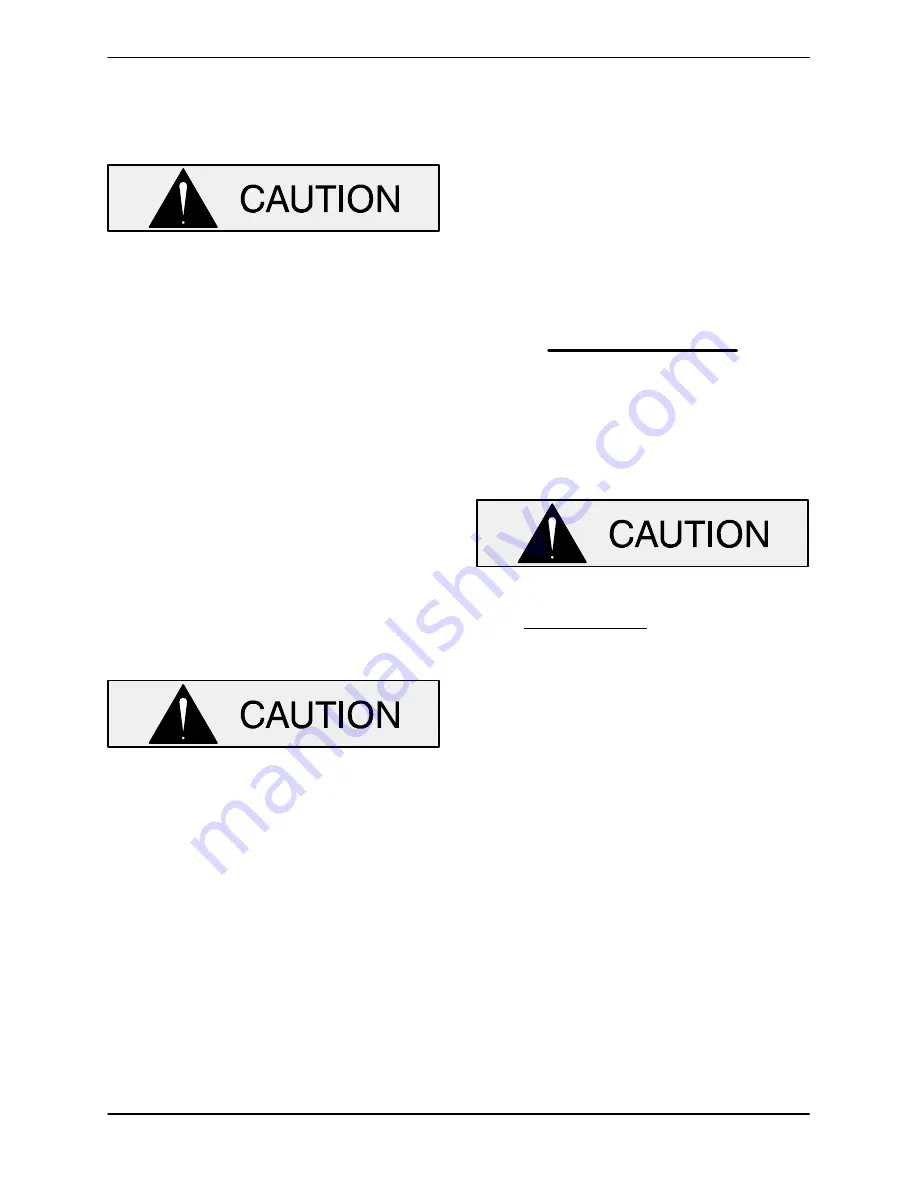
MR−05702
PA SERIES PUMPS
MAINTENANCE & REPAIR
PAGE C − 15
If heating the bearings is not practical, use a suit-
ably sized sleeve, and an arbor (or hydraulic) press
to install the bearings on the shaft.
When installing the bearings onto the
shaft,
never
press or hit against the outer
race, balls, or ball cage. Press
only
on the
inner race.
Install the thrust washer (23) and secure the out-
board bearing (18) to the shaft with the retaining
ring (21).
Apply a light coating of oil to the lips of the inboard
oil seals (42) and press them into the intermediate
with the lips positioned as shown in Figure C−3.
Press the oil seals into the housing until they are
centered in the intermediate bore.
Slide the shaft and assembled bearings into the in-
termediate bore until the retaining ring on the out-
board bearing (18) is fully seated against the inter-
mediate. Use caution not to damage the lip seals
(42) on the shaft threads.
When installing the shaft and bearings into
the bearing bore, push against the outer
race.
Never
hit the balls or ball cage.
Apply a light coating of oil to the lip of the outboard
oil seal (22) and press it into the bearing cover (17)
with the lip positioned as shown in Figure C−3.
The face of the oil seal should be just flush with the
outer face of the bearing cover.
Install the bearing cover gasket (24) and secure
the bearing cover to the intermediate with the hard-
ware (15 and 16).
Be careful
not to damage the lip
of the oil seal (22) on the shaft keyway.
Lubricate the bearings as indicated in
LUBRICA-
TION
at the end of this section.
Securing Intermediate And Drive Assembly To
Power Source
(Figure C−4)
Install the shaft key (19, Figure C−3) in the shaft
keyway. Position the flexible portion of the coupling
assembly (1) on the shaft as shown in Figure C−4.
NOTE
The flexible portion of the coupling must be proper-
ly positioned on the shaft. The heads of the caps-
crews in the center of the coupling
must be posi-
tioned away from the pump end of the shaft
.
Align the keyway in the bushing (2) with the shaft
key, and slide it onto the shaft to the dimension
shown in Figure C−4. Rotate the flexible portion of
the coupling until the tapped holes for the two set-
screws align with those in the bushing, and install
the setscrews.
Make certain that the flexible portion of the
coupling is mounted as shown in Figure
C−4.
This is critical.
If the coupling is not
properly positioned on the shaft, the
coupling parts may not fully engage, or a
pre-load condition can cause premature
bearing failure.
The coupling must be positioned 0.54
inches (13,7 mm) from the end of the shaft.
This will allow the two portions of the cou-
pling to fully engage when the drive flange
is secured to the bellhousing, without pre-
loading the bearings.
With the flexible portion of the coupling and the
bushing properly positioned on the shaft, tighten
the two setscrews in an alternating sequence until
the bushing and coupling are fully secured. Torque
the setscrews to 23.3 ft. lbs. (280 in. lbs. or 3,2 m.
kg.).
If the complete coupling assembly is being re-
placed, apply ‘Loctite Retaining Compound No.
242’ or equivalent to the threads of the hardware (3
and 4), and secure the outer ring of the coupling to
the flywheel by torquing the hardware to 45 ft. lbs.
(540 in. lbs. or 6,2 m. kg.).