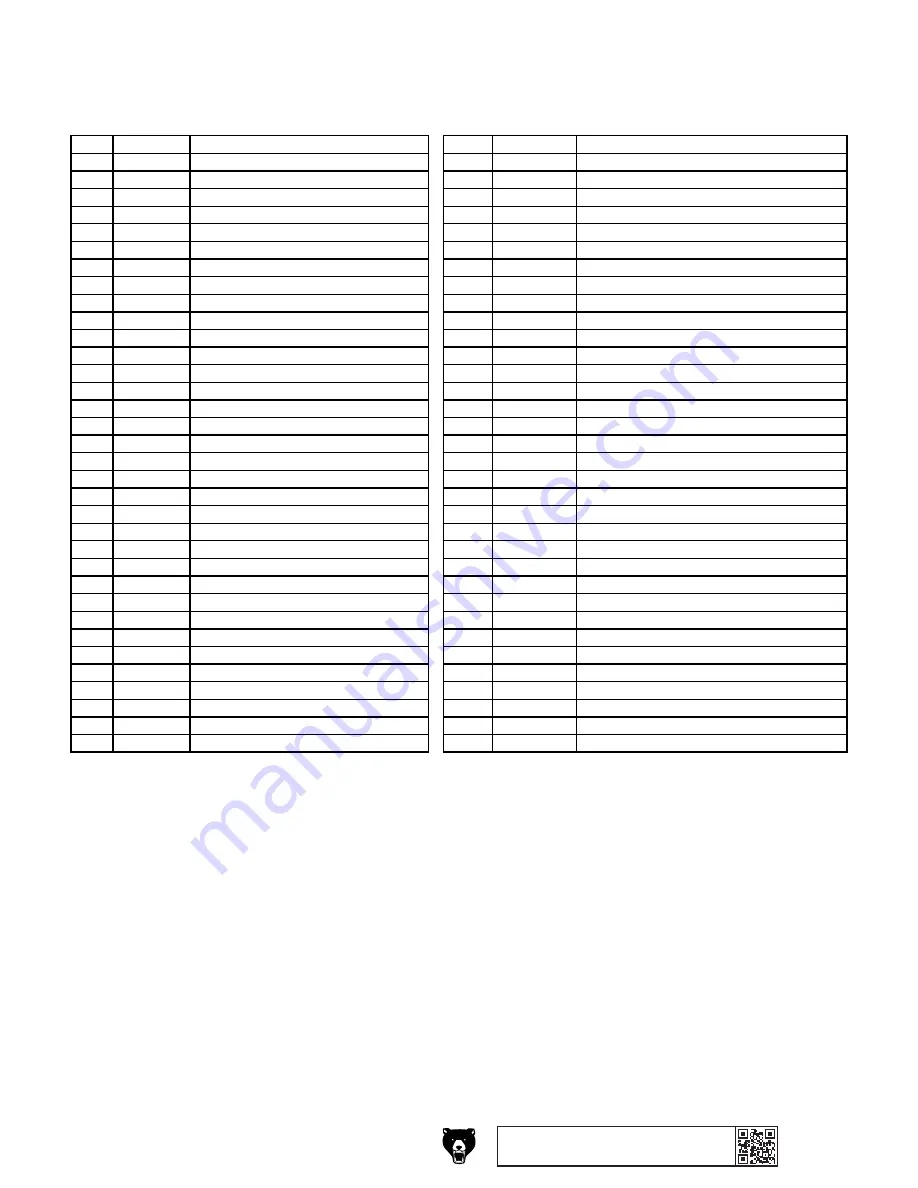
Model G0857/G0858 (Mfd. Since 07/19)
-59-
BUY PARTS ONLINE AT GRIZZLY.COM!
Scan QR code to visit our Parts Store.
Parts List (Cont.)
REF PART #
DESCRIPTION
REF
PART #
DESCRIPTION
110
P0857110
CAP SCREW 3/8-24 X 2
137-9
P0857137-9
BACKING BOARD
111
P0857111
LOCK WASHER 3/8
137-10 P0857137-10 MOTOR FAN COVER
112
P0857112
HEX BOLT M8-1.25 X 25
137-11 P0857137-11 MOTOR FAN
113
P0857113
INFEED TABLE LOCK PLATE
137-12 P0857137-12 CONTACT PLATE
114
P0857114
SCALE POINTER
137-13 P0857137-13 CENTRIFUGAL SWITCH
115
P0857115
BUTTON HD CAP SCREW M5-.8 X 6
137-14 P0857137-14 S CAPACITOR 400M 125V 1-1/2 X 3-1/2
116
P0857116
FLAT WASHER 10MM
137-15 P0857137-15 R CAPACITOR 70M 250V 1-1/2 X 3-1/2
117
P0857117
WAVY WASHER 10MM
137-16 P0857137-16 CAPACITOR COVER
118
P0857118
ADJ HANDLE 93L, M10-1.5 X 25
137-17 P0857137-17 BALL BEARING 6205-ZZ (FRONT)
119
P0857119
PHLP HD SCR M6-1 X 12
137-18 P0857137-18 BALL BEARING 6203-ZZ (REAR)
120
P0857120
FLAT WASHER 6MM
138
P0857138
KNIFE-SETTING JIG (G0857)
121
P0857121
DUST PORT 4"
138
P0858138
TORX DRIVER T-25 (G0858)
122
P0857122
CABINET STAND
139V2 P0857139V2 GUARD PIVOT SHAFT V2.07.19
123
P0857123
WHEEL
140
P0857140
EXT RETAINING RING 11MM
124
P0857124
LOCK NUT M8-1.25
141V2 P0857141V2 TORSION SPRING V2.07.19
125
P0857125
WHEEL AXLE M8-1.25 X 30, 60L
142
P0857142
ROLL PIN 6 X 28
126
P0857126
KNOB BOLT 3-LOBE, M10-1.5 X 22, D40
143V2 P0857143V2 ROLL PIN 5 X 26
127
P0857127
PHLP HD SCR M6-1 X 10 W/WASHER
144
P0857144
SWITCH BOX
128
P0857128
BELT COVER
145
P0857145
SWITCH PLATE
129
P0857129
REAR ACCESS PANEL
146
P0857146
SWITCH CORD 14G 3W 20"
130
P0857130
PHLP HD SCR M6-1 X 20
147
P0857147
POWER CORD 14G 3W 10' 6-20P
131
P0857131
PUSH BLOCK BRACKET
148
P0857148
STRAIN RELIEF TYPE-1 5/8"
132
P0857132
PHLP HD SCR M4-.7 X 8
149
P0857149
PHLP HD SCR M4-.7 X 25
133
P0857133
CAP SCREW M8-1.25 X 20
150
P0857150
PHLP HD SCR M4-.7 X 6
134
P0857134
CARRIAGE BOLT 5/16-18 X 3/4
151
P0857151
EXT TOOTH WASHER 4MM
135
P0857135
FLAT WASHER 8MM
152
P0857152
GROUND LABEL
136
P0857136
POLY V-BELT 300J-7 30"
154
P0857154
FOAM PAD 30 X 30 X 22
137
P0857137
MOTOR 3HP 230V 1-PH
155
P0857155
TAP SCREW M6 X 8
137-2 P0857137-2 KEY 5 X 5 X 30
156
P0857156
ADJUSTABLE FOOT M8-1.25
137-3 P0857137-3 MOTOR PULLEY
160
P0857160
HEX WRENCH 6MM
137-4 P0857137-4 SET SCREW M6-1 X 8
161
P0857161
WRENCH 8 X 10MM OPEN-ENDS
137-5 P0857137-5 MOTOR LABEL
162
P0857162
WRENCH 11 X 13MM OPEN-ENDS
137-6 P0857137-6 STRAIN RELIEF TYPE-3 PG13.5
163
P0857163
LIFTING HOOK
137-7 P0857137-7 MOTOR CORD 14G 3W 32"
164
P0857164
BUTTON HD CAP SCR M6-1 X 12
137-8 P0857137-8 STRAIN RELIEF TYPE-1 3/4"
165
P0857165
CUTTERHEAD GUARD WASHER 6.7 X 19 X 2
Содержание G0857
Страница 65: ......