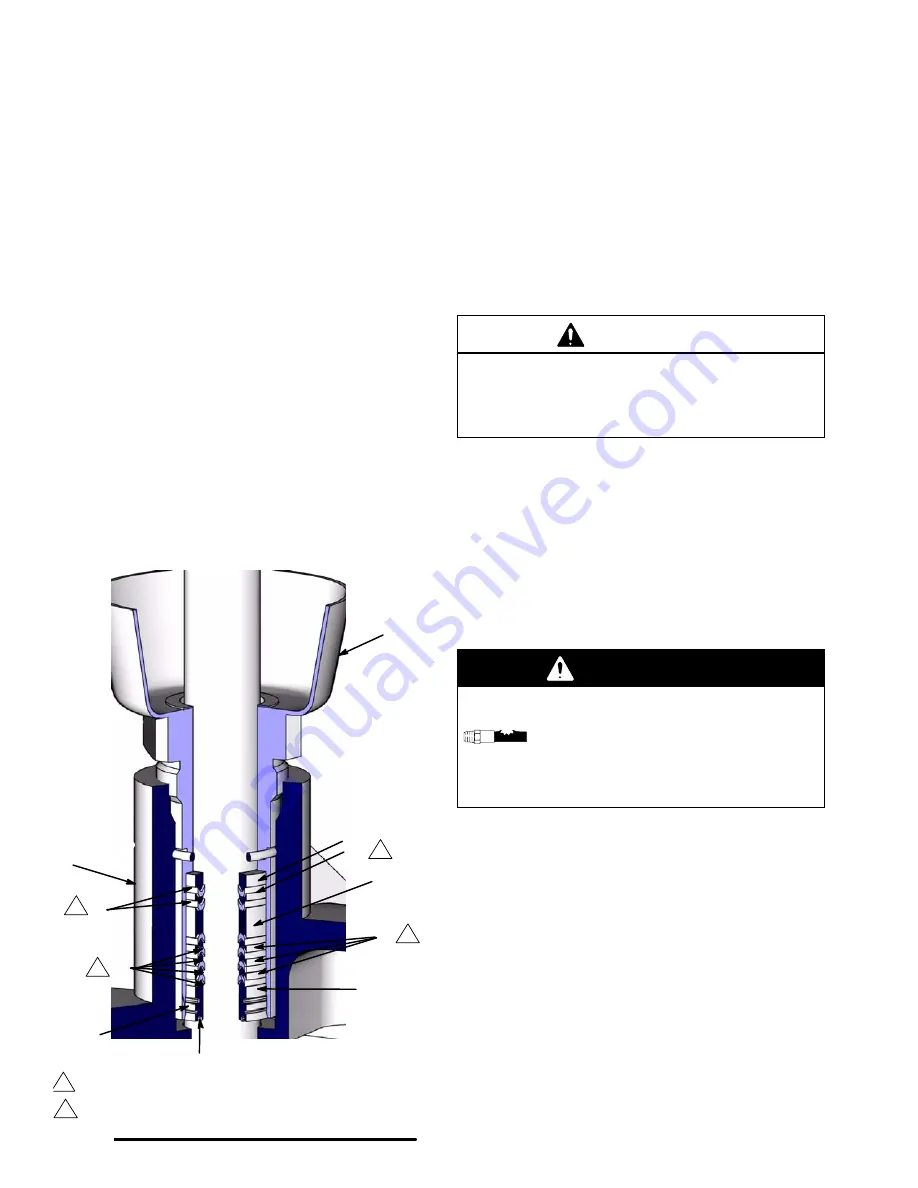
22
309136
Service
NOTE: Refer to Fig. 14 for Steps 21 and 22.
21. Lubricate three new throat packings (two – 31
{
)
and (one – 35†) and the male gland (30
{
) with
light grease. Holding the packing nut (12), drop the
gland (30
{
) into the packing nut so that the lips
face up. Alternately set the three v-packings with
the lips facing up into the packing nut one at a
time, starting with 31
{
, followed by 35†, and
ending with 31
{
.
22. Lubricate the female gland (42
{
) well and place it
in the packing nut. Lubricate seven new throat
packings (four – 31
{
) and (three – 35†) with light
grease. Alternately set the seven v-packings with
the lips facing down into the packing nut one at a
time, starting with (31
{
), followed by (35†), and
ending with (31
{
). Lightly grease gland assembly
(32) and press fit into wet cup (12) until you feel
the o–ring (A) snap into its groove. Place lubri-
cated o–ring (34) into the groove on the face of the
gland assembly.
Fig. 14
1
Lips of v–packings face up.
2
Lips of v–packings face down.
42
12
30†
35
5
35
31
31
34
32
1
1
2
2
A
NOTE: Refer to Fig. 16 for Steps 23–35 unless other-
wise indicated.
23. Loosely screw the packing nut (12) into the outlet
valve housing (5).
24. Lubricate and install the new o-rings (16*) around
each of the four ball seats (17 and 22).
CAUTION
The orientation of the ball valves in the inlet and
outlet valve housings is critical. Install the parts of
the ball valve exactly as instructed and refer to Fig.
16. If installed incorrectly, the pump will not operate.
25. Place the inlet valve housing (6) on a flat surface
with the ball valve openings facing up. Lubricate
the seals (15*) and set them into each side of the
inlet valve housing.
26. Place the ball guides (14) and balls (13) in the inlet
valve housing.
WARNING
COMPONENT RUPTURE HAZARD
The relief valve seat (22) must be in-
stalled at the fluid inlet, to reduce the
risk of pump overpressurization. It can-
not relieve pressure if installed in anoth-
er location.
27. Press the seat (22) with the pressure relief valve
into the fluid inlet side of the inlet manifold (1).
This seat is not reversible. Orient as shown in the
detail in Fig. 16. Press the other seat (17), with the
unworn side facing out, into the other side of the
inlet manifold.
NOTE: The pressure relief seat kit (22) includes two
seals (15) and two o-rings (16). When installing a new
pressure relief seat, also install the seals and o-rings
on both sides of the fluid inlet manifold (1).
Содержание HIGH-FLO 243737
Страница 39: ...309136 39 Notes ...