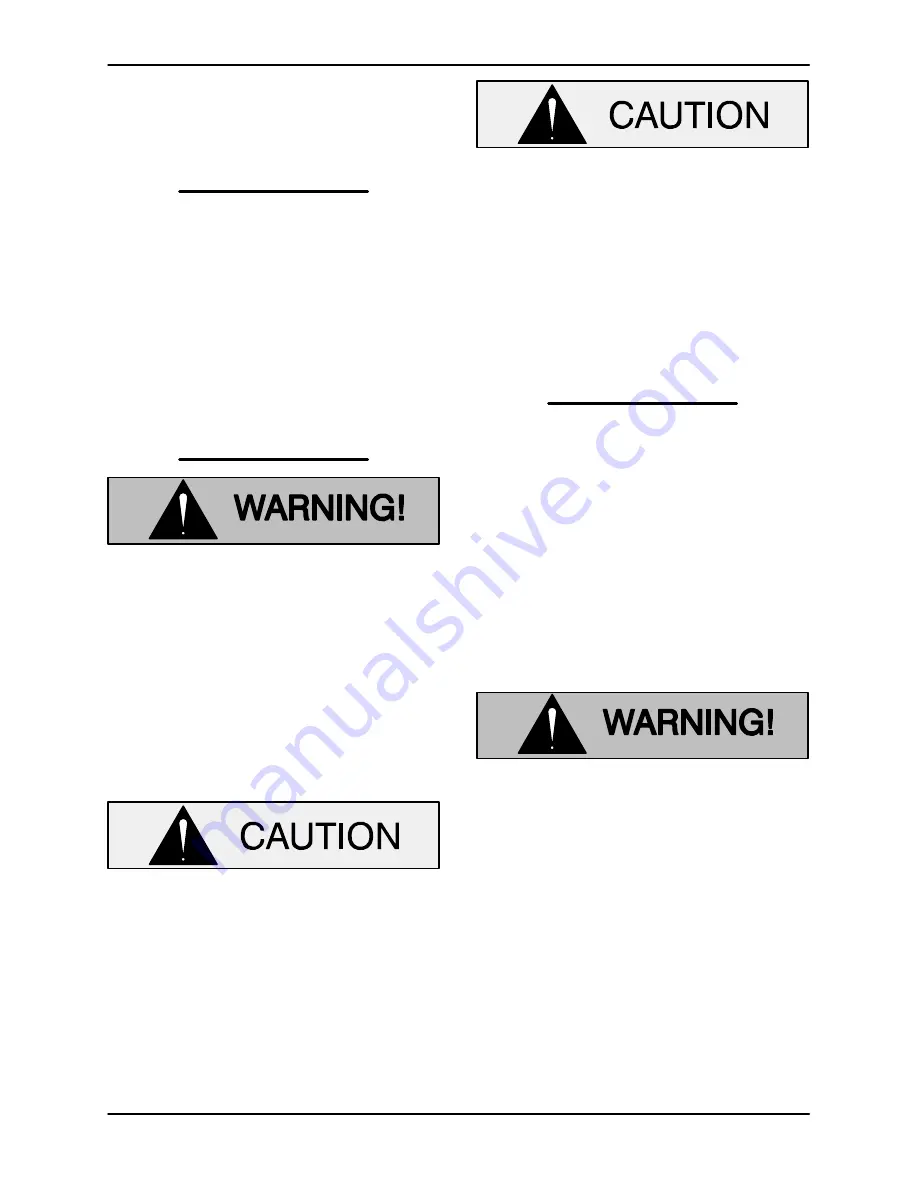
OM-00745
80 SERIES
MAINTENANCE & REPAIR
PAGE E - 7
NOTE
If a hot oil bath is used to heat the bearings, both the
oil and the container must be
absolutely
clean. If
the oil has been previously used, it must be
thor
oughly
filtered.
Heat the bearings to a uniform temperature
no
higher than
250
_
F (120
_
C), and slide the bearings
onto the shaft, one at a time, until they are fully
seated. This should be done quickly, in one con
tinuous motion, to prevent the bearings from cool
ing and sticking on the shaft.
NOTE
When installing the bearings, be sure to install them
with the offset of the bearings positioned in the di
rection as shown in Figure 1.
Use caution when handling hot bear
ings to prevent burns.
After the bearings have been installed and allowed
to cool, check to ensure that they have not moved
out of position in shrinking. If movement has oc
curred, use a suitably sized sleeve and a press to
reposition the bearings.
If heating the bearings is not practical, use a suit
ably sized sleeve and an arbor (or hydraulic) press
to install the bearings on the shaft.
When installing the bearings onto the
shaft,
never
press or hit against the outer
race, balls, or ball cage. Press
only
on the
inner race.
If removed, use snap ring pliers to install the in
board bearing retaining ring (18) in the groove in
the pedestal.
Slide the shaft and assembled bearings into the
pedestal until the inboard bearing is fully seated
against the retaining ring.
When installing the shaft and bearings into
the bearing bore, push against the outer
race.
Never
hit the balls or ball cage.
Install the same thickness of bearing adjusting
shims (12) as previously removed. Reinstall the re
taining ring (15) and check shaft endplay.
NOTE
Shaft endplay should be .002 to .010 inch (0,05 to
0,25 mm). Add or remove bearing adjusting shims
to obtain this endplay.
Install the slinger ring (9) and shaft key (13). Install
any leveling shims used under the pedestal feet.
Secure the pedestal to the base using the pre
viously removed mounting hardware.
Lubricate the bearing housing as indicated in
LU
BRICATION
at the end of this section
.
Seal Reassembly and Installation
(Figures 1 and 3)
Clean the seal cavity and shaft with a cloth soaked
in fresh cleaning solvent.
Most cleaning solvents are toxic and
flammable. Use them only in a well ven
tilated area free from excessive heat,
sparks, and flame. Read and follow all
precautions printed on solvent contain
ers.
The seal is not normally reused because wear pat
terns on the finished faces cannot be realigned
during reassembly. This could result in premature
failure. If necessary to reuse an old seal in an emer
gency,
carefully
wash all metallic parts in
fresh
cleaning solvent and allow to dry thoroughly.
Handle the seal parts with extreme care to prevent
damage. Be careful not to contaminate precision
finished faces; even fingerprints on the faces can
shorten seal life. If necessary, clean the faces with a