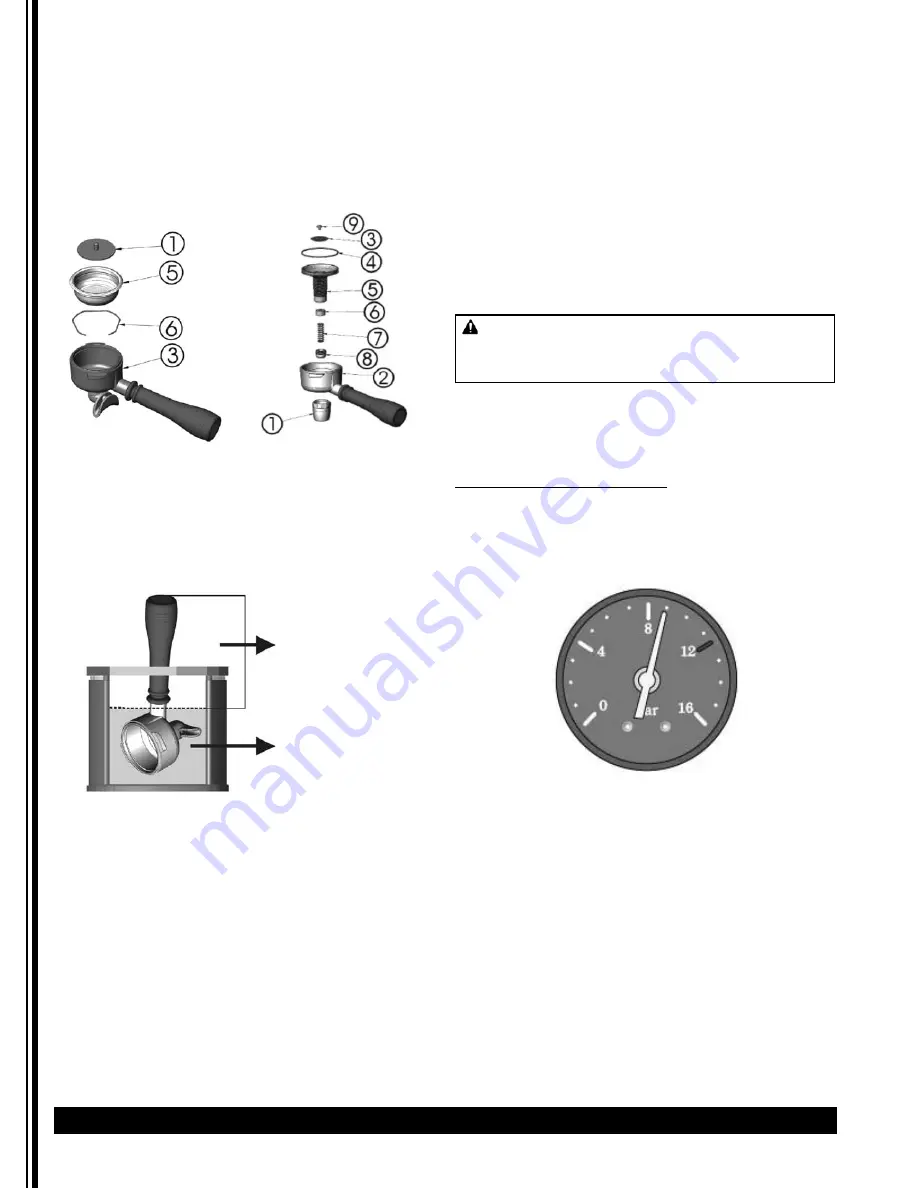
10
Grindmaster
®
ET1 Espresso Machine
Cleaning and sanitizing portafilter:
Notice:
To avoid damage, do not immerse espresso
Porta Filter handle in water. Do not put group gasket
(item B from
Figure I
) in water or any liquid detergent.
1. Disassemble Portafilter. (see
Figure K
)
2. Remove sprayer from hot water wand.
3. Remove nipple from steam arm.
4. Add loose group head parts [screw (E), shower
screen (D), and plate(C) from
Figure I
].
5. Use brush to clean and wash parts in detergent or
espresso urn cleaner/sanitizer. DO NOT immerse
Portafilter handle. (see
Figure L
)
6. Rinse parts.
7. Prepare a sanitizing solution in accordance with
local health department regulations. You may also
refer to the US Food and Drug Administration
regulation 21 CFR 178.1010 “Sanitizing Solutions”
and US Environmental Protection Agency 40 CFR
18.940 “Tolerance exemptions for active and inert
ingredients for use in antimicrobial formulations
(Food-contact surface sanitizing solutions)”.
8. Follow the instructions provided with the sanitizing
agent.
9. Let all sanitized parts drain and dry naturally. DO
NOT WIPE THEM DRY.
10. Reassemble parts.
Drain Tray and Discharge Trough:
1. Remove and wash the drain tray after stopping use.
2. Wipe and remove sediments in the discharge
trough with a wet cloth and wash with hot water
to clear the discharge tube.
3. If water does not discharge properly, place a
teaspoon of detergent into the discharge trough
and flush with hot water to dissolve residual oils in
the tube.
4. Reassemble after the water tray has dried.
Adjustments
The rest of this manual contains information to aid the
service technician who is maintaining this equipment.
This section has information on performing common
service tasks.
Water Pressure Adjustment
The water pressure has been factory adjusted to 9 bar
(the recommended pressure). After machine starts up
and water refills, press continuous flow button and read
pressure on pressure gauge to determine if the
indicator is in blue zone (8-10 bar) as shown in
Figure
M
.
If the pressure is not in the blue zone, adjust pressure
as shown below:
1. Remove left side panel (see
Figure N
, next page).
2. Attach Portafilter into the brewing group with
filled ground coffee.
3. Press continuous flow button. Turn screw clockwise
as shown in
Figure O
on next page to increase
pressure; turn counterclockwise to reduce pressure.
Handle
Do not immerse
Liquid
Figure L
Cleaning (continued)
Figure K
Water Pressure 9 bars
Figure M
WARNING: SHOCK / BURN HAZARD
Only a qualified service technician should perform
electrical and mechanical adjustments or repairs.