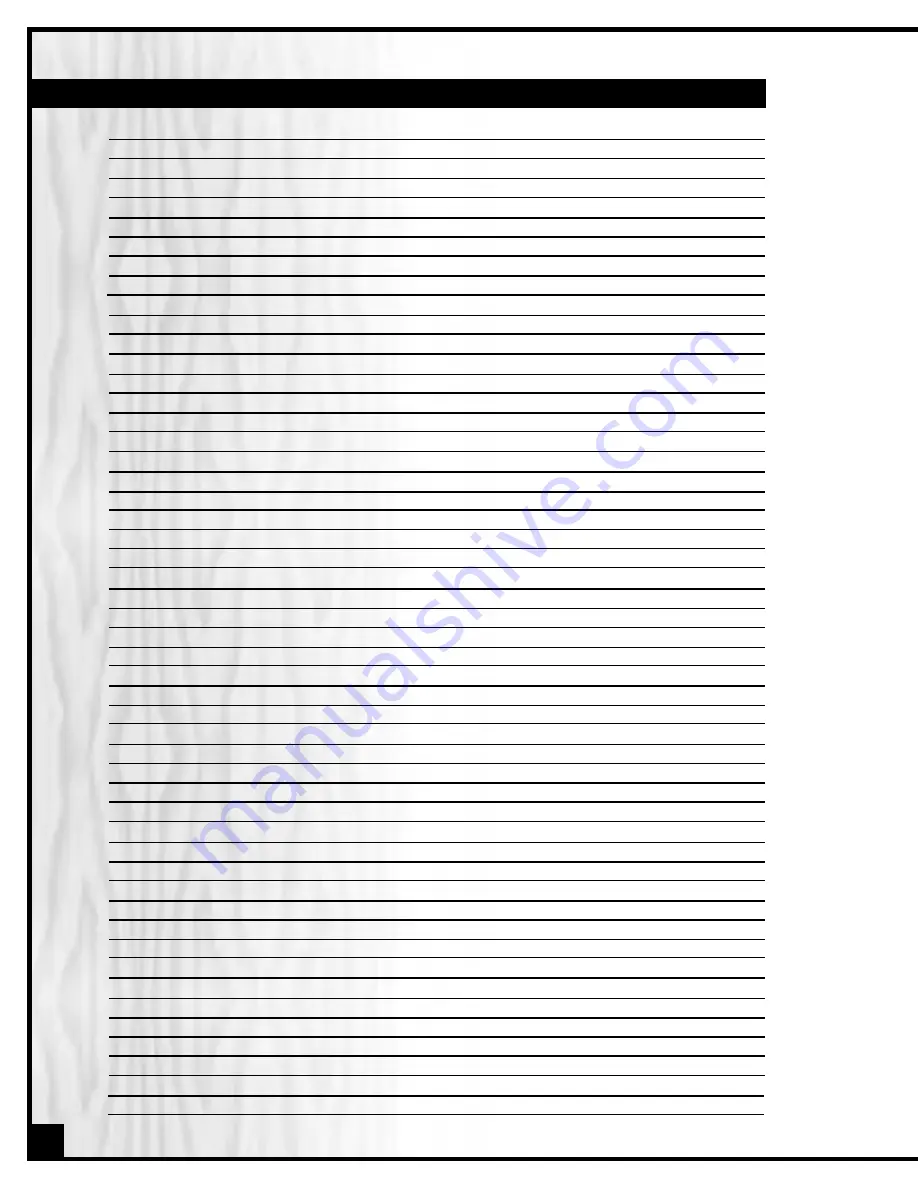
28
PARTS LIST - 15-250 M1
PART N0.
REF N0.
DESCRIPTION
SPECIFICATION
QTY
15250-01
20900001
DRUM
2
15250-02
20703010
TWO-STEP CLAMP
2
15250-03
20703010B
TWO-STEP CLAMP PLATE
2
15250-04
20703010A
SPRING
2
15250-05 20703014A
SPRING
2
15250-06
20703014
FIXED CLAMP BRACKET
2
15250-07
20703014B
FIXED CLAMP PLATE
2
15250-08 20703014C
SPRING
2
15250-09
S0040300
PHILLIPS HEAD SCREW
2
15250-10 S0110300
NUT
3/16"-24UNC
7
15250-11
20900086
RIGHT CLAMP
3
15250-12 20900087
LEFT
CLAMP
3
15250-13 20900069
MICRO-ADJUSTMENT
SPRING
6
15250-14
S0030580M
PHILLIPS HEAD SCREW
6
15250-15 S0120500M
NYLON
NUT
M5X0.8
6
15250-16
20900002
CLAMP BLOCK
2
15250-17
20900003
RIGHT BEARING HOUSING
1
15250-18
20900004
LEFT BEARING HOUSING
1
15250-19
20900005
RIGHT MICRO-ADJUST.BEARING CAP
1
15250-20
20900006
LEFT MICRO-ADJUST.BEARING CAP
1
15250-21
S0020530A
MICRO-ADJUSTMENT SCREW
2
15250-22
S05ETW06
CIRCLIP
E6
8
15250-23
20703002
BEARING CAP
6
15250-24
C1206205
BEARING
6205
4
15250-25
S0060510
CAP SCREW
8
15250-26
S0210500C
FLAT WASHER
38
15250-27
S0230506
LOCK WASHER
5/16"
62
15250-28
S0120500
NUT 5/16"-18UNC
30
15250-29
20900008
DRIVE ROLLER
2
15250-30
S0210532
FLAT WASHER
3/8"X23
2
15250-31
S0020512L
LEFT THREADED SCREW
5/16"-18UNCX1"L
2
15250-32
20900009
CORNER BRACKET
4
15250-33
20900010
FRONT UPPER PANEL
1
15250-34
20900011
DUST HOOD SUPPORT PANEL
1
15250-35 20702019
HINGE
2
15250-36
20900012
DUST HOOD/DRUMS COVER
1
15250-37
20703016
DUST HOOD/DRUMS COVER HANDLE
1
15250-38 S0010502
CAP
SCREW
5/16"-18UNCX3/4"L 18
15250-39 20900070
UPPER
CLASP
1
15250-40 20900071
LOWER
CLASP
1
15250-41 20900068
HINGE
PAD
SS41
2
15250-42
S0030405
PHILLIPS HEAD SCREW
1/4"-20UNC
24
15250-43 S0210401
FLAT
WASHER
1/4"X13X1
41
15250-44
S0110400
NUT
12
15250-45 20900013
PULLEY
GUARD
1
15250-47 S0230400
LOCK
WASHER
1/4"
46
15250-48 20900014
UPPER
BRACKET
2
15250-49 20900015
COLUMN
SUPPORT
BRACKET
2
15250-50 20900016
LOWER
BRACKET
2
15250-51 20900017
WORM
GEAR
2
15250-52 20900018
WORM
2