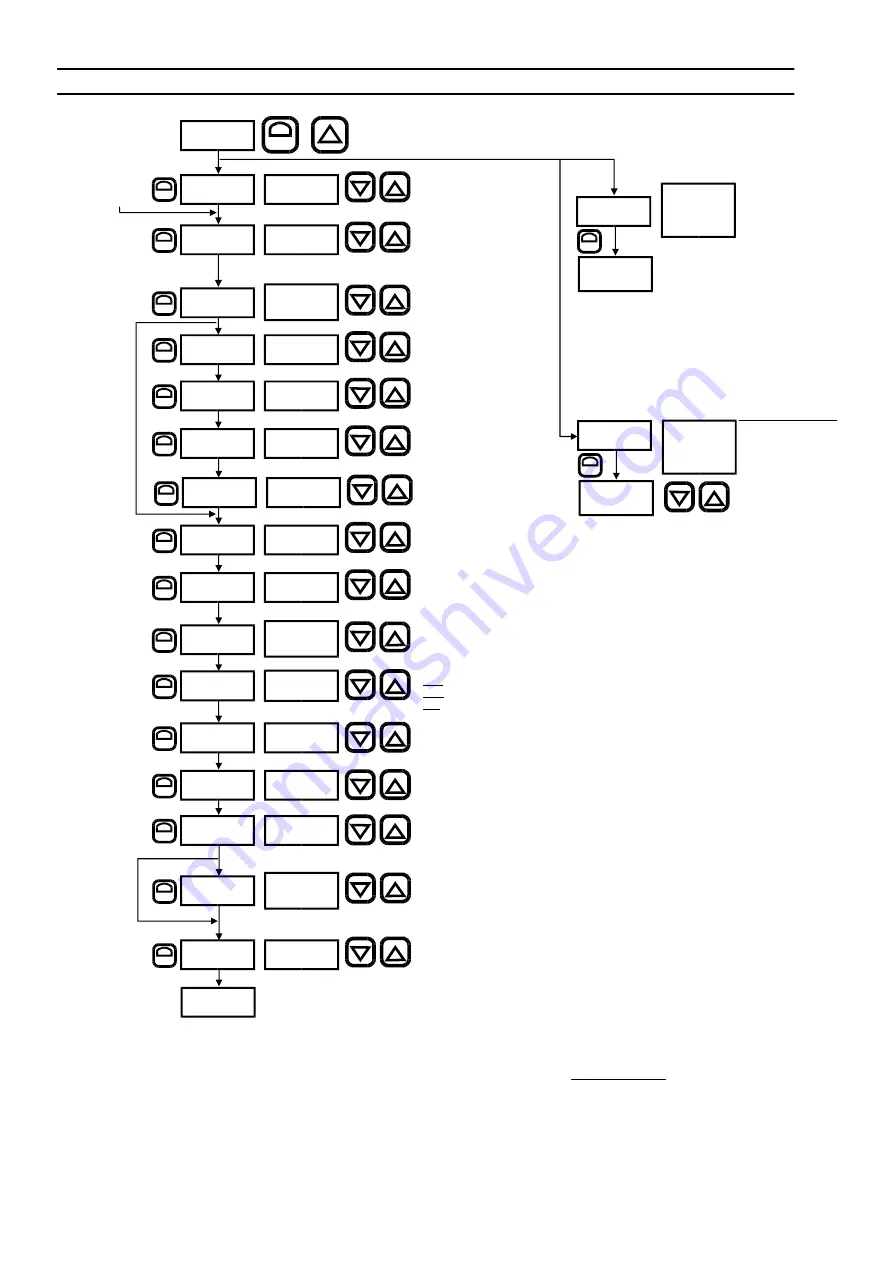
GEMO
PROGRAMMING PARAMETERS
(1) When sensor type is changed, Up.L, Lo.L, H.Set, H.hys, oFFs
Error Messages:
may be set to a new value automatically, according to the selected sensor.
Fail:
Sensor failure or sensor selection wrong
(2) If sensor type is selected as Pt.0, J.0, K.0 or t.0.
E.FLS:
Hardware failure
E.CAL:
Hardware failure
E.EPr:
Memory failure
Gürbüzo
ğ
lu Elektronik San. ve Tic. Ltd.
Ş
ti.
http://www.gemo.com.tr.
Çamlıtepe Cad. No:297 / 3-4 Siteler, Ankara, Türkiye
e-posta: [email protected]
Tel: +90-312-3503900, Fax: +90-312-3511117
3
SET
H.hys
0 .. 50 /
0.0 .. 50.0 (2)
o
C
SET
Heat Hysteresis (
o
C):
PID is active if set to 0
Pb.C
5 .. 150
o
C
SET
Ct
1 .. 200 sec
SET
oFFS
SET
td
SET
+
CodE
Enter 162
SET
UP.L
Lo.L ..
Upper Scale (
o
C)
SET
Upper limit value for Lo.L
and H.SET. Upper Scale
value differs according to
the selected sensor type.
Out
SET
ti
0:00 .. 30:00
min:sec
SET
Inpt
Sensor Type (1)
SET
J, J.0: J type T/C
K, K.0: K type T/C
t, t.0: T type T/C
S: S type T/C
r: R type T/C
Pt, Pt.0: Pt100
Lo.L
Lower Scale ..
UP.L (
o
C)
SET
Lower limit value for UP.L,
H.SET. Lower Scale value
differs according to the selected
sensor type.
P.Err
% 0 .. 100
SET
Determines the duty cycle of OUT output
when “Fail” message is displayed. If 0, OUT is always
OFF. If 100, OUT is always ON, when device “fails”.
Period is Ct.
H.Hys
not 0
Back
Press “Back”
to return to the
top of
parameters
programming
block
Integral Time:
In min:sec If set to 0:00,
P, PD is active (integral OFF).
Derivative Time:
In min:sec. If set to 0:00,
P, PI is active (derivative OFF).
Proportional Band in (
o
C)
Control period (sec)
Offset Value; Offset is directly added
to the measured value. This feature shall
be used for user calibration. Normally set to 0.
Enter 162 to pass
to parameter prog. mode
Press for 2 sec.
Upper Display
rLY, SSr , r-S
Control OUT Type:
rLY: Only Relay is active
SSr: Only SSR is active
r-S: Both Relay and SSR are active at the same time
CodE
Enter “262”
to start
auto-tune
SET
Upper Display
“tunE”
flashes
•
Before starting Auto-tune, adjust H.SET.
•
Process value may exceed H.Set during auto-tuning.
•
After auto-tuning, control form automatically switches
to PID mode.
•
Auto-tuning is stopped (interrupted) any time by
pressing any key. In this case, the parameters before
auto-tuning is valid.
•
Auto-tuning may not always determine the best values
for your process.
Factory SET Values:
H.SEt: 100
o
C
Inpt : J
H.hys: 0
o
C
Pb.C: 30
o
C
Ct: 4 sec
ti: 5:00 min:sec
td: 1:00 min:sec
UP.L: 400
o
C
Lo.L: 0
o
C
oFFS: 0
o
C
Out : r-S
P.Err: 0
C-t: 0.0
o
C / min
L.dSP: yes
o.Sht: oFF
SECU: AH
0:00 .. 10:00
min:sec
-100 .. 100 /
-100.0 .. 100.0 (2)
O
C
C-t
0.0 .. 300.0
o
C / min
SET
If C-t is not 0, ramping starts after power on.
SET value is incremented C-t degrees per minute
until SET reaches H.SEt.
CodE
Enter “555”
for factory
reset
SET
“YES” / “nO”
•
To return to factory settings:
Code > 555 > select “yes” >
Press “SET”
Upper Display
yes: Lower display ON
no: Lower display OFF
SET
L.dSP
yes .. no
End Prog.
o.Sht
OFF, 10.0,
5.0, 3.0,
1.0, 0.2
SET
SECU
H, -
SET
H : “HEAT SET” may be adjusted,
- : “HEAT SET” may NOT be adjusted
Over shoot reduction: All options other than “OFF” may help to reduce over
shoot more but also may increase instability around SET point. For this reason;
First try “OFF” option then 10.0->5.0->3.0->1.0->0.2 options if needed.
Options 1.0 and 0.2 are most sensitive and may result more instability around
SET point among other options. With this parameter, over shoot is not allowed
more than; OFF: not limited, 10.0: 10 , 5.0: 5 , 3.0: 3 , 1.0: 1 , 0.2: 0.2 degrees
(over SET point).
H.Hys
not 0