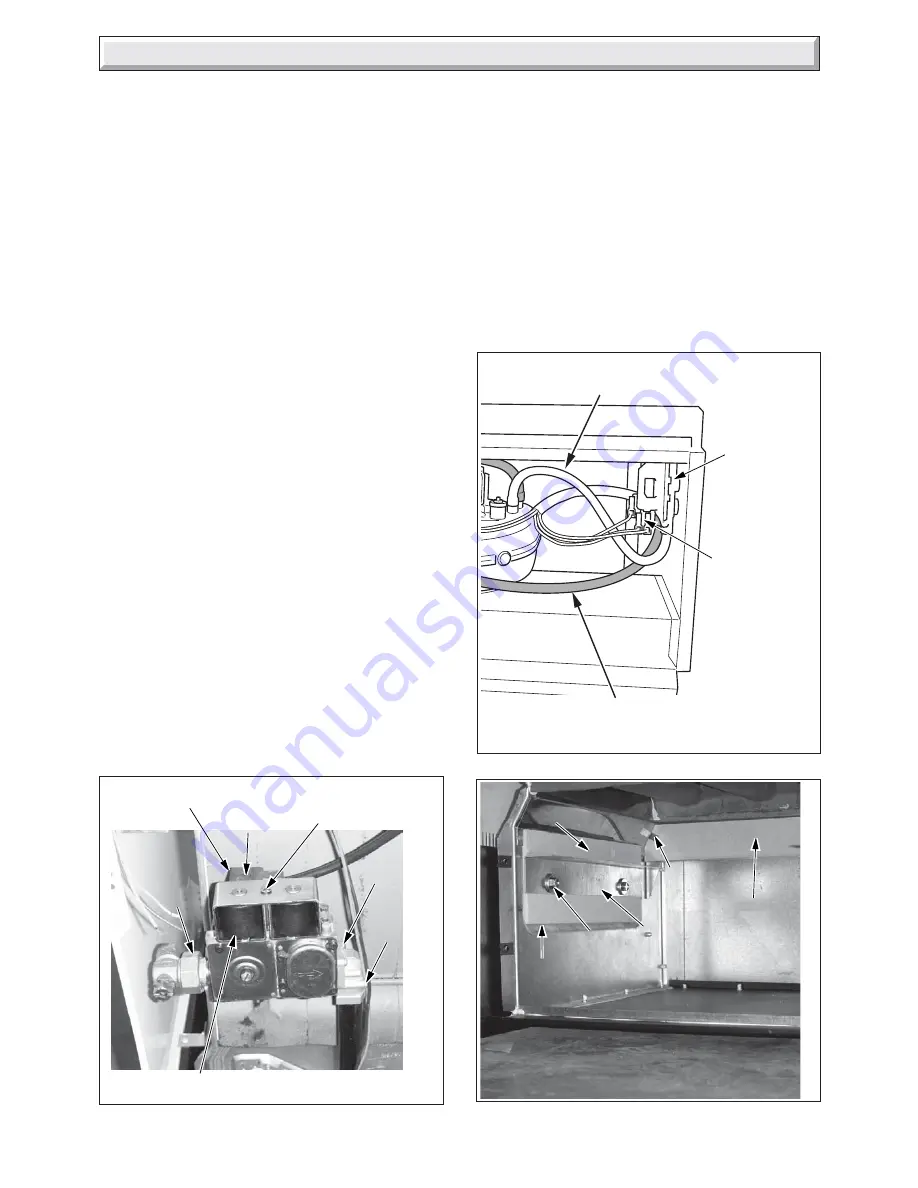
27
221958B
10 Replacement of Parts
Diagram 10.6
REAR
INSULATION
PANEL
SECURING
NIB
SIDE
INSULATION
0000
Diagram 10.4
GAS
SERVICE
COCK
UNION
ELECTRICAL
PLUG
SHORT
SCREWS (2)
LONG
SCREWS
(2)
SOLENOID
SECURING SCREW
SOLENOID ASSEMBLY
BURNER
SUPPORT
BRACKET
NUTS
10.5 Solenoid
Remove the electrical plug from the multifunctional control and
remove the securing screw and then the solenoid assembly,
see diagram 10.4.
10.6 Burner
Refer to the relevant paragraphs of the servicing section to
remove the burner from combustion chamber.
10.7 Injector
Refer to the relevant paragraphs of the servicing section to
remove the burner from combustion chamber.
The injector can then be unscrewed from the manifold.
When replacing use a little jointing compound on the external
thread only, to ensure a gas tight seal.
10.8 Air Pressure Switch
Remove front panel to gain access, see section 6.8.
Refer to the relevant paragraphs of the servicing section to
remove the burner from combustion chamber.
Remove the air pressure tubes and electrical connections from
the switch, release the securing screws and remove the switch,
see diagram 10.5.
When fitting the replacement make sure that the air pressure
tubes are fitted with the clear tube from the air pressure switch
to the front fan connection, as shown in diagram 10.5 and the
electrical connections are made as shown in wiring diagram
9.4.
10.9 Fan
Remove front panel to gain access, see section 6.8.
Refer to the relevant paragraphs of the servicing section to
remove the burner from combustion chamber.
Remove the electrical connections and air pressure tubes from
the fan.
Note: Remove the electrical connections by pulling insulation
boots only.
Undo the screw securing the fan to the flue hood and disengage
fan from flue hood.
When re-assembling, make sure that the air pressure tubes are
fitted as before and that the fan duct engages fully into the flue
duct extension piece.
The polarity of the electrical connections is not important.
SECURING
SCREW
Diagram 10.5
10259
FRONT AIR PRESSURE
SWITCH TUBE (CLEAR)
AIR
PRESSURE
SWITCH
ELECTRICAL
CONNECTORS
REAR AIR PRESSURE
SWITCH TUBES (RED)
10.10 Insulation
Refer to the relevant paragraphs of the servicing section to
remove the burner from combustion chamber.
Sides
Undo the burner support bracket nuts and remove support
bracket and insulation, see diagram 10.6.
Refit support bracket with new side insulation.
Rear
Bend forward rear insulation securing nibs, one on each side,
to release insulation.
Fit new insulation and bend back securing nibs.