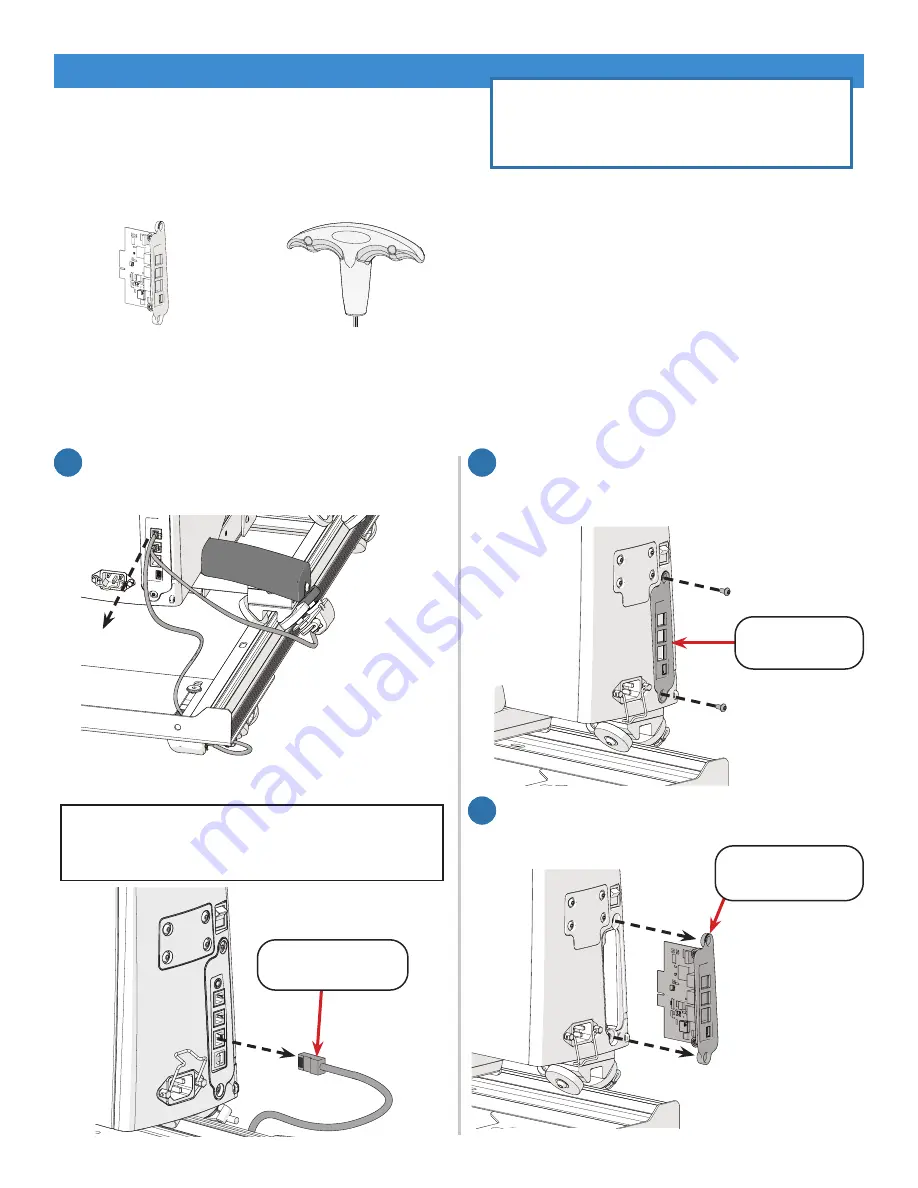
28
19X Service Manual
Replacing the Main Board
Parts & Tools Needed:
Instructions
Take the following steps to replace the main board:
1
Power off the machine and unplug the
encoders from the back.
Main Board Assembly
SMP-09-14303
To avoid damaging the main board
circuitry, keep it in the packaging until
you are ready to install it.
T-handle Allen
Wrench 2.5 mm
2.5 mm
Note
: If you have QuiltMotion installed,
unplug the
6P/6C QuiltMotion cable
from
the back of the machine.
6P/6C QuiltMotion
Cable
2
Use the 2.5 mm Allen wrench to remove the
two screws holding the
main board cover
in place.
Main Board
Cover
3
Remove the
old main board assembly
from the machine.
Old Main Board
Assembly