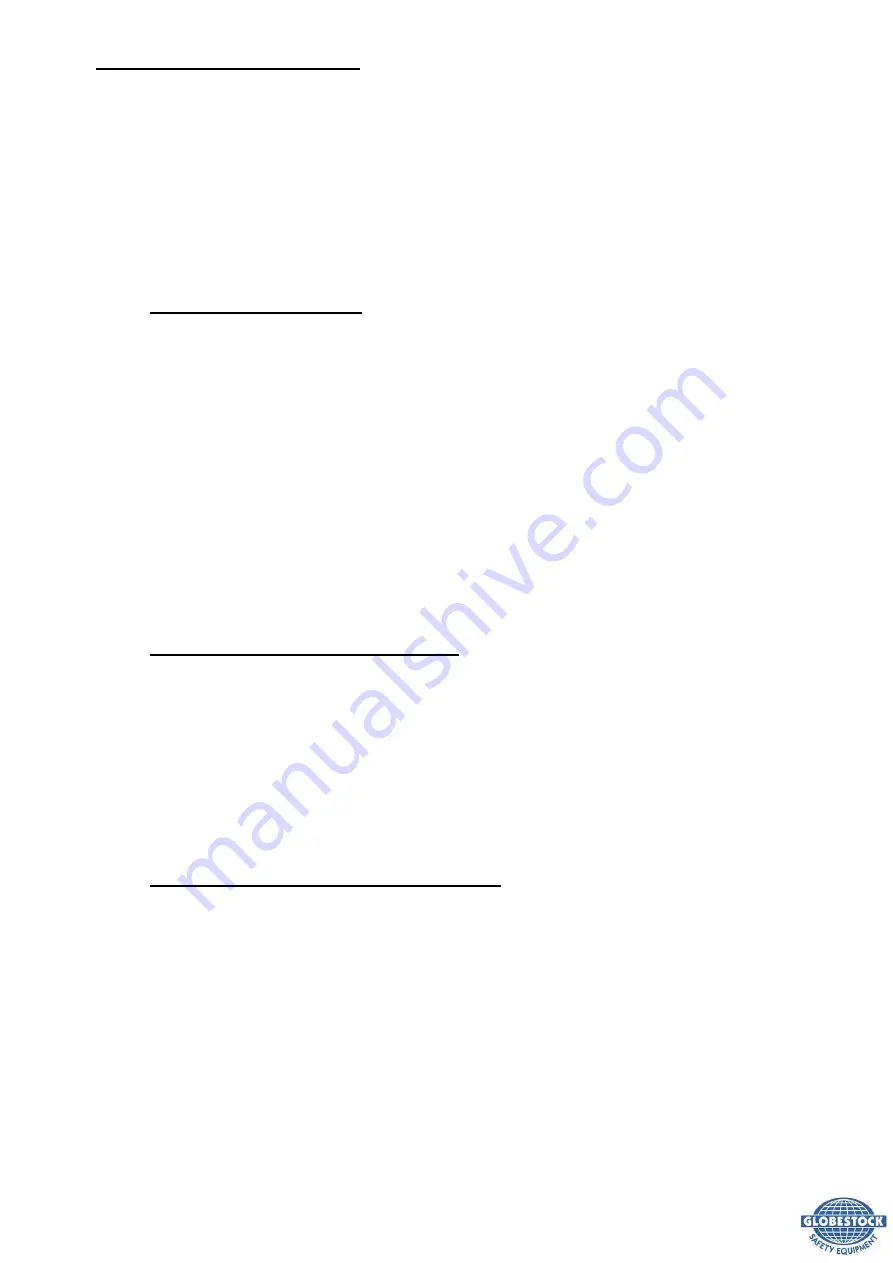
9
Issue 01
6.
Inspection & Maintenance
Like all safety critical devices, the G.Tripod requires regular inspection and maintenance to ensure that the
unit functions safely and correctly.
Repairs or servicing should never be carried out on site or in the field, and should only be completed by the
manufacturer or a service agent approved by the manufacturer. Do not tamper with or modify the unit. Any
alterations or additions to the equipment can only be carried out with the prior written consent of Globestock
Ltd.
a.
Periodic Examination
(This satisfies the requirements of LOLER).
The G.Tripod should be periodically inspected by a competent person at
least once in every 6
months,
dependent upon the frequency of use, and the operating environment. The ‘Examination
Record’ found at the back of this booklet, outlines the main examination criteria.
On passing this detailed inspection the record can be completed, signed off and the unit returned
for use.
Any observed faults must be rectified by the manufacturer or an approved agent of the
manufacturer. If necessary, or
in any doubt
, return the G.Tripod for service, test and re-
certification. (See below).
It is recommended that the Tripod is marked with the date of when the next inspection is due.
b.
Service, Test & Re-Certification
The G.Tripod must be serviced and re-certified annually in the event of a fall arrest or if any doubt
should arise concerning the units condition.
Only a Globestock Ltd approved servicing agency can be used for this.
On completion of a service and retest, a new Test Certificate will be issued which validates the unit
for a further year of use. (This can also cover one 6 monthly LOLER examination).
c.
Cleaning, Storage & Transportation
The G.Tripod may be cleaned using warm water with a mild detergent. It should then be allowed
to dry.
The unit should be stored in a clean, dry, chemical free environment.
When transporting the G.Tripod it should be boxed or retained to prevent damage or
deterioration.
Any accessories/equipment/brackets must be removed prior to transportation.
Once the product has reached it’s end of life it can be broken down and component parts recycled.