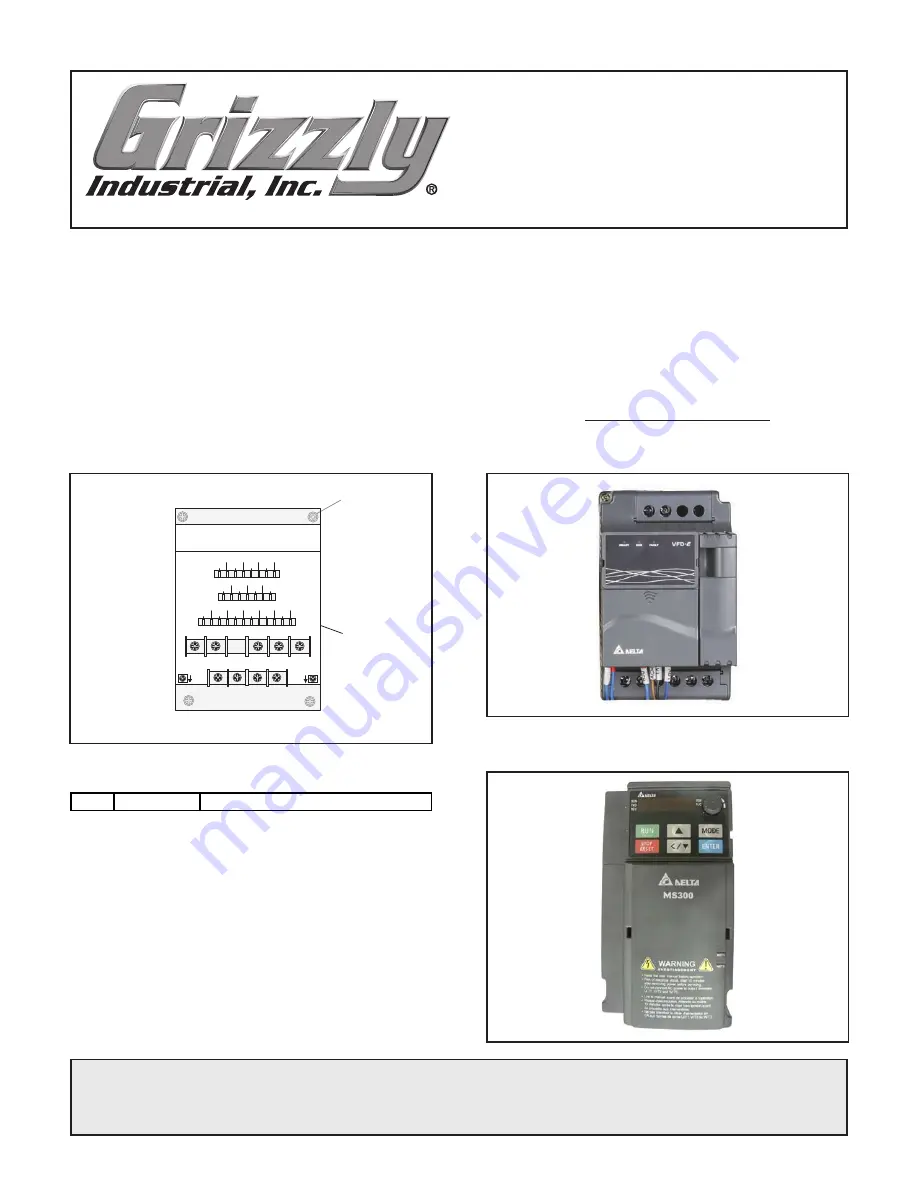
COPYRIGHT © JULY, 2019 BY GRIZZLY INDUSTRIAL, INC.
WARNING: NO PORTION OF THIS MANUAL MAY BE REPRODUCED IN ANY SHAPE
OR FORM WITHOUT THE WRITTEN APPROVAL OF GRIZZLY INDUSTRIAL, INC.
#AI20557 PRINTED IN CHINA
The following change was recently made since the owner's manual was printed:
•
Delta VFD-E replaced by Delta MS300.
Aside from this information, all other content in the owner's manual applies and MUST be read and under-
stood for your own safety.
IMPORTANT: Keep this update with the owner's manual for future reference.
For questions or help, contact our Tech Support at (570) 546-9663 or [email protected].
READ THIS FIRST
For questions or help with this product contact Tech Support at (570) 546-9663 or [email protected]
Model G0757Z
***IMPORTANT UPDATE***
For Machines Mfd. Since 07/19
and Owner's Manual Printed 07/15
Revised Parts Breakdown
New Delta Variable Frequency Drive
Old Delta Variable Frequency Drive
REF PART #
DESCRIPTION
515V2 P0757Z515V2 VFD DELTA MS300 V2.07.19
Variable Frequency Drive
DELTA MS300
GND
GND
W/T3
R/L1
DC
+2/B1
B2
DC
+/+1
S/L2
T/L3
U/T1
V/T2
+24V
S1
S2
DCM
SG+
SG-
SGND
MCM
+10
ACM
AVI
ACI
AFM
M01
M02
MI1
MI2
MI3
MI4
MI5
MI6
MI7
+24V
+24V
DCM
DCM
DFM
515V2
523
Содержание G0757Z
Страница 90: ......