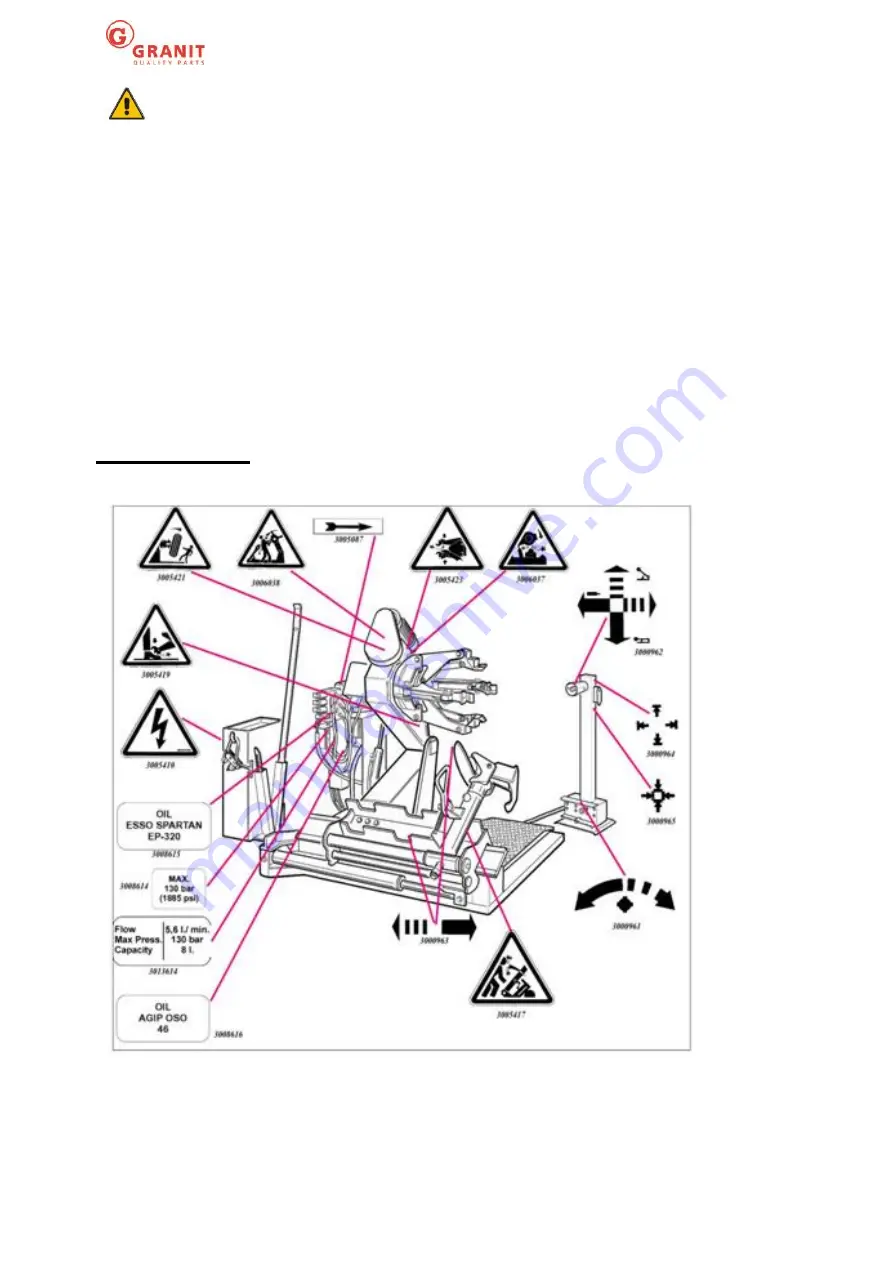
- 4 -
· Always use proper and appropriate equipment and tools.
· Wear suitable protective clothing and safety equipment (e.g. goggles, hearing protection, safety shoes,
etc.).
· Observe the specified information, instructions and technical data of the machine manufacturer or the
manufacturer of the product (tyres & rims) that is to be worked on.
Further special safety instructions are given in the individual chapters.
The Wilhelm Fricke SE does not assume any liability for damage caused by improper operation
and/or unpurposeful use of the tyre-changer.
Unauthorized interventions or changes to the machine are not permitted.
Danger Signs
Содержание 7790400001
Страница 30: ...30 Drawing 1 Complete view Spareparts list Version 1 1 Drawing 2 Chuck arm 30...
Страница 31: ...31 Drawing 3 Hydraulic unit Drawing 4 Pump unit...
Страница 32: ...32 Drawing 5 Control box Drawing 6 Base frame Sledge...
Страница 33: ...33 Drawing 7 Chuck Drawing 8 Tool arm...
Страница 34: ...34 Drawing 9 Mobile control unit Drawing 10 Accessories...