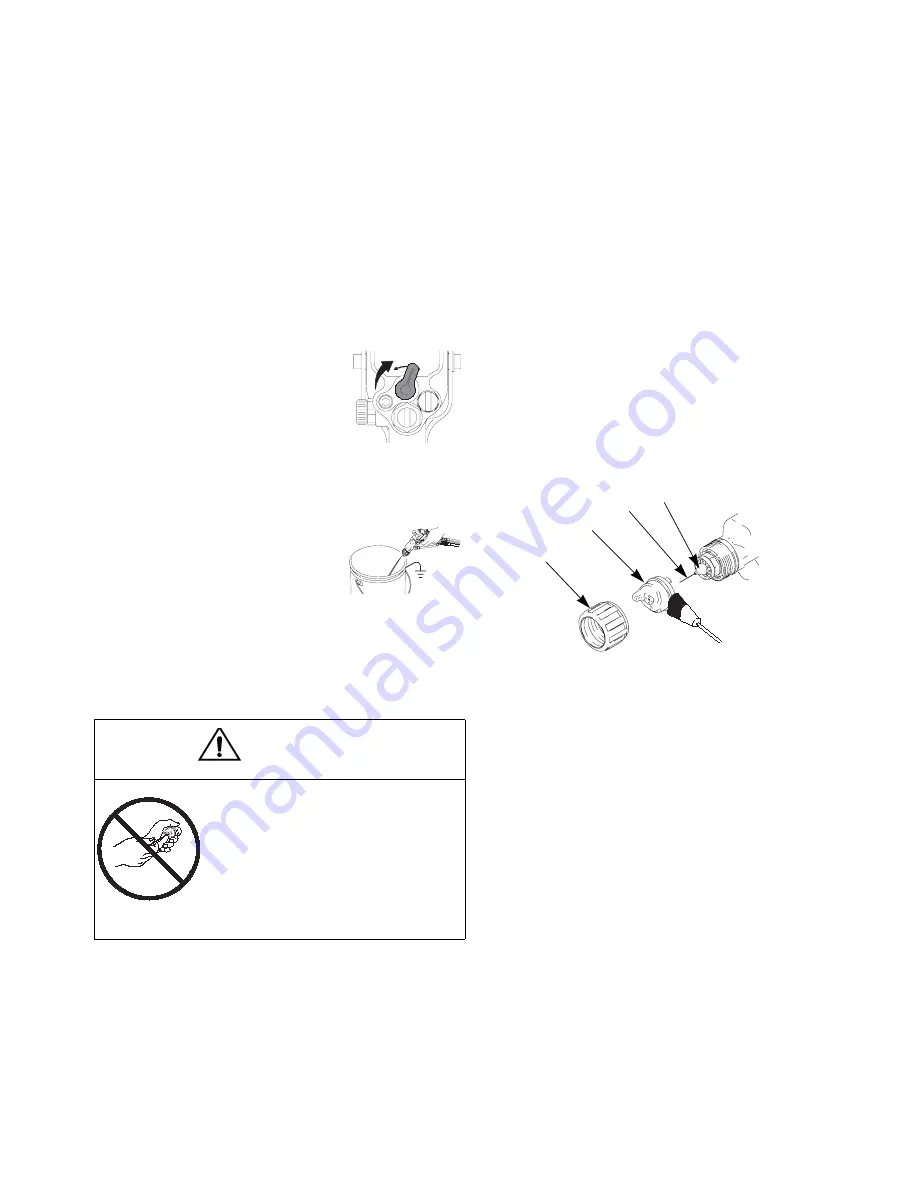
Maintenance
309293J
29
Clean the Air Cap and Fluid
Nozzle
Equipment Needed
•
soft bristle brush
•
non-flammable solvent
Procedure
1.
Turn the ES ON/OFF valve OFF. Wait 30 seconds.
2.
Discharge the system voltage (page 20).
3.
Relieve the pressure (page 20).
4.
Remove the retaining ring (27) and air cap (9). See
F
IG
. 16..
5.
Clean the air cap (9) with the soft bristle brush and
non-flammable solvent or submerge the air cap in
solvent and wipe it clean.
6.
With the gun pointing down, clean the fluid nozzle
(7) and the front of the gun with a soft brush damp-
ened with non-flammable solvent.
If it appears that there is paint inside the fluid nozzle (7)
air passages, remove the gun from the line for servicing.
7.
Carefully install the air cap (9). Be sure to insert the
electrode (29) through the center hole of the air cap.
Rotate the air cap to the desired position.
8.
Tighten the retaining ring (27) until the air cap is
held firmly in place; you should not be able to rotate
the air cap horns by hand.
9.
Test gun resistance, page 30.
Fig. 16. Clean Air Cap and Fluid Nozzle
Grease Door Latch Threads
Inspect the door T-handle locking screw regularly, to
ensure the threads are well greased. Apply silicone-free
grease to the threads when necessary.
CAUTION
Do not use metal tools to clean the
air cap or fluid nozzle holes as this
could scratch them, and make sure
the electrode is not damaged.
Scratches in the air cap or nozzle or
a damaged electrode can distort the
spray pattern.
I O
ES
ti1273a
ti1276a
ti1297a
9
27
29
7