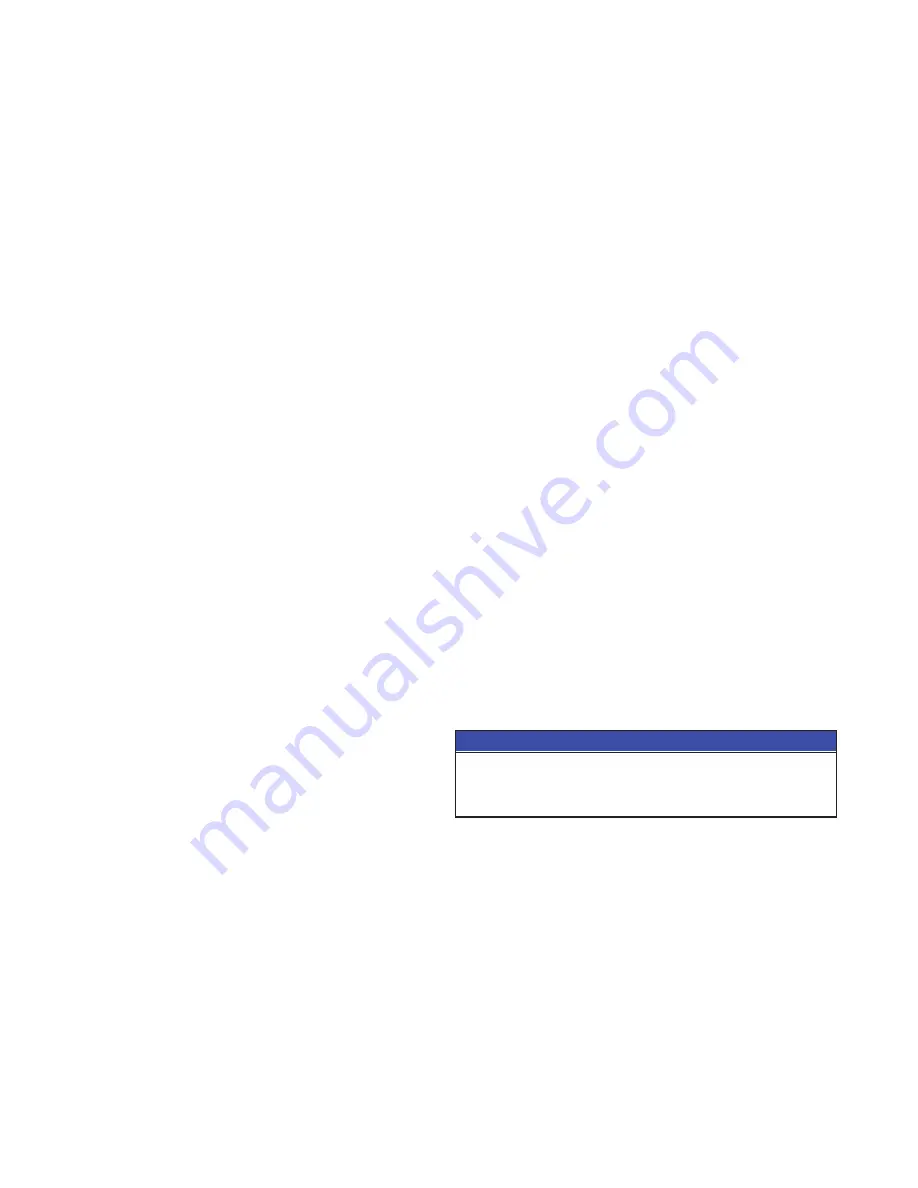
16
STORAGE & MAINTENANCE
INSTRUCTIONS
Engine
The engine instructions that accompany your unit detail
specific procedures for maintenance of the engine. Fol-
lowing the engine manufacturer’s recommendations will
extend engine work life.
Pump
The pump oil must be changed after the first 50 hours
of operation. Once the initial oil change has been
completed, it is recommended the oil be changed every
3 months or 250 hour intervals. If oil appears dirty or
milky, changes may be required at a greater frequency.
Add pump oil and fill only to the center of the sight
glass (Refer to the parts listing for the correct pump oil).
Do not overfill.
Nozzles
Water flow through the spray nozzle will erode the ori-
fice, making it larger, resulting in a pressure loss. Noz-
zles should be replaced whenever pressure is less than
85% of the maximum. The frequency of replacement
will depend upon such variables as mineral content in
the water and number of hours the nozzle is used.
Couplers
There are o-ring seals inside the couplers which will
deteriorate. To replace, simply install a replacement
o-ring to correct the leak. (Additional o-rings can be
purchased from your dealer.)
Fuel Water Separator
The fuel filter has a built in water separator. Occasion-
ally the water has to be drained from the separator.
Follow the procedures listed below:
• Check the collection bowl daily
• Ensure the unit is off and place an oil catch basin
under the fuel cartridge.
• Loosen the drain plug to allow the fuel/water con-
taminants to flow into the catch basin.
• Retighten the drain plug when completed.
• Dispose of drainage according to environmental
regulations in your area.
Burner Air Adjustment
The air shutter has been factory preset for proper
operation between sea level and 2000 feet elevation at
standard conditions (60°F ambient water and air tem-
peratures). To assure maximum combustion efficiency
at colder temperatures and higher altitudes, it will be
necessary to adjust the air supply to the combustion
chamber. A smoke spot test is recommended during
any air shutter adjustment. This will aid in maximizing
the burner efficiency and avoid inefficient operation and
excessive sooting of the combustion chamber.
1. The machine must be running and the burner ON.
2. Take a smoke spot test to determine if more or less air
is required for proper combustion.
• If the test is greater than #3 smoke, turn the shutter
arm counterclockwise to increase the air flow into
the combustion chamber.
• If the test is yellowish in color, turn the shutter arm
clockwise to decrease the air flow into the combus-
tion chamber.
3. Hold onto the air shutter adjusting arm and loosen the
locking nut. Move the shutter in 1/8” increments and
retighten the locking nut after each 1/8” movement.
4. Trigger the gun on the off slowly to make sure there is
proper ignition. Slight or not puffing on the ignition, and
a smoke spot test of less than #3 smoke is good.
5. Repeat steps 2 and 3 until step 4 is attained.
Leaks
Promptly eliminate any leaks found in the pumping sys-
tem by removing suspect parts, applying thread sealant
to the threads and reinstalling.
NOTICE
If using
tape, be certain no tape gets inside
any plumbing to prevent the possibility of a plugged
spray nozzle.
PTFE
Содержание 3A0592B
Страница 21: ...21 Notes ...
Страница 22: ...22 Pressure Washer Parts 262298 Model 3540 GHW ...
Страница 24: ...24 Engine Pump Assembly Parts Item 17 for use with Model 3540 GHW ...
Страница 26: ...26 Pump Assembly Parts 16E609 for use with Model 3540 GHW ...
Страница 28: ...28 Unloader Manifold Assembly Parts Item 8 for use with Model 3540 GHW ...
Страница 30: ...30 Heat Exchanger EMF Assembly Parts Item 31 for use with Model 3540 GHW ...
Страница 32: ...32 Bracket Electrical Box Assembly Parts Item 28 for use with Model 3540 GHW ...
Страница 34: ...34 Decal Placement Parts 262298 Model 3540 GHW ...
Страница 36: ...36 Notes ...