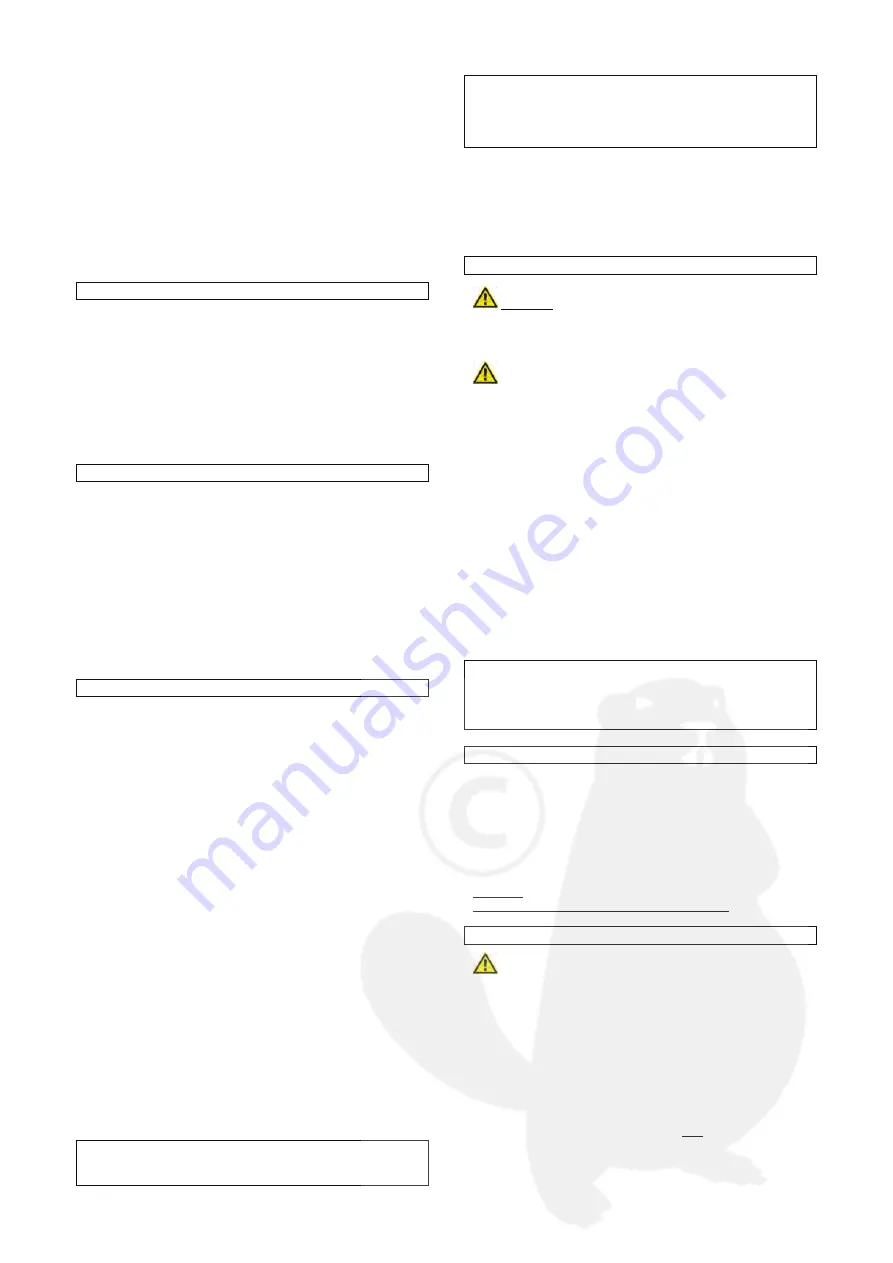
Assembly of wheels – pic. 4
Put the wheel axis with the foot lever (A) through both holes on
the oil tank. Put the M6 socket-head screw (B) through the
wheel axis and screw it with the check nut on the plate (C).
Then install the turning wheel on both sides and secure it with
a safety pin (D) on both sides. Slightly bend the safety pin to
prevent falling out.
Table assembly - pic. 1
Depending on the split wood length, the table board can be
fixed in three heights - 570 mm, 770 mm and 1,060 mm.
Table locking levers (pic. 1/7) are fixed in every assembly
position. Insert the table board to the required holders (pic.
1/12). Now secure the table board by the locking lever on
both sides.
Lift adjusting (pic. 5)
The working output can be increased for wood pieces smaller
than app. 50 cm and for more wood pieces by shortening the
backward movement of the splitting knife.
Proceed as follows:
Put a short piece of wood on the splitter table and move the
splitting knife as low as app. 2 cm above the wood. Switch the
splitter off (red button on the switch and disconnect the plug).
Now you can shorten the backward movement using the fixed
rod (pic. 5/B) by fixing the rod in the required height with the
adjusting screw (pic. 5/A).
Area of application
The appliance can only be used for wood processing. The split
material must have the following dimensions:
-
Minimum diameter: 120 mm
Maximum diameter: 300 mm
-
Wood splitting along fibre is only allowed.
-
Risk of getting jammed at branchy wood when splitting.
-
Jammed piece of wood is released by tipping on the
wood.
-
Cutting the split wood out prohibited!
Split wood length adjusting
Wood of various lengths can be split depending on the splitter
type:
Electric/hydraulic connection (pic. 6 and 7)
Plugging
All splitters are fitted with undervoltage release in the switch in
accordance with provisions of branch professional
organisations “CE“, etc. The release prevents automatic
starting of the appliance in case supply is interrupted as a
result of power failure, unintentional unplugging, defective
fuse, etc. The appliance must unconditionally be switched on
again by pressing the green switching button.
Wilful holding or blocking of the switching button with no
directly earthed conductor automatically leads to switch failure.
In this case that can subsequently be identified the guarantee
expires.
The appliance meets EN 61000-3-11 requirements and is
subject to special connection conditions. That means that
use on optionally selected connection points is
inadmissible.
The appliance can lead to occasional voltage fluctuations
under unfavourable power conditions.
The appliance is only designated to be used for connection
points not exceeding the maximum allowed impedance of
Z
max
= 0,233
.
As a user, you must make sure your connection point on
which you want to use the appliance meets the above-
mentioned requirements – after agreement with your
electricity supplier if necessary.
Hydraulic equipment
Tightness needs to be checked at hydraulic hoses and
couplings after app. 4 running hours and tighting must be
provided if necessary.
Only at 400 V appliances: It is necessary to be particular
about the running direction of the engine (see the arrow
on the engine) as running in wrong running direction can
damage the oil pump. In such a case, all claims arising
from the guarantee expire. If necessary, have the running
direction changed by reversal of polarity of the plug by a
professional electrician. See pic. 6! (three-phase current
models only!)
Hydraulic oil/tank
Common hydraulic oil (e.g. HLP 46 or oil of different producer
of identical viscosity) can be filled in all splitters. Oil change is
not necessary.
Vent the tank before each operation by screwing the filling
screw out and in (pic. 7/A).
Operation
Attention: Make sure wood is cut at right angle, if
possible, and seated closely on the splitting table. Cross-
cut or extremely branchy wood can slide or bend the
service arms.
Always put wood on surfaces (tables) designated for
this purpose (never on the frame). That could damage the
splitter.
1. Start the engine by pressing the green switching button.
Attention: Be particular about the running direction of
the engine at 400 V models!
2. Keep the feeder cable as short as possible at 230
V models and select as big cross section as possible.
3. When the temperature is low, let the splitter run idle
for app. 15 minutes so that oil warms up to
corresponding temperature.
4. Put the split material on the table and hold it using
clamping plates on the lever.
5. Splitting starts by pressing both levers down (as soon as
the splitting knife enters wood tip the lever slightly out
while pressing it down. This will prevent holding sheets
(arms) from bending).
6. Lift at least one lever after you have finished splitting – the
splitter pillar will automatically go up.
It is strictly prohibited to operate the wood splitter in two
persons with one holding wood and the other one
pressing on the clamping plates. Blocking one lever
(clamping plate) is prohibited, too.
Transport instructions
Transport
All wood splitters are fitted with big wheels. Grasp the handle
on the splitting pillar with one hand and handle above the
engine with the other hand and slightly tilt the splitter to you for
transport purposes. The splitter can effortlessly be moved in
this position.
To prevent hydraulic oil leakage, never transport the splitter
laid down
.
Always let the splitting knife go absolutely down for transport.
Residual risks and protective measures
Warning!!!
Taking out of operation, any change, blocking,
disassembly, changeover or assembly of all parts on
safety and protective equipment of the appliance is strictly
prohibited and can have serious consequences, i.e. life
threatening injuries if not observed.
The producer cannot be held liable for material damages
or injuries caused as a result of such negligence.
All guarantee claims towards the producer immediately
expire at each of the above-mentioned negligence.
The splitter can only be operated by one person. Remove
wood remnants that could block or negatively influence
the safety and service elements near the splitter and
workplace during operation.
30