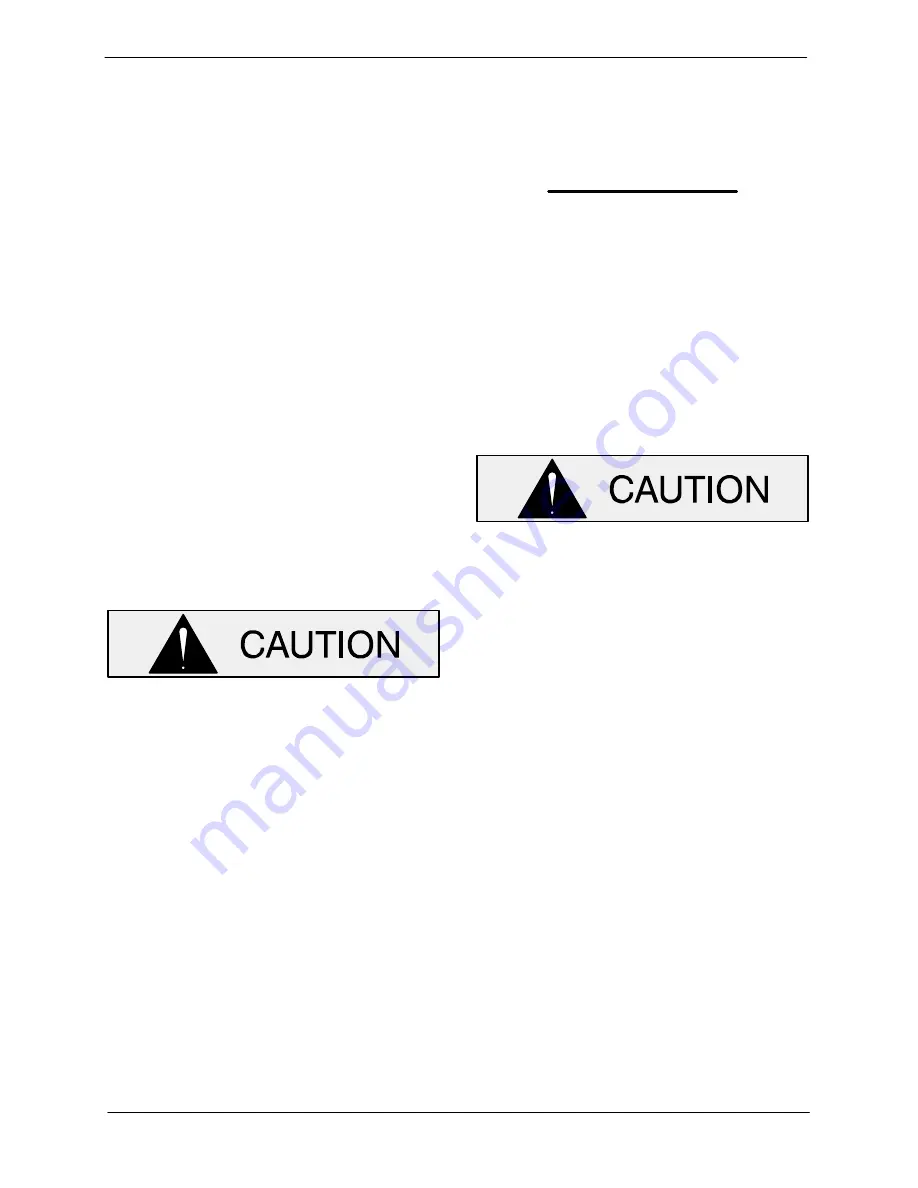
10 SERIES
OM-00652
PAGE B - 5
INSTALLATION
DISCHARGE LINES
Siphoning
Do not terminate the discharge line at a level lower
than that of the liquid being pumped unless a si
phon breaker is used in the line. Otherwise, a si
phoning action causing damage to the pump
could result.
Valves
If a throttling valve is desired in the discharge line,
use a valve as large as the largest pipe to minimize
friction losses. Never install a throttling valve in a
suction line.
A check valve in the discharge line is normally rec
ommended, but it is not necessary in low dis
charge head applications.
With high discharge heads, it is recommended that
a throttling valve and a system check valve be in
stalled in the discharge line to protect the pump
from excessive shock pressure and reverse rota
tion when it is stopped.
If the application involves a high discharge
head, gradually close the discharge
throttling valve before stopping the pump.
Bypass Lines
Self‐priming pumps are not air compressors. Dur
ing the priming cycle, air from the suction line must
be vented to atmosphere on the discharge side. If
the discharge line is open, this air will be vented
through the discharge. However, if a check valve
has been installed in the discharge line, the dis
charge side of the pump must be opened to atmos
pheric pressure through a bypass line installed be
tween the pump discharge and the check valve. A
self‐priming centrifugal pump
will not prime
if
there is sufficient static liquid head to hold the dis
charge check valve closed.
NOTE
The bypass line should be sized so that it does not
affect pump discharge capacity; however, the by
pass line should be at least 1 inch (25,4 mm) in di
ameter to minimize the chance of plugging.
In
low discharge head
applications
(less than 30
feet (9,1 m)), it is recommended that the bypass
line be run back to the wet well, and located 6
inches below the water level or cut‐off point of the
low level pump. In some installations, this bypass
outline may be terminated with a six‐to‐eight foot
(1,8 to 2,4 m) length of 1‐1/4 inch (31,8 mm) I.D.
smooth‐bore
hose; air and liquid vented during
the priming process will then agitate the hose and
break up any solids, grease, or other substances
likely to cause clogging.
A bypass line that is returned to a wet well
must be secured against being drawn into
the pump suction inlet.
It is also recommended that pipe unions be in
stalled at each 90
_
elbow in a bypass line to ease
disassembly and maintenance.
In
high discharge head applications
(more than
30 feet (9,1 m), an excessive amount of liquid may
be bypassed and forced back to the wet well under
the full working pressure of the pump; this will re
duce overall pumping efficiency.
Therefore, it is
recommended that a Gorman‐Rupp Automatic
Air Release Valve be installed in the bypass line.
Gorman‐Rupp Automatic Air Release Valves are
reliable, and require minimum maintenance. See
Automatic Air Release Valves
in this section for
installation and theory of operation of the Auto
matic Air Release Valve. Consult your Gorman‐
Rupp distributor, or contact the Gorman‐Rupp
Company for selection of an Automatic Air Release
Valve to fit your application.