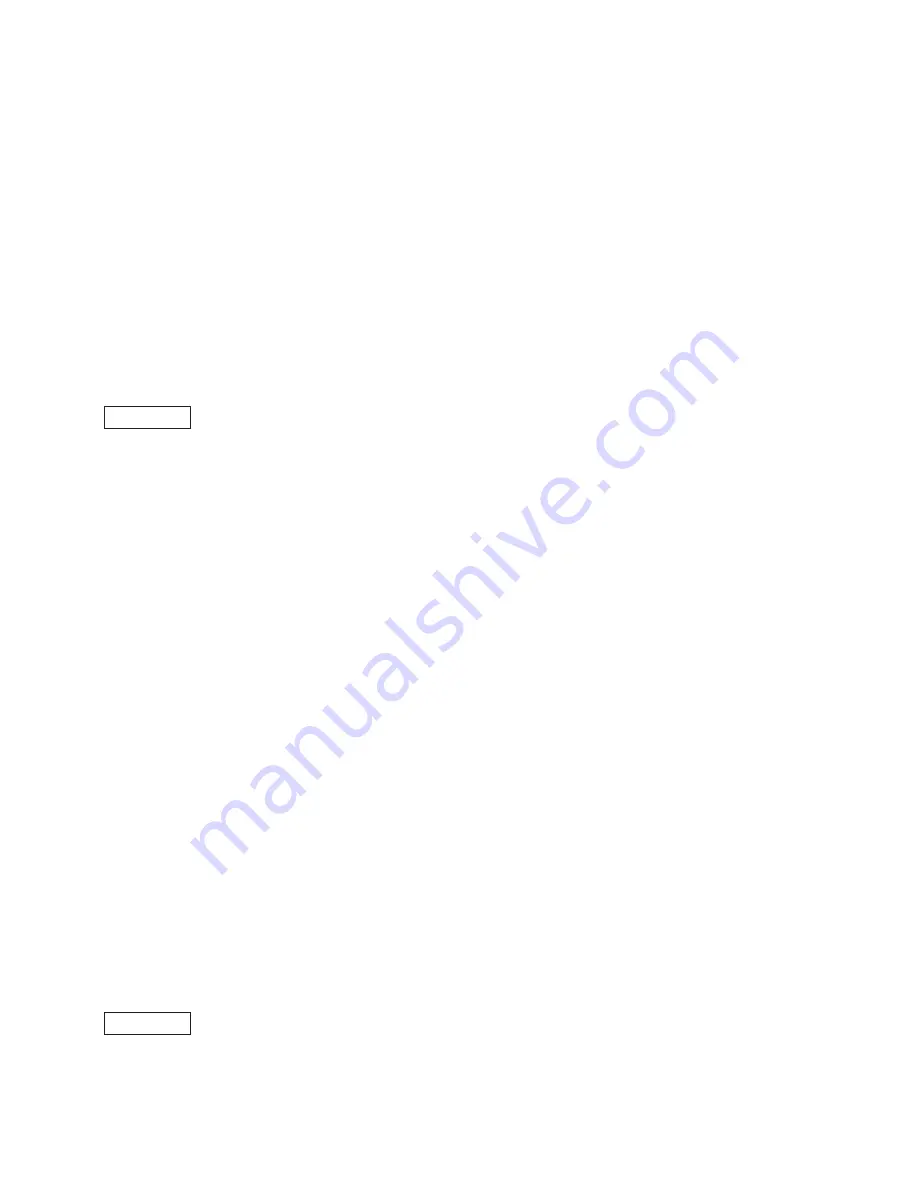
8
BP8085 Repair Instructions
To Check Valves
Remove screws (58), lift discharge casing (50B) up and away. Take out discharge valve
tension element (53). Pull out assembled valves (51), discharge valve adaptor (56) and
suction valve tension element (52) with fi tting tool (part number 04967).
Dismantling valves:
the spring tension cap (51A) is screwed together with the valve seat
(51E). Screw off spring tension cap, take out springs (51C) and valve plate (51D).
Examine o-rings and the sealing surfaces on the pressure rings and guide rings. Replace
worn parts.
Coat threads of the valve seat with silicon grease or molycote anti-seize Cu-7439 when
reassembling. Before refi tting the valves and tension elements, clean the sealing surfaces
in the casing and check for any damage. Tighten screws (58) at 132.7 ft.-lbs. (180 Nm).
Check torque tension after 8-10 operating hours.
To Check Seals and Plunger Pipe
Important!
If necessary, support the pump head by resting it on wooden blocks or by using
a pulley.
Screw off hexagon nuts (49A), remove pump head together with seal case (38) from
intermediate casing (53). If necessary, carefully tap the valve casing (50) past the centring
stud (50A) using a rubber hammer. Pull the seal case (38) out of the valve casing (50) (if
necessary using two screwdrivers placed into the front o-ring groove). Examine o-rings
(38A) and coat with silicon grease before fi tting.
Remove tension screw (36C) and take the intermediate casing (53) together with all
mounted parts out of the drive.
Pull plunger pipe out of seal assembly and check for any damage.
Clean parts from positions 38 to 44, examine them and replace if necessary. Coat new
parts generously with silicone grease before fi tting.
Insert the seal unit (40, 41, 42, 44) into the intermediate casing. Push the ceramic plunger
carefully through the seals from the crankcase side. If necessary, the seals can be held on
the other side of the seal sleeve using a suitable pipe support.
Coat the pressure sleeves (46) lightly with anti-corrosive grease (e.g. molycote no. Cu-
7439) and screw it into the adjusting ring. Coat the step of the plunger pipe (36A) cover
with silicon grease and put it onto the back end of the plunger pipe. Lightly coat the
preassembled parts with silicon grease or molycote anti-seize Cu-7439 and insert it into the
pressure sleeve.
Pay attention that the sealing surfaces on the intermediate casing, crankcase and valve
casing are clean and without damage. The components must lie exactly and evenly on one
another. The same exactness applies to all centering positions in the crankcase, pressure
and valve casing. Fit o-rings (36F, G) into the seal ring (36D) and push these past the
tension screw (36C). Lightly coat tension screw (36C) with screw glue and, together with
seal ring (36D), place into the ceramic pipe. Turn the pump manually until the plunger (25)
touches against the plunger pipe. Tighten tension screw at 29.5 ft.-lbs. (40 Nm).
Important!
Thread glue must never come between the plunger pipe (36B) and centring
sleeve (36E). Overtensioning of the plunger pipe by excessive tightening of the tension
screw and/or dirt or damage on the mounting surfaces can cause the plunger pipe to
fracture.