resistance of the Pilotstat power unit. X
e. If an appropriate meter is not available, replace the
generator first, then the power unit. X
Pan will not heat,
and pilot light
is out.
User
a. Is the Combination Gas Control Valve knob turned ON?
b. Check the pilot tubing and orifice for clogging.
Authorized
Service Rep
Only
c. Are connections from Powerpile generator to Pilotstat
power unit and Powerpile operator clean and secure?X
d. Are Open and closed circuit output voltages of the
generator in the acceptable range shown by the charts
in the manual for the W720 Systems Tester?X
e. If an appropriate meter is not available, replace the
generator. X
Pan will not heat,
but pilot
light is burning.
Authorized
Service Rep
Only
a. That secondary thermostat switch is closed.
SERVICING & CONVERSION
IMPORTANT: BEFORE ATTEMPTING ANY SERVICING, ENSURE THAT THE GAS ISOLATING
COCK IS TURNED OFF AND CANNOT BE INADVERTENTLY TURNED ON.
ENSURE ALSO THAT THE ELECTRICITY SUPPLY IS DISCONNECTED. AFTER
ANY SERVICING OR EXCHANGE OF GAS CARRYING COMPONENTS — ALWAYS
CHECK FOR GAS SOUNDNESS!
FIGURE 1
FIGURE 2
FIGURE 3
FIGURE 7
FIGURE 6
FIGURE 5
FIGURE 4
SERVICING
NOTES:
1. WHEN REPLACING WIRING CONNECTIONS REFER TO THE WIRING DIAGRAM
IN THE UNIT OR THIS MANUAL.
2. WHEN ANY THREADED GAS CONNECTION IS DISTURBED FOR ANY
REASON, THE THREADS MUST BE RESEALED WITH APPROPRIATE GAS LEAK
PREVENTION SEALANT THAT IS SUITABLE FOR THE TYPE OF GAS. UNIFIED
BRANDS/ GROEN RECOMMENDS GAS SEALANT COMPOUND SUCH AS
LOCKTITE® 243 OR UNIFIED BRANDS PART NUMBER 122002.
After Servicing
1. Test for gas soundness as specified in IGE/UP1.
2. If leaks are found, disconnect the mating parts, clean the threads and apply
recommended sealant as specified above in Note #2. as appropriate after
any gas connection has been disturbed.
3. Check for correct operation as appropriate (see Installation, CE Models, Gas
System Performance).
Regular Servicing Procedures
The following must be checked at regular intervals:
1. Burners Clean the burners periodically to maintain maximum performance.
Burners are best cleaned with a stiff bristle brush, or if necessary with a wire
brush. Take care not to damage the burner.
Clean the injector orifice with a wooden splinter or toothpick. Avoid metal
reamers, which may distort or increase the orifice size. WARNING - Do not
leave any wood splinter or bristles from brush in the burner or injector. Fire
could result.
2. Gears and Bearings: The gear housing has been fitted for proper lubrication
of moving parts. Since the gears do not run in oil, periodic lubrication with
grease is essential. Frequency of lubrication depends on operating conditions,
but should occur at least once every six months. Groen recommends the use
of a Number Two grade LGI lithium grease. Add grease through the Zerk
fittings on the gear housing until grease flows out of the bearings around the
trunnion shaft. Place a liberal amount of grease on the gear to cover the arc
that is in contact with the worm gear.
CONVERSION
NOTES:
1. SEE INSTALLATION, CE MODELS, GAS SYSTEM PERFORMANCE FOR
IMPORTANT INFORMATION. VERIFY THE TYPE OF GAS TO BE USED. IN THE
COUNTRIES LISTED IN THAT SECTION, ALL CONVERSIONS MUST BE FOR
APPROVED GAS.
2. ALL THREADED GAS CONNECTIONS MUST BE SEALED AS SPECIFIED IN
NOTE #2 IN SERVICING SECTION.
To change the type of gas used (e.g G20 to G31 natural to propane or inverse)
following parts should be changed:
1. Burner injectors. See instruction in REMOVAL OF BURNER ORIFICES at the
end of this section.
2. Igniter tube injector. This is inserted inside the igniter tube as shown in the
figures.
3. Gas valve spring. Install per instructions supplied with the spring package as
shown in figure 5.
4. Pilot orifice. Insert the black shaded orifice for G31 or propane gas as shown
in figure 6. The light colored orifice is for G20 on natural gas.
5. Data plate with correct rate and gas manifold pressure information.
After Conversion
1. Test for gas soundness as specified in IGE/UP1as appropriate after any gas
connection has been disturbed.
2. If leaks are found, disconnect the mating parts, clean the threads and apply
recommended sealant as specified in SERVICING, Note #2, at the beginning
of this section.
REMOVAL OF CONTROL CABINET PANELS
1. Remove 10 screws on cover.
2. Remove 4 screws at center of cover.
3. Lift off the removable side panel.