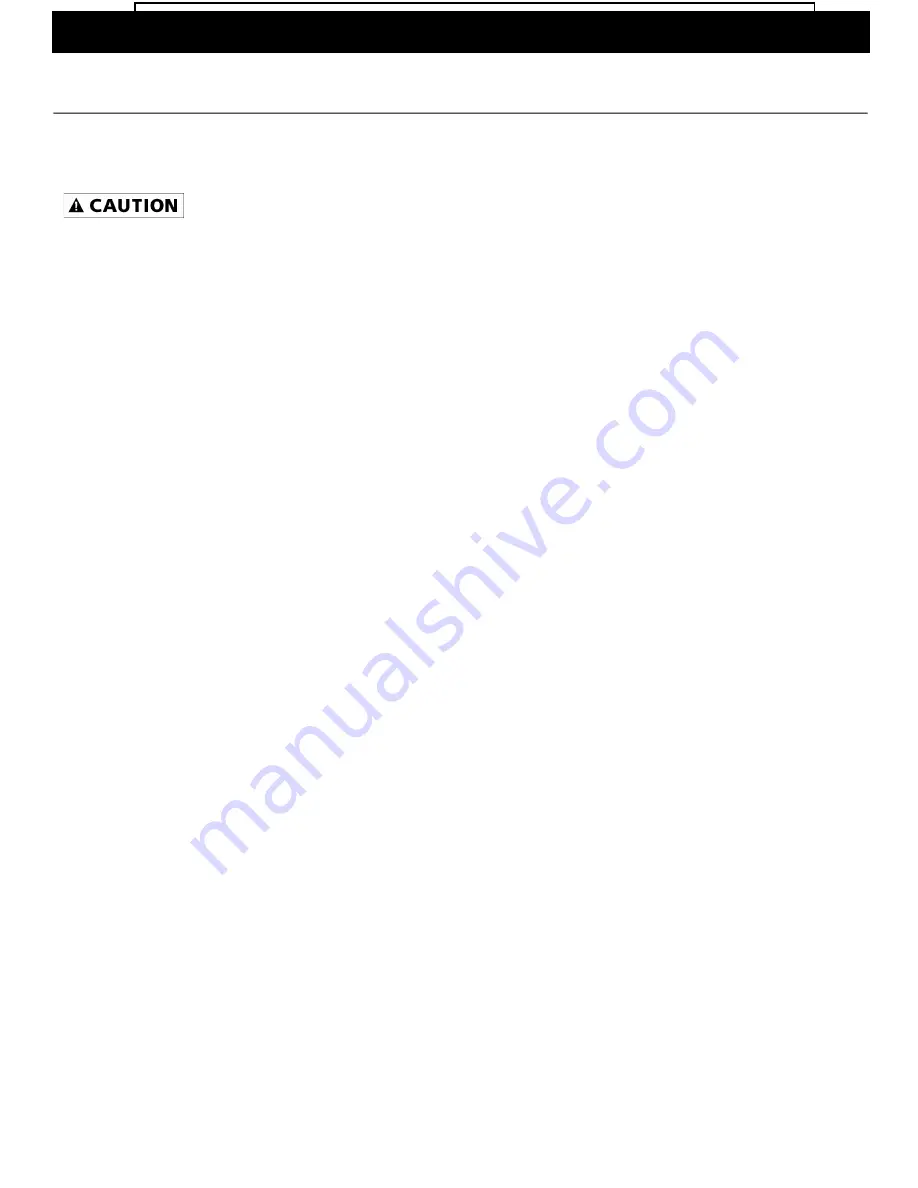
5587-250-00
5
9/2017
Specifications Information and Repair Parts Manual
x
6” Trash Pump
1.
Refer to "Sliding Engine Sled Operation" section for
procedure to access the volute and inside of the casing.
2.
Remove casing O-ring (Ref. No. C35) from outside diameter
of volute (Ref. No. C24) flange.
A mechanical means of supporting the volute during this
procedure is recommended. The volute casting weighs 50 lbs.
3.
Remove three 1/2-13 x 1-1/4" cap screws holding volute to
pump adapter (Ref. No. 28). Slide volute out of adapter
machined pocket.
4.
Replace worn parts as necessary.
NOTE:
When replacing volute, attach a new volute gasket (Ref. No.
C36) to new volute with fasteners.
NOTE:
Before installing new parts, clean all mating surfaces
thoroughly.
5.
Install volute aligning flange outside diameter with adapter
machined pocket. Replace three 1/2-13 cap screws. Check
for interference between impeller face and volute by slowly
rotating engine shaft. See SHIM ADJUSTMENT section for
procedure to set impeller clearance.
6.
Inspect casing O-ring for cracks or tears, replace if
necessary. Install O-ring on outside diameter of volute
flange.
7.
Slide engine sled and engine assembly into casing, align
outside diameter of volute flange with casing machined
inside diameter, do not pinch casing O-ring. Install four 5/8-
11 hex bolts and nuts. Tighten six 1/2-13 hex nuts clamping
engine sled in position.
IMPELLER STUB SHAFT BEARING REPLACEMENT
Gas engine units are equipped with a permanently lubricated impeller
shaft ball bearing (Ref. No. E14). Diesel engine units are equipped with
two bearings. These bearings support the radial and axial loads
produced by the impeller reducing the load on the engine crankshaft
bearings. The bearing does not require lubrication but should be
inspected periodically for wear or water damage from a leaking shaft
seal. As part of a maintenance schedule, the bearing should be
replaced periodically.
1.
Refer to "Sliding Engine Sled Operation" section. Access
impeller as described.
2.
Refer to MECHANICAL SEAL REPLACEMENT section.
Follow steps 1 through 3; remove impeller, impeller shims,
shaft sleeve, seal and seal plate.
3.
Remove shaft washer.
4.
Remove cap screws (Ref. No. E20 or E21) fastening bearing
housing to engine (Ref. No. E38). Diesel engine units:
Loosen set screw in impeller stub shaft. Remove bearing
housing assembly from engine by sliding away from engine.
Gas engine and Vanguard diesel units: disengaging engine
PTO shaft from impeller stub shaft. Do not lose shaft key
(Ref. No. E16). Yanmar diesel engine units: disengaging
flywheel drive hub attached to impeller stub shaft from
flywheel drive plate and flywheel bearing.
5.
On appropriate bearing press, press stub shaft and bearing
from bearing housing adapter. Remove bearing from stub
shaft.
6.
Replace bearing with equivalent ball bearing. Reassemble
bearing, stub shaft and bearing adapter.
7.
Gas engine and Vanguard diesel engine units: insert shaft
key into engine PTO shaft. Align shaft key with stub shaft key
way, slide stub shaft, bearing adapter assembly onto engine
and secure with fasteners. Yanmar diesel units: align
flywheel drive hub with flywheel drive plate and align end if
impeller stub shaft with bearing in flywheel. Slide assembly in
until bearing housing seats on engine bell housing. Secure
with fasteners.
NOTE:
Apply a light coating of anti-seize compound to shaft to prevent
corrosion and galling.
8.
Replace shaft washer onto stub shaft. Flat surface of shaft
washer must face impeller.
9.
Replace seal plate, shaft sleeve, seal, impeller shims and
impeller, turn clockwise to tighten. Refer to MECHANICAL
SEAL REPLACEMENT section; follow step 12 and steps 14
through 19 for reassembly procedure.
CLEANING
These units are designed so that for most cleanout or clogging
problems it should not be necessary to remove hoses or piping. The
suction area can be reached by removing two threaded handles (Ref.
No. C10) and removing suction cleanout cover plate (Ref. No. C11)
and O-ring (Ref. No. C34). To reach the impeller chamber or casing
discharge areas, follow procedures described in SLIDING ENGINE
SLED OPERATION.
NOTE: When replacing cleanout cover plate, carefully wipe clean all
surfaces on which the O-ring has contact. Also make sure the O-ring is
in position in its groove.
ENGINE (DRIVER)
1.
For information pertaining to the engine, engine service and
engine parts, consult the Engine Manual or contact the
nearest authorized service representative or the engine
manufacturer.
2.
Follow engine manufacturer’s operating and maintenance
procedures and recommendations covered in the engine
manual.
3.
Use tachometer-hour meter installed on the engine to log
operating hours. See tachometer-hour meter instruction
sheet included for operating information. Perform engine
maintenance according to recommended hour intervals listed
in engine manual.
4.
An engine oil drain extender has been installed in the engine
oil drain port to assist in changing the engine oil. Adding
longer piping, hose, or a valve to fit each individual’s
maintenance requirements is left to the discretion of the
operator.
5.
Consult engine manual for engine warranty information
needed. Any warranty issues concerning the engine must be
address through the engine manufacturer. Warranty contact
phone number, website, Authorized Service Representative
listing and warranty directions are listed in the engine
manual.
Yanmar 3TNM72
1.
Use the engine fuel system hand primer to prime the engine
with fuel on initial start-up or whenever the fuel system has
been drained. See engine manual for details. Do not use the
engine starter to crank the engine until the fuel system is
primed.
2.
Maximum ambient air temperature during engine operation is
45°C (113°F). Engine may not cool itself effectively if
operated when ambient air temperature exceeds this limit. If
pump is used below 0°C (32°F) do not allow water to freeze
inside the pump. Damage to the pump components will occur
if water freezes inside pump.
3.
Engine speed may be set at 3600 rpm during the priming
cycle. Once pump is fully primed engine speed must be
reduced to a maximum speed of 3200 rpm. Damage to
engine or pump end may result if operated for an extended
period of time at speeds greater than 3200 rpm.
www.PumpAgents.com - Click here for Pricing/Ordering for Pumps and Parts