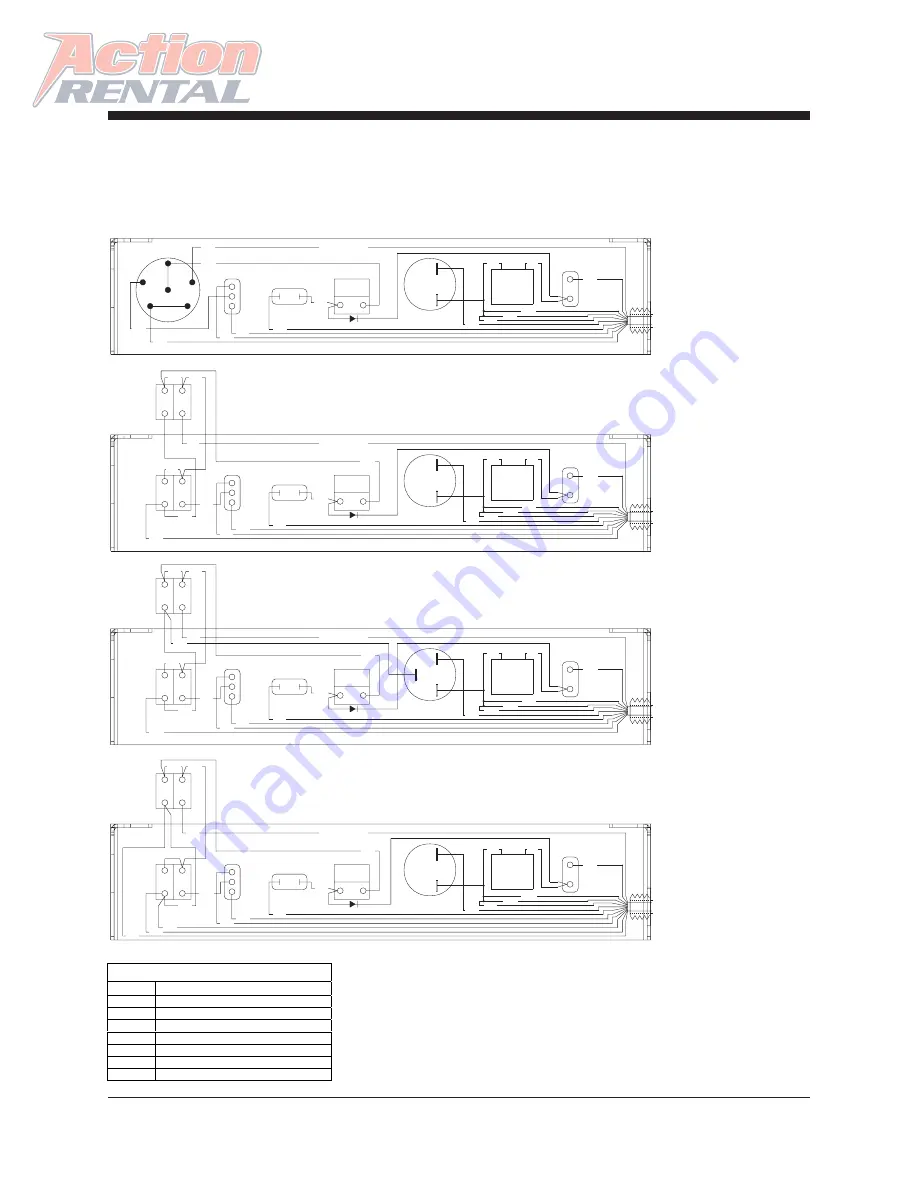
Part No. 72972
Genie GS-2046 and GS-2646 and GS-3246
6 - 9
Section 6 • Schematics
June 2003
REV B
Ground Controls Wiring Diagram
GS-3246
NC
P1
NO
NO
TS66
BN23
CB2
NO NO
KS1
(PLATFORM)
KS1
(GROUND)
(UP)
(DOWN)
G6
-
+
51F
24F
A12
B12
76F
45F
50F
49F
48F
A11
52F
A11 KEY SWITCH
EMERGENCY
DOWN
BATTERY
-
+
BK
RD
60E
B7
53F
25F
29F
41F
60E
NC
P1
NO
NO
TS66
BN23
CB2
NO NO
KS1
(PLATFORM)
KS1
(GROUND)
3
2
1
(UP)
(DOWN)
G6
53F
51F
24F
A12
B12
76F
45F
50F
49F
48F
A11
52F
A11 KEY SWITCH
EMERGENCY
DOWN
BATTERY
-
+
BK
RD
60E
B7
54F
25F
29F
41F
60E
NC
P1
NO
NO
TS66
BN23
CB2
NO NO
KS1
(PLATFORM)
KS1
(GROUND)
(UP)
(DOWN)
-
G6
+
53F
51F
24F
A12
B12
42F
76F
45F
50F
49F
23F
A11
52F
A11 KEY SWITCH
EMERGENCY
DOWN
BATTERY
-
+
BK
RD
60E
B7
25F
29F
41F
60E
NC
P1
TS66
BN23
CB2
KS1
(UP)
(DOWN)
G6
-
+
51F
25F
24F
A12
B12
76F
A11
B
B1
3
1
4
2
52F
A11 KEY SWITCH
EMERGENCY
DOWN
BATTERY
-
+
29F
41F
60E
BK
RD
60E
B7
53F
(after serial number 48717)
(from serial number 40926 to 48717)
(from serial number 21065 to 40925)
(before serial number 21065)
(B7 not used after
serial number 49199)
ABBREVIATION LEGEND
Item
Description
B7
Auxiliary down battery (GS-3246)
BN23
Auxiliary down button (GS-3246)
CB2
Circuit breaker, 7A
G6
Hour meter
KS1
Key switch
P1
Emergency Stop at ground controls
TS66
Platform up/down toggle switch
800-610-4101
ActionRental.com
Содержание GS-2046
Страница 1: ...Service Manual Part No 72972 September 2006 Rev B2 800 610 4101 ActionRental com ...
Страница 169: ...800 610 4101 ActionRental com ...
Страница 172: ...Electrical Schematic from serial number 17408 to 21064 June 2003 Section 6 Schematics 800 610 4101 ActionRental com ...
Страница 173: ...800 610 4101 ActionRental com ...
Страница 176: ...Electrical Schematic from serial number 21065 to 21262 June 2003 Section 6 Schematics 800 610 4101 ActionRental com ...
Страница 177: ...800 610 4101 ActionRental com ...
Страница 180: ...Electrical Schematic from serial number 21263 to 24438 June 2003 Section 6 Schematics 800 610 4101 ActionRental com ...
Страница 181: ...800 610 4101 ActionRental com ...
Страница 184: ...Electrical Schematic from serial number 24439 to 25141 June 2003 Section 6 Schematics 800 610 4101 ActionRental com ...
Страница 185: ...800 610 4101 ActionRental com ...
Страница 188: ...Electrical Schematic from serial number 25142 to 27181 June 2003 Section 6 Schematics 800 610 4101 ActionRental com ...
Страница 189: ...800 610 4101 ActionRental com ...
Страница 192: ...Electrical Schematic from serial number 27182 to 28936 June 2003 Section 6 Schematics 800 610 4101 ActionRental com ...
Страница 193: ...800 610 4101 ActionRental com ...
Страница 196: ...Electrical Schematic from serial number 28937 to 33721 June 2003 Section 6 Schematics 800 610 4101 ActionRental com ...
Страница 197: ...800 610 4101 ActionRental com ...
Страница 200: ...Electrical Schematic from serial number 33722 to 40925 June 2003 Section 6 Schematics 800 610 4101 ActionRental com ...
Страница 201: ...800 610 4101 ActionRental com ...
Страница 204: ...Electrical Schematic from serial number 40926 to 48054 June 2003 Section 6 Schematics 800 610 4101 ActionRental com ...
Страница 205: ...800 610 4101 ActionRental com ...
Страница 208: ...Electrical Schematic from serial number 48055 to 48717 June 2003 Section 6 Schematics 800 610 4101 ActionRental com ...
Страница 209: ...800 610 4101 ActionRental com ...
Страница 212: ...Electrical Schematic from serial number 48718 to 49199 June 2003 Section 6 Schematics 800 610 4101 ActionRental com ...
Страница 213: ...800 610 4101 ActionRental com ...
Страница 216: ...Electrical Schematic after serial number 49199 June 2003 Section 6 Schematics 800 610 4101 ActionRental com ...
Страница 217: ...Hydraulic Symbols Legend and Component Reference Section 6 Schematics June 2003 800 610 4101 ActionRental com ...
Страница 232: ...Hydraulic Schematic GS 3246 after serial number 36044 June 2003 Section 6 Schematics 800 610 4101 ActionRental com ...
Страница 234: ...Hydraulic Schematic GS 3246 Models with Traction Control June 2003 Section 6 Schematics 800 610 4101 ActionRental com ...
Страница 235: ...Service Manual GS 2046 GS 2646 GS 3246 Part No 72972 Rev B2 800 610 4101 ActionRental com ...