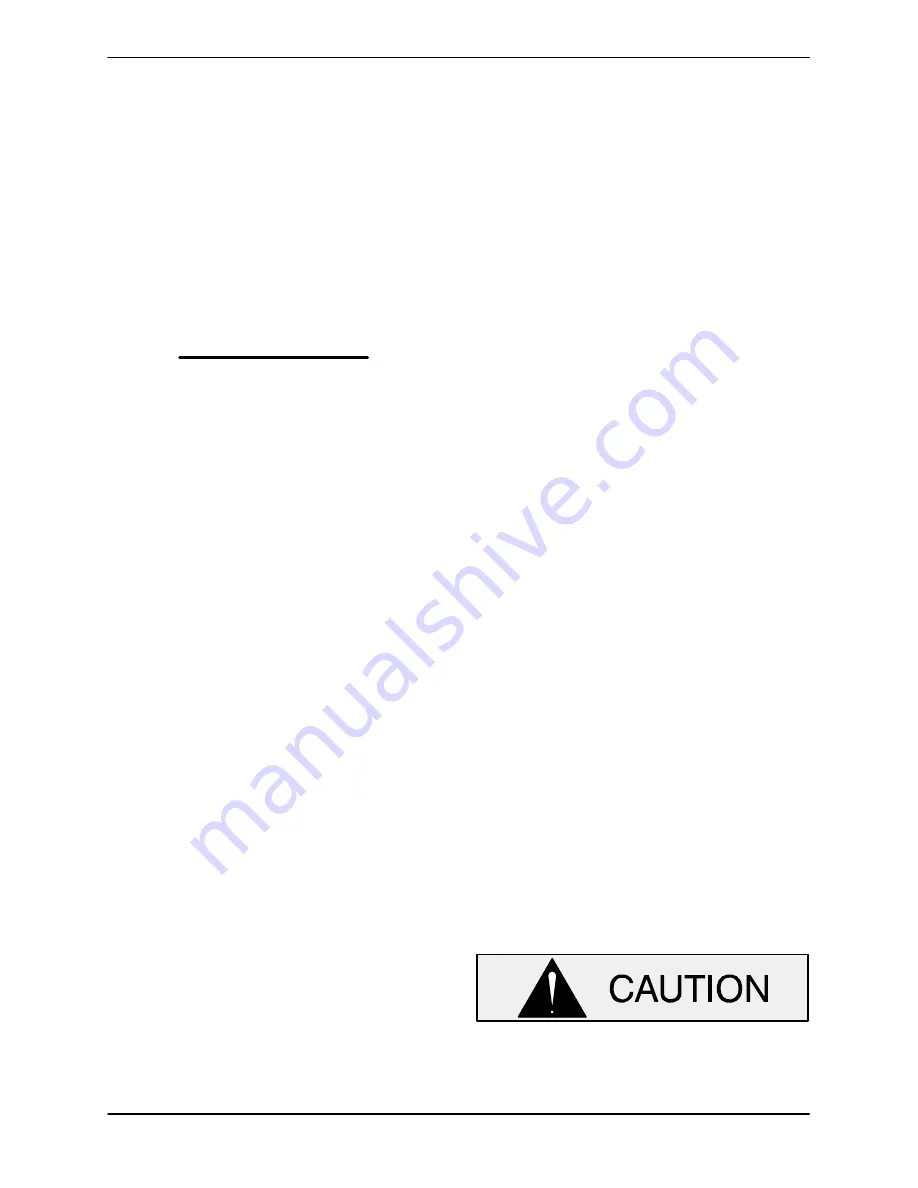
OM-01516
D SERIES
MAINTENANCE & REPAIR
PAGE E - 15
free from excessive heat, sparks, and flame.
Read and follow all precautions printed on sol
vent containers.
Inspect the bearing cap for wear or damage and
replace if necessary.
NOTE
The bearing cap consists of an upper and lower half
secured with the hardware (2, 3 and 4). The cap is
machined as one piece before being split to ensure
concentricity of the bore, and is available only as an
assembly.
Screw the bearing cap assembly onto the plunger
rod until fully seated against the spring retaining
nut.
Loosen the hardware (2, 3 and 4), and position the
bearing cap over the crankshaft roller bearing (33,
Figure 4). Secure the plunger rod assembly by
tightening the hardware (2, 3 and 4).
Secure the eccentric guard (41, Figure 1) with the
hardware (38, 39, 40, 43, 44, and 45, Figure 1).
Lubricate the plunger rod assembly as described
in
LUBRICATION
, Section E.
Diaphragm Installation
(Figure 3)
Position the diaphragm (6) on the upper dia
phragm plate (9), making sure the lip is properly
seated. Slide the studs in the lower diaphragm
plate (8) through the holes in the upper diaphragm
plate, and secure with the nuts (10).
(Figure 1)
Secure the diaphragm pot assembly (34) to the di
aphragm ring (23) with the hardware (31, 32 and
33).
Suction And Discharge Check Valve Installation
(Figure 2)
Inspect the check valve components and replace
as required. Subassemble the check valve weights
(26, 28, 33 and 34) and check valves (27 and 37)
with the hardware (29, 30, 35 and 36).
If the inboard discharge flange (18) was removed,
clean the mating surfaces and install the gasket
(12). Secure the flange to the diaphragm pot (1)
with the hardware (14 and 15).
Subassemble the valve seat (24) and discharge
check valve (25) to the discharge elbow (23) with
the weights positioned as shown in Figure 2, and
secure with the hardware (16 and 17).
Clean the mating surfaces of the valve seat and dis
charge flange. Install the gasket (19) and secure
assembled discharge elbow, check valve, and seat
to the discharge flange with the hardware (21 and
22).
Check the operation of the check valve to ensure
proper seating and free movement.
Subassemble the suction check valve (32). Clean
the mating surfaces, and position the gasket (10),
check valve assembly, and valve seat (31) against
the diaphragm pot with the weights positioned as
shown in Figure 2. Secure with the hardware (5
and 6).
Check the operation of the check valve to ensure
proper seating and free movement.
Secure the suction accumulator (3) to the dia
phragm pot with the hardware (8 and 9).
Connect the suction and discharge piping as de
scribed in
INSTALLATION
, Section B.
Refer to
OPERATION
, Section C before starting
the pump.
LUBRICATION
Plunger Rod Assembly
(Figure 1)
The crankshaft roller bearing (33, Figure 4)
should be lubricated thoroughly after each
8 hours of operation. Failure to do so may
cause the bearing to overheat and fail.