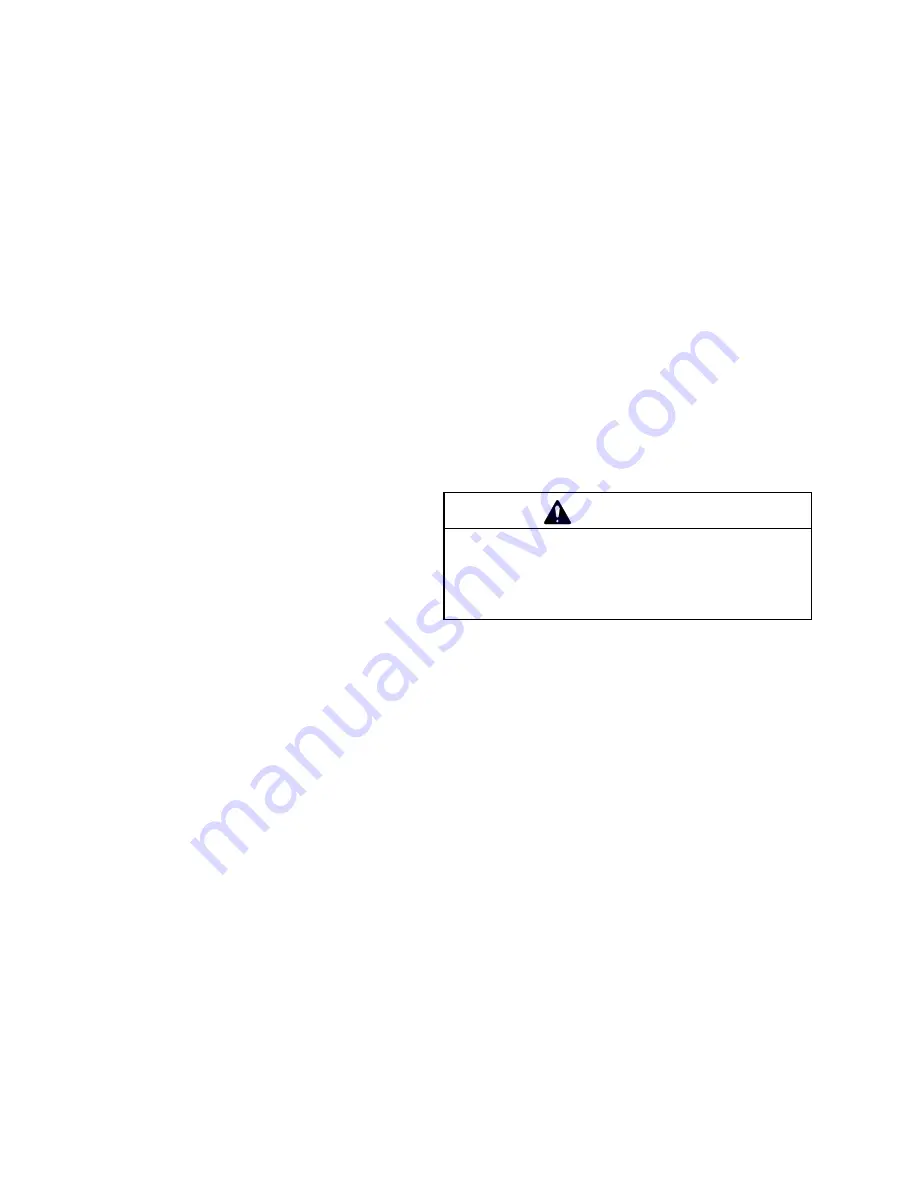
10 307-043
Air Motor Service
Reassembly
1.
Place the piston rod (A) flats in the vise with the air
motor up.
2.
Pull the exhaust valve poppets (M**) into the valve
actuator (V), and clip off the top parts of the pop-
pets (shown with dotted lines in the Cutaway
View in Fig. 3).
3.
Install the grommets (Y*) in the actuator (V), place
the inlet valve poppets (N*) in the piston, and
thread the bottom valve nuts (K*) onto the inlet
valve poppets until there are a few threads left
before the threads run out.
NOTE: If you thread the valve nuts too far down onto
the poppets, they will run off of the threaded part of the
poppets.
4.
Place the actuator (V) in the yoke (O) and insert
the trip rod (C) through them. Thread a 5/16–18
unc nut on the trip rod to prevent it from sliding into
the piston when assembling. Grease the trip
rod/actuator/yoke assembly heavily and place into
the piston with the inlet valve poppets (N*) going
through the grommets (Y*).
5.
Thread the top valve nuts (J*) onto the inlet valve
poppets (N*) until one thread of the inlet valve
poppets is exposed above the valve nuts.
6.
Install the toggle pins (Z) in the yoke (O). As-
semble the toggle assembly (U) by placing a well
greased spring onto the toggle arm (T) and then
the toggle rocker (S). Place the toggle arm (T)
ends of the toggle assembly (U) onto the toggle
pins, and snap the pivot pin (S) ends of the toggle
assembly into the lugs (P).
7.
Measuring with the gauge (171–818), create
0.145-in. (3.7 mm) of clearance between the inlet
valve poppets (N*) and the piston seat when the
inlet valve is open. See the Cutaway View Fig. 3.
NOTE: Adjust the distance between the inlet valve
poppets and the piston seat by turning the top valve
nuts (J*).
8.
Tighten the bottom valve nuts (K*) securely by
hand.
9.
Align the holes in the valve nuts (K*) and the slots
on the tops of the inlet valve poppets (N*), and
drop the lock wires (L**) through the holes in the
valve nuts and into the slots in the inlet valve
poppets. Pull the lock wires down tightly, and
bend the ends about 120
with needle-pliers so
that they cannot be pulled back out of the holes.
CAUTION
Never re-use the old lock wires. They will get brittle
and break easily from too much bending.
Do not score the lock wires when you bend them
because they will break on the scoring.
10. Grease and install the new o-rings on the piston
assembly (G) and in the groove in the air motor
base (F).
11. Clamp the air motor base (F) in a vise by closing
the vise jaws on the flange.