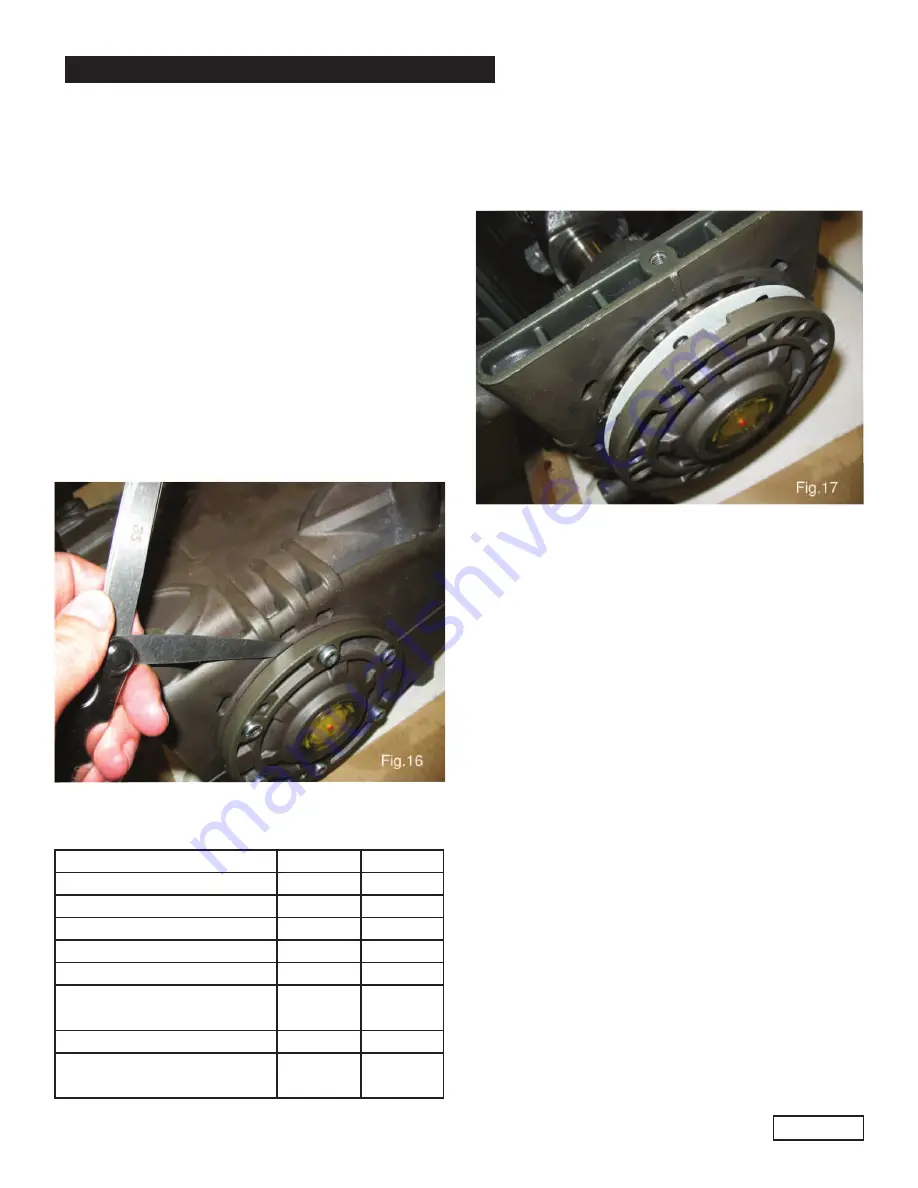
GENERAL PUMP
A member of the Interpump Group
KE SERIES
Page 14
The new roller bearings can be mounted at room
temperature with a press; it is necessary to hold them on
the side surface of the ring nuts with suitable rings. The
driving operation can be facilitated by heating the parts
at a temperature between 250-300oF, making sure that the
ring nuts are correctly fitted in their seats.
Note: Take care not to invert the components of the 2
bearings (outer ring nut of bearing 1 instead of the one of
bearing 2...).
To maintain the right axial load, the shim package has to
be calculated again as follows:
A) Install the crankshaft into the crankcase making sure
that the PTO end comes out on the correct side.
B) Fit the motor side flange on the crankcase with
special attention to the seal lip as indicated on point
11.1.2.
C) Position the sight glass side flange using the 3
screws M6 x 16 until the crankshaft cannot be
turned freely by hand.
D) By means of a thickness gauge (see Fig. 16)
determine the shim set as indicated in the table
below.
Measure
Shim Type # of Pieces
From: 0.05 a: 0.10
From: 1.00 a: 0.20
0.1
1
From: 0.21 a: 0.30
0.1
2
From: 0.31 a: 0.35
0.25
1
From: 0.36 a: 0.45
0.35
1
From: 0.46 a: 0.55
0.35
0.10
1
1
From: 0.56 a: 0.60
0.25
2
From: 0.61 a: 0.70
1.35
0.25
1
1
E)
Fit the shims under the sight glass cover
tightening it on the crankcase with the screws,
checking that the stall torque is between 4 Nm and
6 Nm.
F)
If the torque is correct, connect the rods to the
crankshaft, otherwise, calculate the shims again
as per point “C”.
Ref 300614 Rev.E
05-12